Introduction to Crude Oil Separation
Crude oil, or ‘black gold’, is a flammable liquid, a complex mixture of hydrocarbons found in the earth’s crust and sourced from oil wells just like gold from a Gold mine. This is the source of a variety of essential products which are used in day-to-day life such as petrol, diesel, plastics, etc. But crude oil in its unprocessed form is of little use and it undergoes different separations according to different boiling points and molecular weights of its constituents. This separation is important since it enables the concentration and purification of the individual portions of crude oil that are of interest to different industries.
A process that involves breaking down crude oil into different components is called as oil refining. There are different separation processes that can be used in oil refining and each of them has its own strengths as well as areas of use. These comprise solvent extraction that separates constituents according to their chemical characteristics; membrane separation, which is currently a more advanced technique for selective separation of molecules; filtration that eliminates solids from the crude oil; molecular sieves in adsorption separation matrix; and the primary one, fractional distillation that is responsible for the separation of hydrocarbons based on their boiling points. Also, there are conversion processes like cracking and reforming, which cause further enhancement of separation and increase the quality of the end products.
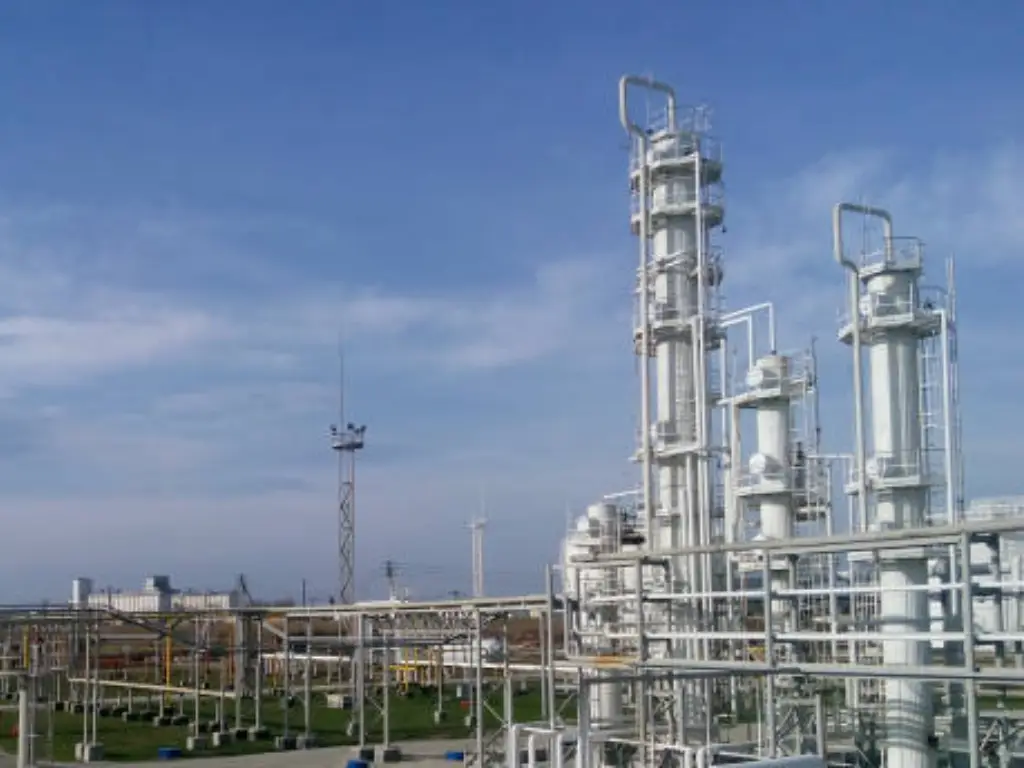
Overview of Key Crude Oil Separation Techniques
Solvent Extraction: Separating Components Through Chemical Affinity
This is a method that distinguishes crude oil components based on their chemical affinity with other compounds. In this, solvent is added to the crude oil mixture with an expectation that certain components will dissolve while others will not. The components that dissolve in the solvent can be separated in distillation or evaporation process. This technique is suitable for removing aromatic compounds like benzene and toluene which are present in crude oil mixtures of hydrocarbons.
Membrane Separation: Modern Methods for Selective Molecular Separation
Membrane Separation is a modern technique that has recently become widely used due to its ability to separate molecules of different geometry in size and their chemical structure. In this process, the crude oil mixture is passed through a semi-permeable membrane with pores smaller than a certain size that prevents the passage of other molecules. This technique is extremely effective and has broad applications as it can be used to isolate components in a wide range of sizes from small gas molecules to larger organic compounds. Membrane separation is particularly effective in the removal of contaminants including sulfur containing compounds and heavy metals from crude oil.
The Role of Filtration in Removing Solids from Crude Oil
Filtration can be referred as an essential unit operation for the separation of crude oil on the grounds of any solid components and contaminants. In this method, the crude oil is passed through a filter medium such as sand or cloth that captures the solid particles while allowing the liquids to flow through. This process can also be regarded as a pre-treatment process to safeguard the pump used in the further separation processes like the fractional distillation that can treat the liquid crude.
Adsorption Separation: Molecular Sieves and Its Applications
Adsorption and molecular sieves
Adsorption may be described as a separation process where certain materials have the capacity to attract and bind specific molecules. In this instance, when referring to the separation of crude oil, molecular sieves are also referred to as adsorbents. These are materials that possess interconnected pores of nearly equal diameters, which permit adsorption to take place selectively on the basis of molecular size and shape. For instance, molecular sieves are very useful in removing water and other small impurities from crude oil since these molecules are small enough to be contained in the pore of the sieve whereas larger hydrocarbon molecules can be excluded.
How Molecular Sieves Aid in the Removal of Water and Impurities from Hydrocarbon Streams
Crude oil is not a pure substance and often contains water and other impurities. This is particularly paramount since these impurities can result in corrosion, catalyst poisoning, and poor product yield during the refining phase. Molecular sieves solve this problem easily and efficiently. Here, the crude oil has first been depolarized and then dried before it is passed through a column filled with molecular sieves which have a relatively high oil adsorbent capacity. As such, smaller particles are absorbed within the material’s pores leaving only a clean hydrocarbon product. This technique is called dehydration, and it is one of the crucial steps involved in the treatment of crude oil for further processing. The International Association of Oil & Gas Producers indicates that the incorporation of molecular sieves filters allows reducing water in crude oil from 1000 up to less than 1 ppm (bars); hence the safety of the entire downstream processes is enhanced.
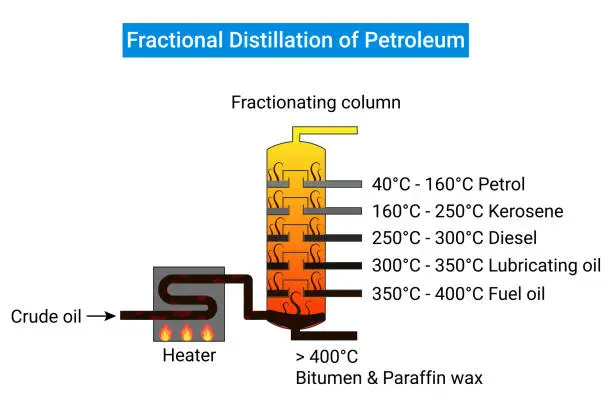
Fractional Distillation: The Core Method for Crude Oil Separation
The Basics of Fractional Distillation
Crude oil, which consists of a heterogeneous mixture of hydrocarbons, can be physically separated into several fractions through a process called fractional distillation. In its simplest form, distillation utilizes the differences in boiling points between different hydrocarbons within the crude oil mixture. The crude oil mixture is ordinarily contained within a fractional distillation column, also known as a fractionating column. To obtain the desired fractions, the crude oil would have to first be heated to the point that it becomes a vapor. As the vapors rise through the column, they cool and condense at different heights, depending on their boiling points. The vapors of the mildest fraction evaporators such as gasoline and liquid petroleum gas (LPG) will come to the apex of the column. Others, like diesel and lubricating oil fractions, gather toward the lower section of the column.
How Fractional Distillation Separates Hydrocarbon Fractions Based on Boiling Points
The crude oil distillation practice is based on the principle of various hydrocarbons having different boiling points. When the temperature in the fractionating column is raised gradually, the lightest hydrocarbons, and those with the lowest boiling points, start to vaporize and rise to the top of the distillation tower. As they rise, they cool and condense on trays or packing materials, which provide a large surface area for the various components to interact with. The condensed liquid then move down the column while the rest of the vapors keep rising. This is accomplished on various levels of the column with each tray or packing material having its own temperature and boiling point range. By the time vapors escape the top of the column, leftovers only lightest hydrocarbons and rest have already been condensed and separated at lower parts of the column, with the components with the highest boiling points remaining at the bottom of the distillation tower.
The Role of Fractional Distillation in Refining Light, Medium, and Heavy Fractions
The importance of fractional distillation in the petroleum industry is very high as this process helps to divide the crude oil into its constituents- light, medium, heavy and its fractions are characterized to be useful in different sectors. Gasoline and naphtha are light fractions which are very low in boiling points and are majorly used as fuels for engines and other petrochemical processes. Kerosine and diesel fuel are medium fractions with an intermediate volatile rate and find their uses in heating, as jet fuel, and road transport. The heavy gas oils and residuals are the heaviest fractions and are the least volatile and most of the time, they are processed underneath to make lubricating oils, waxes, and asphalt. The U. S. Energy Information Administration has reported that a typical barrel of crude oil can produce approximately 20% of gasoline and 15% of diesel fuel oil while 5 percent is heavy fuel oil and the balance of the 60 percent applies to other products or further distillation.
Enhancing Fractional Distillation Efficiency with Molecular Sieves
Molecular sieves can also be employed to enhance the efficiency and product quality of the fractional distillation process. Although the distillation process separates hydrocarbons based on their boiling points, some of the resulting fractions may still contain impurities that can negatively impact the quality of the final products. By incorporating molecular sieves with specific pore sizes into the distillation system, these impurities can be selectively removed, ensuring that each fraction meets the required purity standards. For instance, molecular sieves can be used to remove sulfur compounds, nitrogen compounds, and other contaminants from the distillate fractions, thereby improving the quality of the products and protecting downstream catalysts and equipment from damage. This integration of molecular sieve technology into the fractional distillation process demonstrates how various separation techniques can work together to optimize the overall crude oil refining process.
Impurity | Concentration Before Treatment (ppm) | Concentration After Treatment with Molecular Sieves (ppm) |
Water | 500-1000 | < 1 |
Hydrogen Sulfide (H2S) | 50-100 | < 0.1 |
Mercaptans (RSH) | 100-500 | < 1 |
Nitrogen Compounds | 100-500 | < 1 |
Oxygenates | 50-100 | < 1 |
Carbon Dioxide (CO2) | 500-1000 | < 10 |
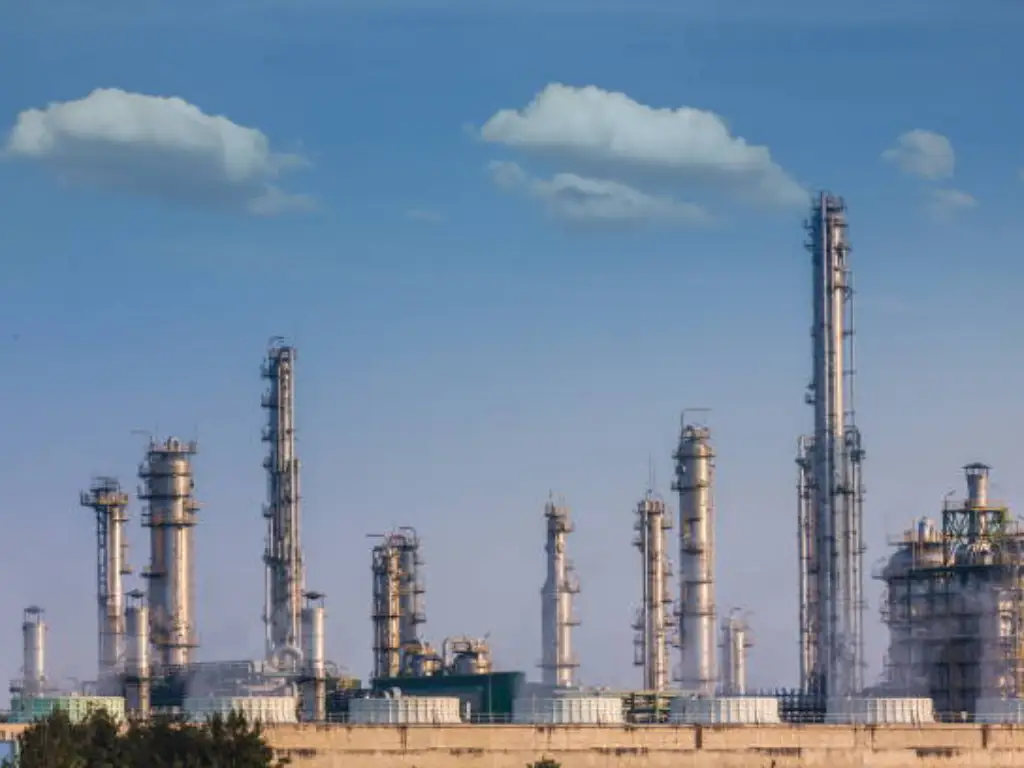
Conversion Processes: Enhancing Separation Efficiency After Initial Distillation
Cracking: Breaking Down Heavy Fractions into Lighter, More Valuable Products
Post the initial fractional distillation, higher fractions of the crude oil still remain as non-burnable statuses or feedstocks for petrochemicals. To improve the output of light and high-value products, these heavy fractions may be subjected to a process known as cracking. Cracking refers to the rupture of heavy fractions associated with large complicated hydrocarbon molecules into the simpler molecular parts which can act as fuels or chemical intermediates. There are two principal ways of doing cracking: the first consists in the use of high temperature to heat the carbon bonds, thermal cracking, while the other employs the use of a catalyst that reduces energy for the reaction, catalytic cracking. Cracking is an integral stage for which it maximizes the worth of crude oil and in addition guarantees most of the resource is put to good use.
Reforming: Rearranging Hydrocarbon Molecules to Improve Fuel Quality
Reforming is redefining processes with structural changes in chemical composition to enhance the gasoline and other fuels which provide utility in transportation via oil refining industry. Rearrangement of hydrocarbons in this process is carried out with an objective of increasing the molecular weight and octane value which is an index of fuel’s ability to withstand knocking in an engine. Rhodesias include the use of a catalyst like Platinum or Rhenium to obtain the chemical reactions. Because of an increasing octane rating of gasoline, reforming makes it user-friendly to high-purposive engines to make sure that the fuel used burns effectively and cleanly. This process is significant today when more focus is on the fuel quality than ever before.
The Importance of Secondary Treatments After Separation
Desulfurization: Removing Sulfur Compounds to Meet Environmental Standards
The presence of Sulphur compounds as impurities in crude oil is a concern because in the course of usage of oil as a fuel burnt these compounds leads to several environmental as well as health issues. To mitigate this, oil refineries include desulphurisation techniques in which such compounds are eliminated from the different fractions obtained from the separation process. Desulphurisation is often done with the addition of catalyst mixtures such as cobalt and molybdenum that convert sulphur containing compounds to hydrogen sulphide gas that can be easily further cleaned, changing it into sulphur. This process is necessary because national and international regulations require minimum sulphur content in oil and its derivatives, which are aimed at protecting the environment. An example in the US, the Environmental Protection Agency has restricted diesel fuel that is made for on road use to 15 parts per million sulphur from the previous wall of 500 parts per million.
Treating Heavy Residues: Vacuum Distillation and Coking to Further Process Heavy Fractions
The bottom of oil is not made use of in fuels or petrochemical feedstocks even after the processes of fractional distillation and conversion. Oil refineries in an attempt to recover more value from these residues, apply secondary treatment processes like vacuum distillation and coking. On vacuum distillation, heavy residues are boiled off at lower pressures, rotating higher boiling points of different components for better separation efficiency. Coking on the other hand is a thermal cracking, types of thermal cracking, but instead of isolating its fractions from each other, coking decomposes the heavy residues converting them into light hydrocarbons and a solid, carbon rich residue called coke. Fuel coke has numerous other industrial applications such as steelworks and power generation. Thus, with such added processes were performed on the residues, refiners manage to maximize the value from each barrel of crude oil and ensure that no waste is left useless.
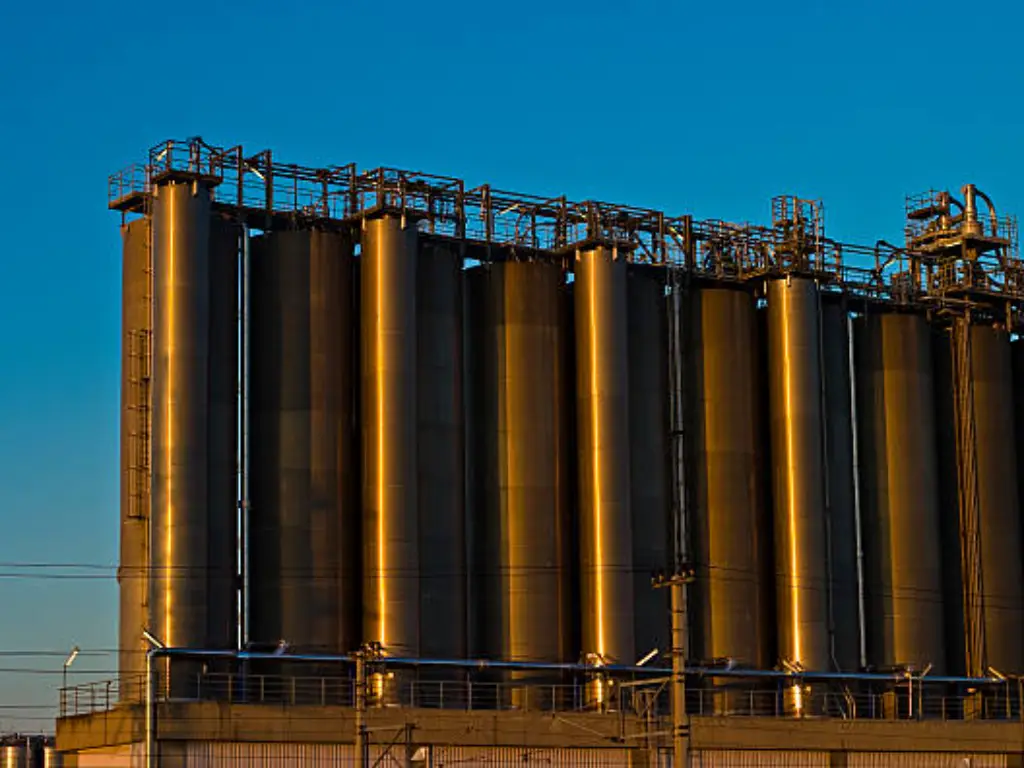
Environmental and Efficiency Considerations in Crude Oil Separation
Sustainability and environmental protection tend to be important principles in contemporary society and, consequently, the oil refining industry faces numerous challenges in achieving more efficiency in its processes which are also less harmful to the environment. One of the branches of interest is cutting the energy and greenhouse gases which are emitted in the process of crude oil separation. Among several options, it is the implementation of waste heat recovery through integrating different processes, replacing equipment with more energy-efficient ones, and potentially using renewable energy for the refinery processes. It is also increasing concern to shift towards practicing and applying methods to cut the environmental footprint of refinery emissions such as Flue gas pollution control by advanced scrubbing systems and industrial waste treatment before its discharge. Therefore, the same kind of approach can also be applied to the performance of the crude oil separation process and help move towards the goal of a cleaner and greener planet. The positive effects that result from improvements in the crude oil separation process make an important contribution to the overall cost of a particular oil refining unit.
Enhancing Refinery Efficiency with Jalon’s Expertise
If you require molecular sieves for the separation and refining processes of crude oil, teaming up with a qualified manufacturer such as Jalon is likely to be a rational approach. Being in the profession for a substantial period, Jalon has the ability to develop different types of customized molecular sieve solutions for the petroleum industry. By teaming up with Jalon, you will take advantage of their experience and modern technology so that the best possible performance will be achieved in their oil refining activities.
Conclusion
To conclude, the deconstruction of crude oil into its constituent parts varies in genres; its genres include but are not limited to: fractional distillation, solvent extraction, membrane separation, filtration, and adsorption. These strategies are helpful in separating the complicated assortment of hydrocarbons from crude oil and transforming them into useful products that are virtually indispensable in today’s civilization. The principal method for Crude oil separation is fractional distillation and it classifies the hydrocarbons according to their boiling substances; other methods such as solvent extraction and membrane separation enhance and purify the final products. With the world’s energy and petroleum-based products requirements ever increasing, it becomes imperative for the oil refining industry to continually improve those separation processes to be more effective whilst minimizing the potential environmental hazards.