Introduction to Molecular Sieves
Molecular sieves have increasingly become an integral part of the modern-day industrial purification and separation processes. For instance, the global market for molecular sieves which was valued at US$ 5.1 billion in 2020 will reach beyond US$ 6.8 billion by 2026 (MarketsandMarkets, 2021), emphasizing the importance of these materials in various sectors growth. However, what is a molecular sieve. A molecular sieve is a material that is very spongy and thus since it possesses pores, it is able to adsorb particles, but this time restricting the kinds of particles by their size and polarity. Because of this singular feature, it is possible to separate different gases and liquids. Thus, molecular sieves are essential components in a myriad of industries due to their ability to separate different gases and liquids including that of natural gas cleaning and high purity chemical production.
Chemical Composition and Structure
Zeolites and Their Role in Molecular Sieves
The majority of molecular sieves is composed of synthetic zeolites, which are cubic crystalline materials with a framework of intricate hollow channels. These zeolites, defined by their crystal structure, constitute most of the molecular sieve desiccants due to their particular and advanced adsorption properties. The determination of the relative positions of aluminum, silicon, and oxygen that occurs in the crystalline structure of zeolite, as outlined in its chemical formula, leads to the formation of equally sized pores suitable for filtration of small particles based on molecular size.
Of all the synthetic zeolites available, the variants have different pore dimensions, referring to the pore size of the molecular sieve, and selective adsorption characteristics. Types A, X, and Y are some of the more popular zeolites utilized in the molecular sieve devices. Specialized synthesis modification of the zeolites in design helps enable such zeolites to meet the requirements of different applications. For example, the pore geometry of zeolite type A could be modified depending on the starting Si:Al ratio, and so the firm produces zeolite molecular sieves, 3A, 4A, and 5A.
Pore Sizes and Their Significance
The pore structure of a molecular sieve is by far the most selective mode of distinguishing between different sieves. Pore sizes are values calculated in angstroms (Å) within the range of 3 Å to sometimes 10Å and beyond. Commercial molecular sieves usually are made with individual classes of pore size, these include: 3A (3 Å), 4A (4 Å), 5A (5Å) and 13X (10Å).
Pore sizes of molecular sieves extend from about 3 to10 angstroms (that is ridiculously very tiny – we are talking about billionth of a meter). Different pores are made to interact with certain molecules. Different types of molecular sieves have different pore diameters in order to meet certain requirements such as 3A, 4A, 5A and 13X which are quite popular. For example, 3A molecular Sieve consists of sizes of pores that can absorb water molecules but passé through larger the molecules. As such selectivity helps a great deal in applications such as gas drying or hydrocarbon fractionation. This question could be answered by these pore sizes key in answering how do molecular sieves work in different processes within the industry.
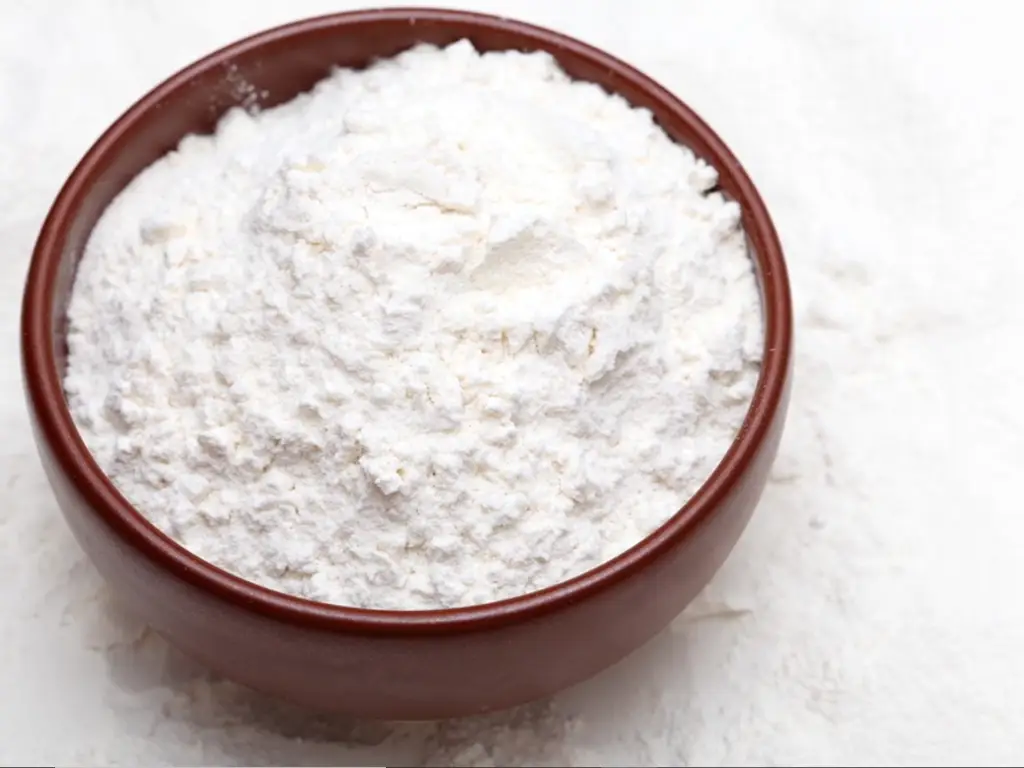
How Molecular Sieves Work
The Mechanism of Adsorption
The beauty of molecular sieves is that they are capable of adsorbing smaller molecules through a mechanism known as physisorption. Chemisorption on the other hand involves the formation of chemical bonds between the molecules and the adsorbent while physisorption involves the use of weak van der Waals forces to attract and hold molecules within the pores of the molecular sieve. In a molecular sieve desiccant, if a gas or liquid stream is passed through it, then the molecules which are smaller than the pore size can enter the pores and get held there. Larger molecules, which cannot enter the pores, just go round the surface. This selective adsorption process enables the molecular sieves to selectively remove impurities, moisture or specific gases from the mixture and produce a purified stream.
Factors Influencing Adsorption Efficiency
The adsorption performance of a molecular sieve is affected by many factors. One of the important factors is temperature; an increase in temperature usually decreases the adsorption although a decrease in temperature increases the adsorption. Pressure, too, is another important factor whereby higher pressures in general increase the rate of adsorption. Adsorption is also influenced by the concentration of the target molecules in the stream. That is, if the concentration is increased, more molecules will be driven into the pores.
The properties of the molecular sieve itself, including the pore dimensions, the surface area and the size of the molecular sieve beads, also affect the efficiency of the adsorption process. The adsorbing surface area is larger in smaller beads, whereas the larger pore does not mean a less efficient molecular measure as the amount of molecules it can capture will be extensive. Improving these aspects in order to obtain a particular degree of purification or separation during industrial applications is significant as well.
Types of Molecular Sieves
Overview of Common Types (3A, 4A, 5A, 13X)
Molecular sieves do not have a universal solution. While the sieves do have many common fundamental properties, their differences warrant different usage for each type. Let’s examine how they are categorized and which ones are the most widely used you will come across. The first one being 3A molecular sieve which has a pore diameter of about 3 angstroms – the smallest of them all. This type is ideal for the dehydration of polar liquids and gases since it has the capability to capture water molecules while larger molecules are quite freely allowed to pass.
This is followed by the 4A and 5A molecular sieves with somewhat larger pore widths. These are workhorses in many industrial applications, able to adsorb more molecules. The 4A type for example is extensively employed in the dehydration of natural gas while the 5A can be used to fractionate normal paraffins from branched and cyclic hydrocarbons. Last but not least is the 13X molecular sieve which is known to have the widest pores among all other commercial types. This has made it easy for it to adsorb large molecules such as carbon dioxide out of gaseous streams. The 13x type of molecular sieves is also extensively applied in air separation processes and can also be used in removing Sulfur compounds from natural gas.
Molecular Sieve Type | Pore Diameter (Å) | Molecules Adsorbed | Common Applications |
3A | 3 | H2O, NH3, He | Drying of polar liquids and gases, purification of helium |
4A | 4 | H2O, CO2, SO2, CH4, C2H6, C2H4, C3H6 | Drying of natural gas, purification of liquid hydrocarbons |
5A | 5 | H2O, CO2, SO2, CH4, C2H6, C2H4, C3H6, C4H8, C4H10 | Separation of normal and branched paraffins, removal of CO2 from natural gas |
13X | 10 | H2O, CO2, SO2, NH3, H2S, C6H6, C7H8, C6H12, C4H10S | Air separation (N2, O2), purification of hydrogen, removal of sulfur compounds from gases |
Carbon Molecular Sieves and Their Applications
Besides zeolite-based molecular sieves, carbon molecular sieves (CMS) have also drawn interest due to their distinctive adsorption features. In contrast with conventional molecular sieve desiccants, which are usually inorganic, the carbon molecular sieves are constructed with carbonaceous substances, for example, coal, coconut shells and polymers. Their pore distribution is more random in nature than that of the zeolites, with pore diameters between few angstrom and a few nanometers.
CMS are also included in many industries such as gas separation, air purification system for volatile organic compounds recovery etc. They are especially useful for separation of nitrogen and oxygen from the air and also for absorption of volatile organic compounds from the emissions of industrial processes. Also, CMS can be utilized in PSA applications for hydrogen purification or CO2 adsorption.
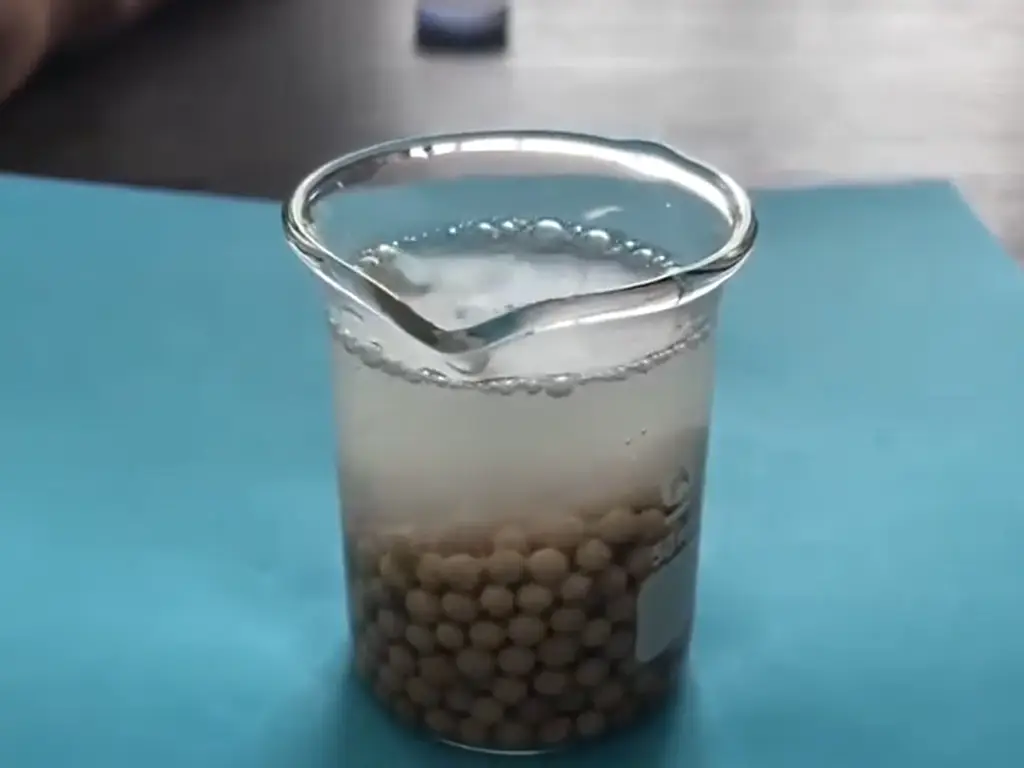
Industrial Applications
Use in Petrochemicals and Gas Purification
One of these various industries is the petroleum industry, and perhaps this is not surprising. These microscopic filters are very effective and efficient when it comes to purifying and separating several gases and liquids in refineries and processing plants. This is especially important in the refining processes, and that is why natural gas has to be treated. Natural gas, when extracted from the well, very often contains unwanted substances such as water vapor and carbon dioxide, contributing to the overall water content. In conjunction with this, molecular sieves for water removal are used to dry the gas, preventing pipeline corrosion and hydrate formation. In the same manner, molecular sieves can also help in the removal of CO2 and metal ions, thus satisfying the specifications of pipelines, maintaining the appropriate relative humidity, and further enhancing the energy content of the gas.
However, this is only the beginning of what can be delivered by molecular sieves. This is also the case for molecular sieves, in that they are employed in high purity hydrogen production that is necessary for many refining processes. The employment of pressure swing adsorption (PSA) systems enabled the addition of molecular sieves that remove impurities, including small molecules, in hydrogen gas to a 99.9%. While producing olefins such as ethylene and propylene, molecular sieves alleviate contaminants that may cause catalyst poisoning in the further stages of the process. The multifunctionality of molecular sieves to tackle various molecule types renders them essential in the industry since petrochemicals are significantly more complicated.
Applications in Pharmaceuticals and Food Industries
Molecular sieves are extensively employed in the pharmaceutical and food industries because there is a greater need to protect quality and safety of the product. In the pharmaceutical industry, molecular sieves are employed in the solvents to dry them, in the raw materials to remove moisture, and to purify the active pharmaceutical ingredients (APIs). Such medicines remain stable and effective since moisture degradation is avoided.
Molecular sieves play a key role in food industries where edible oils need to be dried, impurities such as sugars and syrups need to be treated, and alcoholic products need to be purified. With their assistance, the unsurpassed length of the shelf life of products, better taste of the products, all food protection regulations are met. Also, a molecular sieve desiccant for the packaging of food products controls the moisture level in the package to avoid spoilage of food products.
Selecting the Right Molecular Sieve
Considerations Based on Pore Size and Molecule Type
To effectively make selection of a particular molecular sieve, one must take into account both the pore size and shape of the particular target molecules. Pores of a specific molecular sieve should be designed according to the size of the intended molecules. If the pore size is too small, the targeted molecules will find them too infeasible to get into the sieve and become adsorbed. To the contrary, if the segmentation pores are too large, then segmentation pores will also adsorb undesired molecules which will impact on the efficiency of the separation process. The molecules’ polarity also comes into play when considering which molecular sieve to use. Water and alcohols, which are polar molecules, will tend to take up space in the A-type zeolite more easily than other non-polar adsorbates. Non-polar hydrocarbons will be absorbed better by silicalite or carbon molecular sieves which are structurally linear.
Matching Sieve Types to Industrial Needs
Different sectors use molecular sieves of different types depending on the particular processes and the purities to be achieved. In the petrochemical sector, since the elimination of moisture is imperative, molecular sieve desiccants such as 3A or 4A pore sizes are used. In the case of purification of natural gas, 4A molecular sieves are preferred since they can extract carbon dioxide and hydrogen sulfide. In the case of the pharmaceutical sector, where the drying of solvents is frequently required, 3A sieves are common. For separation of gases like nitrogen or oxygen which are required in pure form, several 13X zeolites are effectively employed. Within the food industry, there may be a need for the use of a combination of more than one molecular sieve types as the use may vary depending on, for instance, 3A for drying oils and 4A for decanting sugars.
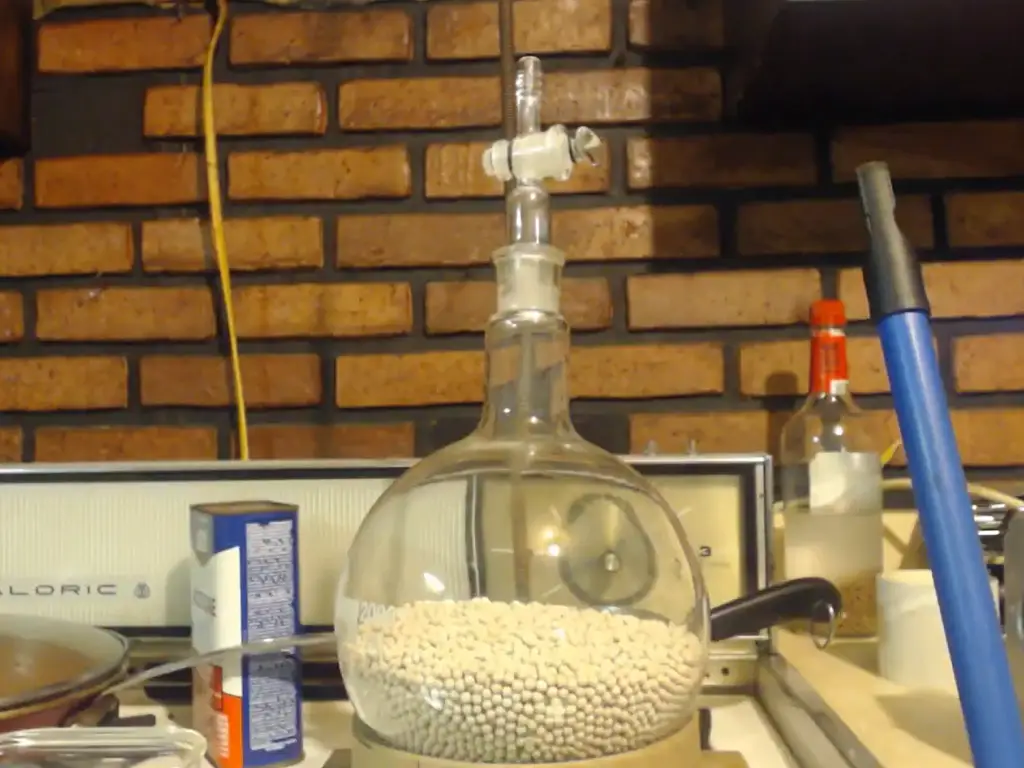
Advantages of Molecular Sieves
High Adsorption Capacity
Perhaps the main disadvantage when it comes to the use of molecular sieves is the high adsorption capacity. It is worth to compare with other absorbents such as silica gel or activated alumina, which therefore adsorb less moisture or target molecules in a given unit mass. This high capacity arises from the porous and high surface area of the adsorbent material.
The high adsorption capacity of molecular sieves has several advantages in any manufacturing purposes. It means that the required level of purification can be attained with lesser amounts of molecular sieve desiccants, hence reducing the material amounts and equipment dimensions Green adsorbent materials therefore will be more efficient Economically whilst the non-thermal processes will ensure minimal damage on the materials. High capacity also means longer periods of operations between regeneration or replacement, thus reducing down time and optimizing the process.
Regeneration and Reusability
Yet another noticeable positive trait of molecular sieves is their capacity to be recovered and employed again. Some adsorbents are used once and thrown away. However, this is not the case with molecular sieves as they can be regenerated by means of heating or pressure swing systems which allows desorption of the adsorbed molecules and enables adsorption capacity recovery.
Thermal regeneration methods involve raising the temperature of the saturated adsorption to over 200 degree Celsius so that the adsorbed molecules are removed. Pressure swing adsorption (PSA) regeneration entails the application of a pressure cycle together with a vacuum cycle on the molecular sieve. Because of this cycling between the adsorption and desorption stages, the molecular sieves can be used over and over again, thus decreasing waste and lowering operating expenses.
Challenges and Solutions
Dealing with Contaminants
Despite the fact that molecular sieves are very efficient in what they are designed to do, they are not invulnerable to problems. One of the biggest challenges is handling of contaminants that may affect the efficiency of the devices in the long run. Some of the molecules such as larger ones or those with high polarity can become strongly adsorbed and hence challenging to desorb during normal regeneration. This can result in a progressive reduction of the sieve’s capacity and effectiveness. At times, the contaminants can also plug the pores and thus deny access to the internal adsorption sites.
Well, how do we deal with this challenge? One of them is the pretreatment of the feed stream to minimize the possibility of the contaminants getting to the molecular sieve. This might include the use of filters or other separation techniques upstream. Another approach is to employ a number of molecular sieves of different types in sequence, each of which is designed to remove certain impurities. It is also possible to monitor the sieve’s performance and determine when more intensive regeneration or replacement is required. In some cases, it is possible to apply specific regeneration methods, including chemical washing or increasing the temperature and holding the sieve for a longer time.
Optimizing Conditions for Maximum Efficiency
Proper use of molecular sieves is not only dependent on their correct selection but on the proper operation of the sieve as well. Factors such as temperature, pressure, flow rate and concentration of the target molecules determine the extent to which each molecular sieve will perform. For example, it is known that high temperatures tend to decrease the adsorption ability, however, this could increase the speed of adsorption and may improve overall performance of dynamic systems.
Reaching these conditions usually requires trade-offs. In pressure swing adsorption systems, for instance, higher working pressure during the adsorption step can also lead to improvement of the system performance because of its capacity with regards to the adsorbate involved in the process. Quite often that is the case where we need to find optimal separation procedure in terms of maximum separation efficiency at lowest operational costs. Usually, this requires that theoretical modeling needs to be combined with practical experiment. Advanced process automation systems allow one to keep the proper working parameters in the industrial processes, changing them depending on the feed composition and desired product in the real-time, and monitoring such changes. As we have been perfecting our knowledge of the behavior of molecular sieves, we have been coming up with more and more options on how to exploit these materials further.
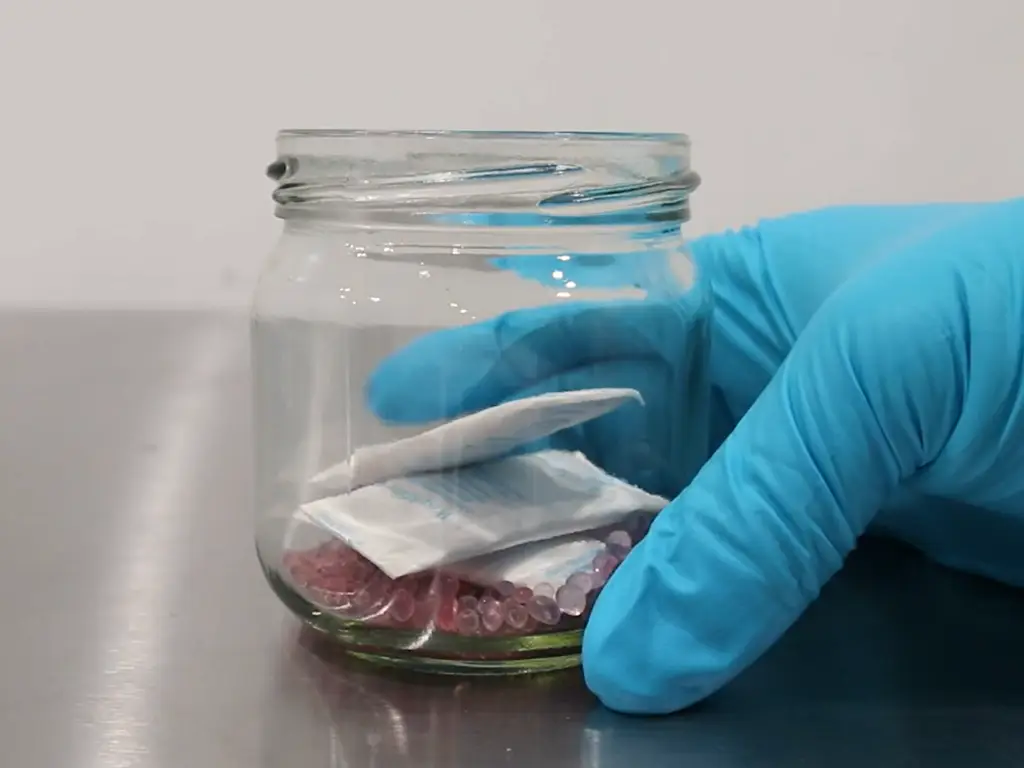
Molecular Sieves vs. Other Desiccants
Comparative Analysis with Silica Gel and Activated Alumina
When it comes to drying gases and liquids, one can be sure that molecular sieves aren’t the only game in town. Other novel and widely used materials used are activated alumina as well as silica gel. So, how do these measure up? Let’s start with those two of a molecular sieve and a silica gel for comparison. Silica Gel is famous for its water retention at higher humidity levels and also for the capacity to be regenerated at low temperatures. It is, however, less expensive than molecular sieves. That is why it is gentler with delicate materials. On the other hand, Molecular sieves have a high degree of water absorption capacity in the first place but can achieve much lower dew points in drying which makes them ideal in most processes requiring almost complete dryness.
However, for activated alumina, this is somewhere between silica gel and molecular sieve. It is better than silica gel but lesser than molecular sieves. One of the strong suits of activated alumina is its potential to remove more than just water. Ion exchange resins are useful in situations where removal of more than one type of impurity is required. While it is clear that activated alumina has its limitations and disadvantages in terms of the moisture content of the ambient air and in separating molecules of different sizes, this is however, where molecular sieves will come in.
Conclusion
To sum up molecular sieves can be regarded as amazing materials which have changed many industries due to their selective adsorption characteristics. Within the complex structures of the zeolites and a variety of pore sizes, molecular sieve desiccants provide a strong means of drying, cleaning, and separating.
Grasping the basic principles of molecular sieves, including their chemical composition and the basics on how to improve their use in industry is an important activity. This requires the use of the appropriate variety of molecular sieve, the shape and size of the pores, and such molecules to be fit into a particular industrial application for effectiveness.