What is CO2 Recovery and Why It Matters Now?
In its essence, CO2 recovery is the process of capturing carbon dioxide from industrial emissions before it is released into the environment. While the greenhouse effect is a major problem, recovery technologies are designed to take CO2 and turn it into a useful product. This is not just the act of being an environmentalist; it is a business strategy in a world that is experiencing climate change.
This task is especially important due to the growing problem of global warming that threatens the planet. Science tells us that if left unabated, CO2 levels are the root cause of climate change, which leads to increased frequency and intensity of natural disasters, rising sea levels, and species extinction. Businesses, the engines of our economies, are also major contributors to these emissions. Industrial CO2 recovery is, therefore, not only the right thing to do, but the smart thing to do for the future, in compliance with the international agreements and as a path towards a carbon-free industrial sector.
Key Industrial CO2 Recovery Technologies Explained
The realm of industrial CO2 recovery offers a suite of technologies, each a distinct approach to capturing carbon. Understanding their nuances is key for industries aiming to curtail their carbon footprint.
Chemical Absorption
Chemical absorption is one of the oldest methods of capturing CO2 and it operates like a chemical embrace that pulls in carbon dioxide molecules. This conventional method uses selective solvents which are usually solutions containing amines that are specifically chosen to react and form a chemical bond with CO2 in industrial gas streams. The simplicity of this process is that the solvent is exposed to CO2 and then heated and the carbon dioxide is released in a concentrated form and in a form that can be used for other purposes or be disposed off. The solvent is then ready to be recycled back to the absorption cycle without the presence of CO2 and is intended to be a closed system that can be operated on a continuous basis with minimal losses. Chemical absorption has been widely used and has been proved to be flexible in handling different composition of the gas and therefore is the most widely used method in industries that emit high levels of CO2.
However, chemical absorption has some operational factors that affect its efficiency in the process. The cost of the energy expenditure required to regenerate the solvent – to liberate the captured CO2 and restore the solvent’s absorptive capacity- is a another operational cost which can turn out to be the major in the process. In addition, the chemical solvents are not permanent; they get exhausted with each cycle and need replacement and disposal which is expensive and affects the environment. However, chemical absorption remains a popular technology to this date, especially in large scale power generation and core industrial processes where high concentration of CO2 is present and requires efficient capture technologies as the search for better and environmentally friendly technologies goes on.

Membrane Separation
Membrane separation technology is a relatively efficient and flexible approach to CO2 recovery that uses specific membranes to filter out carbon dioxide. These are usually made from advanced polymers or robust ceramics and are designed to have a higher permeability for CO2 than other gaseous components in an industrial mixture. The attractiveness of membrane separation lies in the fact that it is less energy-intensive compared to other methods, it is easily scalable and can be easily integrated into existing industrial systems without much interference. This places membrane technology as a more viable solution for industries that want to reduce their energy consumption and make the application of carbon capture technologies more feasible.
However, it is still difficult to achieve CO2 capture efficiencies that are comparable to those of chemical absorption or adsorption based techniques especially when faced with low concentration or high volumetric flow rate gas streams. Also, the presence of impurities in the feed gas stream can cause membrane fouling which in turn affects the CO2 permeation rate and the overall efficiency and durability of the membrane. Despite these ongoing challenges, membrane separation is steadily establishing its niche in specific applications such as natural gas processing, hydrogen purification, and targeted industrial sectors where its inherent energy efficiency and operational simplicity offer compelling advantages, especially as material science continues to push the boundaries of membrane performance and durability, promising a future where membranes play an increasingly prominent role in the landscape of CO2 capture technologies.
Temperature Swing Adsorption (TSA)
TSA is a highly advanced CO2 recovery technique that utilizes temperature changes to selectively adsorb and desorb CO2 from various industrial gas streams. TSA systems work in cycles, using adsorbent materials, and molecular sieve adsorbents are preferred because of their properties to capture CO2 at low temperatures and release it at high temperatures. TSA technology has been applied in a wide variety of industrial processes, including the removal of flue gases from power plants and other industrial facilities that seek to reduce emissions, the upgrading of biogas to increase the proportion of methane for greater fuel value, and in the relatively new field of direct air capture (DAC) where CO2 is captured from the low concentrations present in the atmosphere. The inherent features of TSA such as the high selectivity of CO2 over other gas components and the long-term stability of many adsorbent materials especially the molecular sieves are some of the factors that have made TSA to be widely used and relevant in these diverse and challenging applications.
However, the operational environment of TSA technology is not without its problems. The main issue is the high thermal energy consumption for regeneration of the adsorbent, particularly the heating step necessary to release the captured CO2 and restore the adsorbent for the next cycles. This thermal energy consumption can have a significant impact on the energy utilization and the cost effectiveness of TSA systems especially in industries where energy costs are a major consideration. Although there is still a challenge in this energy consideration, which is being met by constant development in the molecular sieve adsorbent technology. The enhancement of the CO2 adsorption capacities of the advanced molecular sieves and, importantly, the desorption kinetics at lower temperatures are gradually enhancing the energy balance and the economic feasibility of TSA.
Pressure Swing Adsorption (PSA)
Pressure Swing Adsorption (PSA) is a highly efficient and energy-saving development of physical adsorption, which skillfully uses pressure fluctuations to facilitate the continuous adsorption and desorption of CO2. PSA systems operate in a continuous manner of high pressure adsorption and low pressure desorption and usually involve the use of several adsorbent beds to ensure that there is a steady flow of captured CO2. This technology is most valued for its inherent energy-savings, especially when compared to energy-intensive technologies such as chemical absorption, and for its ability to deliver CO2 streams of very high purity, making it ideal for processes that require concentrated CO2 feed. The performance envelope of PSA systems is further extended through the incorporation of advanced adsorbent materials and molecular sieves play a crucial role in increasing the selectivity and efficiency of the capture process.
Although PSA technology offers a range of benefits, the successful application and long-term operation require the consideration of several factors. The cost of purchasing high-performance adsorbent materials, especially the molecular sieves that are specifically developed for the capture of CO2, may be expensive to acquire at the initial stage. In addition, PSA systems can be sensitive to the level of impurities in the incoming gas stream, which can cause gradual fouling of the adsorbent and a consequent decline in capture efficiency over time, which is why it is crucial to pre-treat the gas stream. However, its applications are extending to the areas like hydrogen production, biogas upgrading to pipeline quality, and with growing pace, post combustion CO2 capture from power plants and industrial sources due to the rising need for efficient and high purity CO2 recovery.
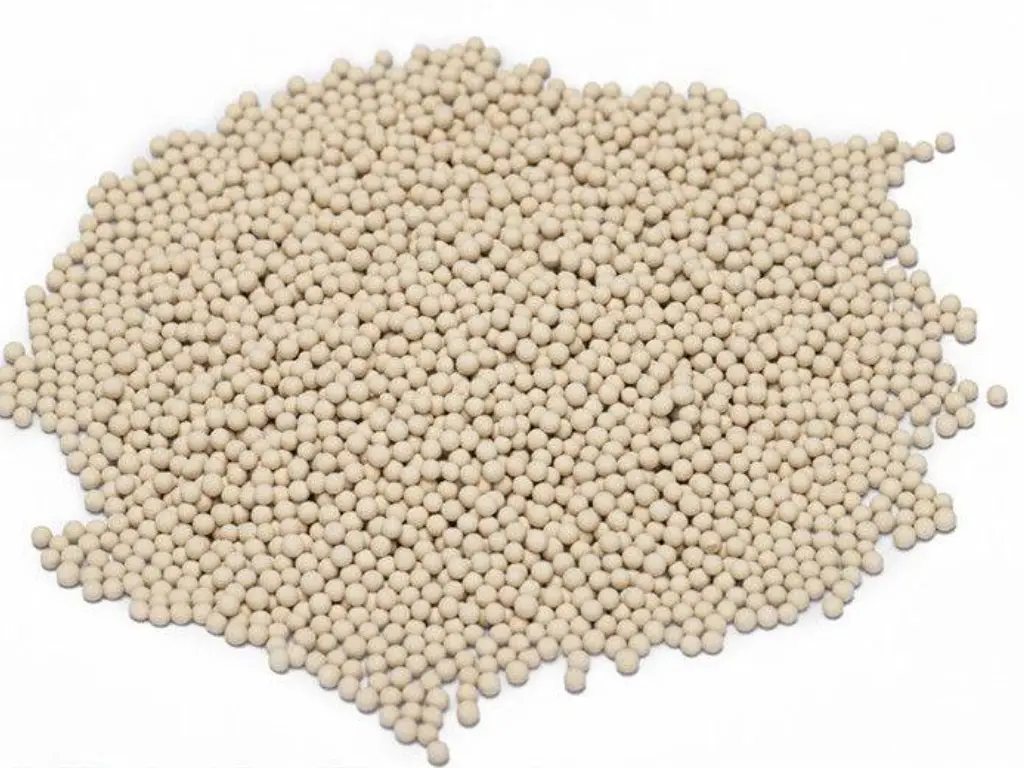
Cryogenic Separation
Cryogenic separation is a technology that is based on cryogenics and uses the force of low temperatures to effectively separate CO2 from gaseous streams. It is like a sub-zero distillation process where the industrial gas streams are cooled to very low temperatures so that the various components of the gas can be separated based on their boiling points. CO2, which has a higher condensation temperature compared to other industrial gases such as nitrogen and methane, can easily be condensed and separated in the liquid state from other gaseous components. This cryogenic approach is particularly effective in its ability to produce CO2 streams of high purity, which is a desirable feature for certain industrial applications where high purity of CO2 is mandatory, for example in the production of food grade CO2 for use in the beverage industry or as a high purity reagent in specific chemical synthesis processes.
The application of cryogenic separation for large-scale CO2 capture is limited by several challenges, which include high costs and operational issues, mainly due to the high energy demand and the need for extensive and costly equipment. The process of cooling large volumes of gases to cryogenic temperatures requires a significant amount of energy, making it relatively less energy efficient for CO2 capture especially when applied at large scale in industries that deal with dilute sources of CO2. The equipment required for cryogenic operation such as high pressure compressor, cryogenic expander and complex heat exchanger required for low temperature operation adds to the capital cost. Molecular sieves may also be a significant capital cost, but they can be useful in improving the efficiency of cryogenic CO2 removal systems. This is because by using molecular sieves to remove even the smallest amount of water vapor and other condensable impurities from the incoming gas stream, operators can avoid the formation of ice and solid hydrates within the cryogenic unit, which can cause operational problems and loss of efficiency. However, the use of molecular sieves prior to the cryogenic separation unit makes the process more efficient, less problematic, and less costly, thus demonstrating the applicability and compatibility of molecular sieve adsorbents in other CO2 capture technologies that are not necessarily adsorption-based.
Molecular Sieves for Industrial CO2 Recovery
- 13X Molecular Sieves: These sieves have a pore size of about 10Å and are effective in adsorbing both CO₂ and H₂O. This makes them suitable for uses such as natural gas purification and air separation, which removes both moisture and carbon dioxide. They are also utilized in flue gas decarbonization processes to capture CO2 emissions.
- 5A Molecular Sieves: These sieves have a pore size of 5Å and are ideal for selective adsorption of CO₂. They are mainly used in Pressure Swing Adsorption (PSA) systems where they selectively remove CO₂ from gas mixtures by size and adsorption selectivity to produce high purity CO₂.
- 4A Molecular Sieves: These are mainly used for the removal of moisture because of their pore size of 4Å but they can also adsorb CO₂ under certain circumstances. Although they are not as selective for CO2 as 5A or 13X zeolites, they are used in some CO2 capture applications where the removal of water vapor is also necessary.
- Modified Molecular Sieves (NaX, LiX): These modified zeolites, such as NaX and LiX, undergo ion exchange to enhance their CO₂ adsorption capabilities. This modification, often involving lithium ions, results in significantly improved CO2 capture capacity, making them highly effective in advanced PSA and TSA technologies for efficient CO2 recovery.
Other materials that have been considered for CO₂ capture and separation in the recent past include carbon molecular sieves (CMS) and metal organic framework (MOF) materials, but the current industrial applications are still dominated by the 13X molecular sieves.
Molecular Sieve Adsorbents: Jalon’s Expertise
In the case of physical adsorption CO2 recovery, especially in PSA and TSA, the adsorbent plays a crucial role. Jalon, a well-known molecular sieve manufacturer, is outstanding here. Jalon has been in the business for more than two decades and is a reliable manufacturer of molecular sieves, ranging from 3A and 4A for dehydration to 5A, 13X and LiX for CO2 capture. They are not just mere suppliers; they are strategic allies, providing customized services and a diverse portfolio, proving their versatility.
Jalon’s LiX, 13X, 5A, and 4A molecular sieves are designed to provide the best CO2 recovery and have high adsorption capacity and selectivity. Being one of the leading producers of these key CO2 capture materials, Jalon uses its R&D and application experience to offer the appropriate molecular sieve for various industrial CO2 capture processes. Selecting Jalon means working with a company that offers dedicated knowledge and a range of products focused on the efficiency of your CO2 capture systems.
For more information:
- Phone: +86-186 3889 5089/+86-379-6989 5719
- Email: info@jalonzeolite.com
- Address: Junmin Road, Industrial Cluster District, Yanshi, Henan, China.
-scaled.webp)
CO2 Recovery Applications Across Industries
CO 2 recovery is not a universal process. Its application varies significantly across industries, driven by specific emission profiles, operational needs, and economic considerations. Here is a brief look at some of the industries where carbon dioxide is collected:
Industry | CO2 Emission Source | CO2 Recovery Application | Value Proposition |
Brewery Industry | Fermentation process | Capture and purification of CO2 from fermentation for reuse in carbonation and packaging. | Cost savings by reducing CO2 purchase, ensuring CO2 supply security, enhancing sustainability profile. |
Food & Beverage Industry | Various processes, including food production and packaging | Supply of food-grade CO2 for carbonation, modified atmosphere packaging, and other applications. | Reliable and sustainable CO2 source, reduced reliance on external CO2 markets, potential for revenue generation. |
Refining & Chemical Industry | Hydrogen production, process heating, and chemical reactions | Feedstock for chemical synthesis (e.g., methanol, synthetic fuels), enhanced oil recovery (EOR). | Reduced greenhouse gas emissions, creation of valuable products, potential for enhanced resource utilization. |
Dry Ice Production | Flash evaporation of liquid CO2 | Recovery of CO2 flash gas for reuse in dry ice production, minimizing CO2 loss. | Increased CO2 utilization efficiency, reduced CO2 emissions, lower operating costs. |
Other Industrial Flue Gas | Combustion processes in power plants, cement plants, steel mills | Post-combustion CO2 capture for utilization or geological storage. | Significant reduction in industrial carbon footprint, contribution to climate change mitigation efforts. |
Benefits of CO2 Recovery
Reduced Production Costs
The use of CO2 recovery systems is one of the best ways of realizing cost savings in industrial processes. For companies that utilize CO2 as a feedstock, capturing and recycling the emitted CO2 is economically viable since the companies do not have to buy the gas. Furthermore, the integration of energy recovery technologies with CO2 capture can result in extra benefits in terms of energy requirements and hence, cost. This effect on the raw material and energy sources makes the recovery of CO2 not only a sustainable practice but also a profitable and cost effective business model for industries that seek to maximize their profits.
Environmental Protection
The role of CO2 recovery in the present day conservation of the environment cannot be overemphasized. In this way, industries play a role in decreasing the amount of CO2 released into the atmosphere and combating climate change. This approach is effective in reducing greenhouse gas emissions and therefore their overall carbon footprint and aligning their operations with more and more crucial global environmental goals. CO2 recovery is not anymore an activity that a company can perform as an extra, but it is an activity that has become a part of the industrial practice that shows the company’s concern towards the environment and helps to shift towards more sustainable production.
Enhanced Resource Efficiency
CO2 recovery is also in line with the circular economy since it transforms what used to be a waste product into a valuable stream. While emitted CO2 is a waste product that can be dumped, recovery technologies enable it to be reused as an input. This not only significantly reduces the release of negative effects but also transforms the efficient utilization of industrial goods. By recycling CO2, industries show that they are managing resources in a proper way, which can lead to the generation of new revenues and value from what was previously considered waste.

Reduced Dependence on CO2 Markets
The application of CO2 recovery technologies gives industries more operational and strategic flexibility. Therefore, by decreasing the reliance on external sources of CO2 and controlling the volatility of the prices of CO2, companies promote a more autonomous business model. This change also assists in the keeping and possibly reducing the cost of inputs while at the same time increasing the long-term viability of the business. Therefore, by protecting themselves from the fluctuations of the global markets, companies establish a more stable and strategically advantageous environment, which is especially important in the world that is gradually turning into a carbon-constrained and economically unpredictable one.
Future Trends and Innovations in CO2 Recovery
The trend in the recovery of CO2 is one that has been on the rise over the years. New developments on the adsorbent materials and advanced membranes exist and hold the prognosis of raised capture efficiency. New and advanced methods of CO2 capture and integration pave the way in industrial processes. In addition to capture, there is increasing interest in utilization of CO2, where the captured CO2 is converted to useful chemicals and fuels through power-to-X processes and biotechnological methods. Some new policies like the regulatory policies and market policies are increasingly becoming tighter, enabling the enhancement of adoption. It is a multimedia CO2 recovery process that will extended international inter-industry networking to effectively become the next generation to build up a sustainable industrial structure.
Conclusion
The collection of CO2 from their source is no longer a luxury in industry but a necessity. It isn’t easy, especially as it requires strong technological background, appropriate policies and, of course, active involvement of the industry. As we have noted, there are various technologies available depending on the requirements, and molecular sieves, particularly those from experienced manufacturers such as Jalon, are crucial. These are apparent, for they range from business benefits to being environmentally conscious. The pressure is on; industries are urged to adopt CO2 recovery, seek out the best solutions, and work with specialists such as Jalon. It is time to seize the opportunity and build an environment that unites industry and sustainability.