What Is a Nitrogen Generator? An Overview
In the industrial processes, nitrogen is a useful, inert gas that is used in many applications including food preservation, safety in chemical plants, etc. In the past, nitrogen was acquired by ordering it in cryogenic tanks or cylinders that were shipped do the heavy lifting. However, the nitrogen generator has changed how the modern business obtains this key element.
As we are aware, atmospheric air is made up of about 78% nitrogen molecules, 21% oxygen molecules and other gases such as carbon dioxide. It’s separated from the ambient air by the nitrogen generator, which functions as a substitution of traditional supply methods and is more continuous, inexpensive, and reliable. This unit is tailored to charge specific flow and purity requirements, thus acting as a dedicated production unit. This on-demand availability reduces logistical issues and supply chain issues that may arise, allowing businesses to manage their nitrogen supply.
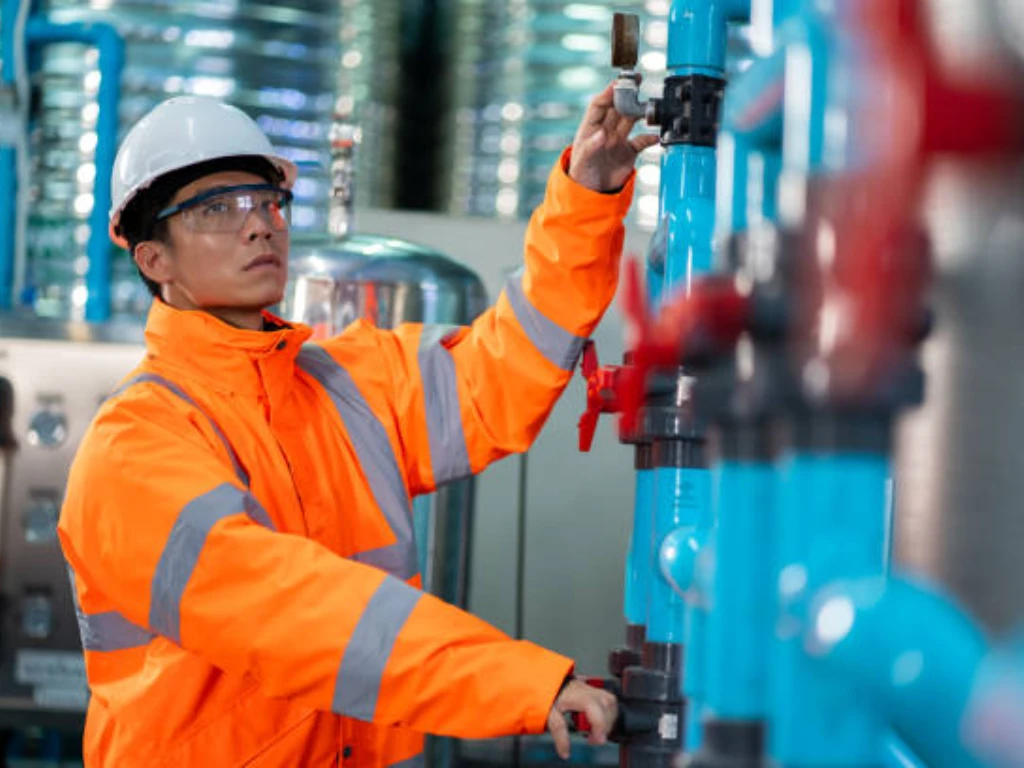
Types of Nitrogen Generators
These generators achieve the same end result – an uninterrupted supply of nitrogen – but they do use different methods, each having its own advantages and appropriate uses. The two dominant types that comprise the industrial bulk are:
Membrane Nitrogen Generator
A membrane nitrogen generator utilizes a nitrogen membrane to extract nitrogen from other elements found in compressed air. This technology employs an operating principle called selective permeability that works on the basis of separating larger molecules from smaller molecules. Oxygen molecules and water vapors can permeate through the membranes, and nitrogen molecules are retained due to their larger size. This separation method produces nitrogen enriched gas streams of 95% to 99% which consists of negligible impurities.
Membrane nitrogen generators are advantageous due to their operational convenience and simplicity. These generators have reduced moving components which makes them more resistant to vibration, corrosion, and wear and tear. These generators are also ideal for use in fire sprinkler systems, some industrial applications, and even some areas in the pharmaceutical industry that require moderate nitrogen purity.
The efficiency of a membrane nitrogen generation system depends on the quality of the compressed air stream quality, pore size, and flow rate. There are no complex adsorptive stage oxygen separation processes involved with this method, which is why it can be utilized in applications that need an uninterrupted supply of nitrogen without high maintenance requirements.
Pressure Swing Adsorption (PSA)
A gas generator using a pressure swing adsorption (PSA) system is a new and sophisticated nitrogen generator with a greater accuracy when compared to the previous designs of nitrogen generators. At its core, PSA employs a molecular sieve to filter nitrogen from other gases, mainly oxygen, in compressed air. This process involves the use of pressure cycles to capture oxygen and let nitrogen pass through.
The PSA process is a cyclic process and it generally employs two adsorption vessels filled with the molecular sieve material. In the first vessel, compressed air is passed through at high pressure, where the molecular sieve adsorbs oxygen, water vapor and carbon dioxide and the nitrogen with a purity of 99.9% or higher is collected. When the molecular sieve in the first vessel is full, the system shifts to the second vessel that contains fresh molecular sieve that has been regenerated. At the same time, the first vessel depressurizes and the trapped gases are released and the molecular sieve is ready for the next cycle. By changing between the vessels continuously, nitrogen is delivered without any pauses.
PSA nitrogen generators are especially suitable for applications where high nitrogen purity is needed, for example, gas chromatography, pharmaceuticals, and fire protection. Although the cost of PSA systems is slightly higher than that of the membrane-based systems, the former is preferred for its ability to produce nitrogen at a very high purity of more than 99.999% (typically ranging from 99.5% to 99.999%).
The last degree of purity of the nitrogen produced by the PSA system depends on the quality and type of the molecular sieve used. Jalon is a professional manufacturer of molecular sieve adsorbents with more than 20 years of experience and a focus on quality. With 112 patents, Jalon specializes in the research and production of advanced molecular sieves that offer high compressive strength, high bulk density, and exceptional adsorption performance. This guarantees that our molecular sieves provide a constant and dependable supply of nitrogen for various applications.
Key Components of a Nitrogen Generator
Component | Description |
Air Compressor | The most important component, responsible for compressing environmental air to the required pressure for nitrogen separation. The size and type of the compressor determine the generator’s efficiency and power output. |
Pre-filters | The first stage of filtration that removes large particles, dust, and oil aerosols from compressed air. This protects downstream components and ensures nitrogen quality. |
Air Dryer | Removes water vapor from compressed air using refrigerated or desiccant dryers. This protects the adsorbent material in PSA systems and improves membrane system efficiency. |
Separation Unit | The core unit for nitrogen generation, which can be a membrane nitrogen generator or a PSA nitrogen generator using a molecular sieve for adsorption. |
Control System | The central control unit that manages pressure, flow rates, and adsorption vessel switching in PSA systems. It may also include advanced automation features. |
Nitrogen Storage Tank | An optional but essential component that stores produced nitrogen, ensuring a steady supply despite usage variations. |
Post-Filters | The final filtration stage that removes any remaining fine particles or impurities, ensuring the nitrogen meets the required quality standards. |
How Does a Nitrogen Generator Work? Step-by-Step Process
Although the procedures may differ slightly depending on the type of nitrogen generator (membrane, or PSA), the process is the same: to take the air from the environment and separate nitrogen from it to provide the nitrogen with the desired purity and flow rate for various industries. Now let us take a step-by-step look at the following:
Step 1: Air Compression
The process starts with an air compressor that sucks in air from the surrounding environment and compresses it to a certain pressure. The pressure required is dependent on the type of generator and the level of purity required, and is usually between 5 and 10 bar for most PSA systems. On the other hand, membrane systems work at relatively low pressures, normally ranging from 4 to 7 bar.
Step 2: Air Pre-Treatment
The air that is to be separated is first pre-treated to eliminate any unwanted materials that may be present. This entails filtering the air to eliminate dust, particles, and oil and then using an air dryer to eliminate moisture. Of all the factors affecting the performance of PSA and membrane separation, moisture is a key problem and one of the most challenging to manage.
Step 3: Gas Separation Process
In a membrane nitrogen generator, the compressed air is taken through membrane systems where oxygen molecules, water vapor and other impurities are separated from the nitrogen.
In a PSA nitrogen generator, the adsorption stage oxygen process takes place where oxygen is selectively adsorbed by the molecular sieve while the nitrogen molecules pass through it.
Step 4: Nitrogen Storage (Optional)
In cases where nitrogen is needed continuously, the generated nitrogen is stored in tanks. This storage helps to maintain a steady rate of flow even if there is a temporary increase in the rate of flow.
Step 5: Nitrogen Post-Treatment (Optional)
In some cases, nitrogen may be subjected to final treatment, which may involve further purification to remove any residual impurities to achieve a certain level of purity for specific applications.
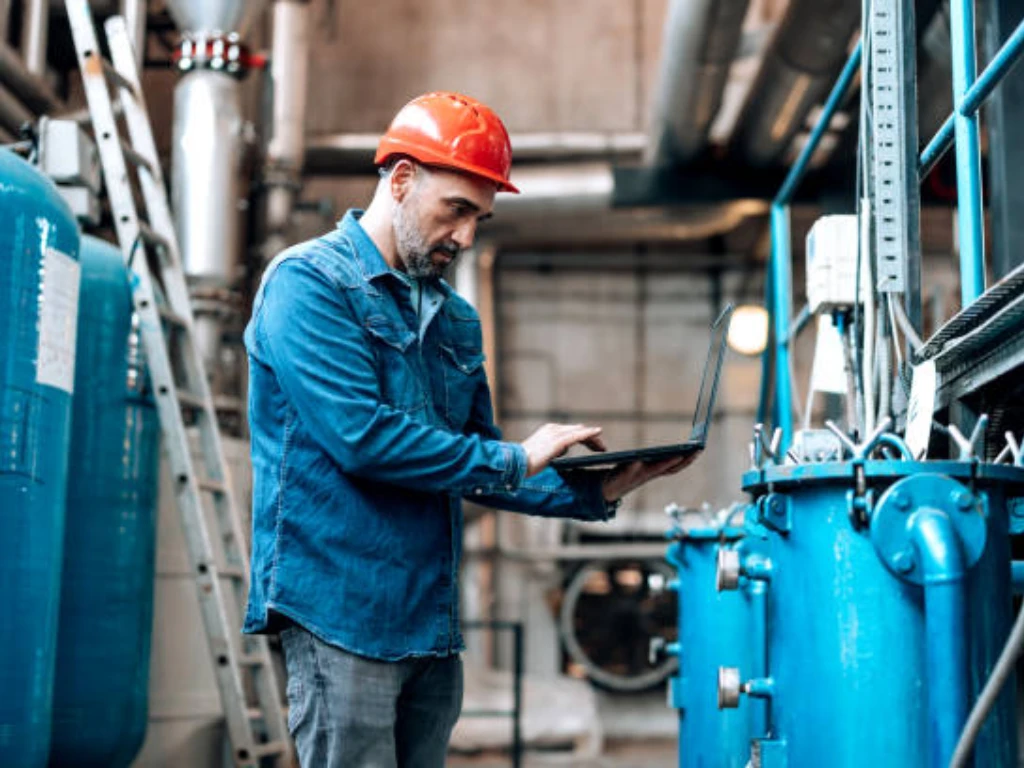
Advantages of Using a Nitrogen Generator Over Traditional Supply Methods
There are many advantages of using an on-site nitrogen generator over other methods of nitrogen supply such as cylinders or liquid nitrogen deliveries. The most important benefits can be attributed to cost reduction, increased dependability, and increased safety.
Cost Savings and Efficiency
The major benefit that can be derived from the use of a nitrogen generator is the fact that it is relatively cheaper to run. In contrast to nitrogen cylinders, which are costly to maintain through delivery fees, cylinder rental, and other administrative costs, a nitrogen generator supplies nitrogen as needed. This does away with such recurrent costs, which in the long run translates to cost savings. For industries that use nitrogen in large quantities, the cost of owning a generator will be recovered in the long run since it is cheaper than having to order nitrogen in bulk or rent cylinders.
Reliability and Convenience
An on-site nitrogen generator guarantees a constant and stable supply of nitrogen, which is free from the dangers of having to depend on third parties. Businesses do not have to worry about cylinders’ stock, delivery, or lack of nitrogen at some point in the process. This means that there is a constant supply of nitrogen whenever it is required, thus making the operations to run smoothly and efficiently.
Safety and Operational Simplicity
Nitrogen cylinders pose certain risks such as leakage of nitrogen, pressure risks and proper storage and ventilation. These risks are however eliminated by using a nitrogen generator since nitrogen is generated within the facility hence no need to handle high pressure cylinders. This results in a reduction of the number of accidents that are likely to occur in the course of transporting and handling the cylinders.
Purity Control
Nitrogen generators allow the user to generate nitrogen at the level of purity that is needed for the application. In contrast to other methods that may provide less control, on-site generation guarantees that nitrogen is of the right purity to enhance performance and quality.
Environmental Benefits
On-site nitrogen generation also has a number of environmental advantages. This is because businesses do not have to transport nitrogen cylinders or liquid nitrogen, which helps in cutting down the carbon footprint. Further, on-site generation is less wasteful of nitrogen, particularly when compared to liquid nitrogen, which is known to undergo evaporation losses during storage and use.
These benefits of cost, reliability, safety, and environmental advantages make nitrogen generators suitable for industries that need a constant and high quality nitrogen supply.
Common Applications of Nitrogen Generators in Various Industries
Nitrogen generators have become indispensable in various fields due to the convenience of having a constant supply of high purity nitrogen. The following are some of the uses of nitrogen generators:
Pharmaceutical Industry
Nitrogen gas is used in the pharmaceutical industry in various ways such as in packaging of drugs, storage of drugs, and in laboratory uses. High purity nitrogen helps to avoid oxidation of the product, moisture content and microbial growth, thus enhancing the stability and safety of the product.
Fire Protection Industry
In the fire protection industry, nitrogen gas is used to help reduce the effects of corrosion in fire sprinkler systems. This is because when oxygen rich air is replaced with nitrogen molecules in the sprinkler pipes, the chances of corrosion are greatly reduced thus increasing the life span of the system.
Food and Beverage Industry
In food packaging, nitrogen gas is used to create an environment that reduces the rate of oxidation and microbial activities hence increasing the shelf life of the food. Cylinders of nitrogen were used in the past but the current membrane nitrogen generator systems are cheaper and supply nitrogen in a continuous flow for the packaging lines.
Electronics and Manufacturing
Some of the industries that use nitrogen include electronics manufacturing, laser cutting, and gas chromatography where nitrogen is used to minimize contamination and oxidation. A nitrogen generator system provides a consistent temperature of nitrogen and the flow rate of nitrogen is also controlled, which enhances the production process.
Oil and Gas Industry
PSA nitrogen generators are used in the oil and gas industry to ensure that storage tanks and pipelines are filled with an inert gas. This is because when oxygen is replaced with pure nitrogen, the chances of combustion and oxidation are greatly minimized.
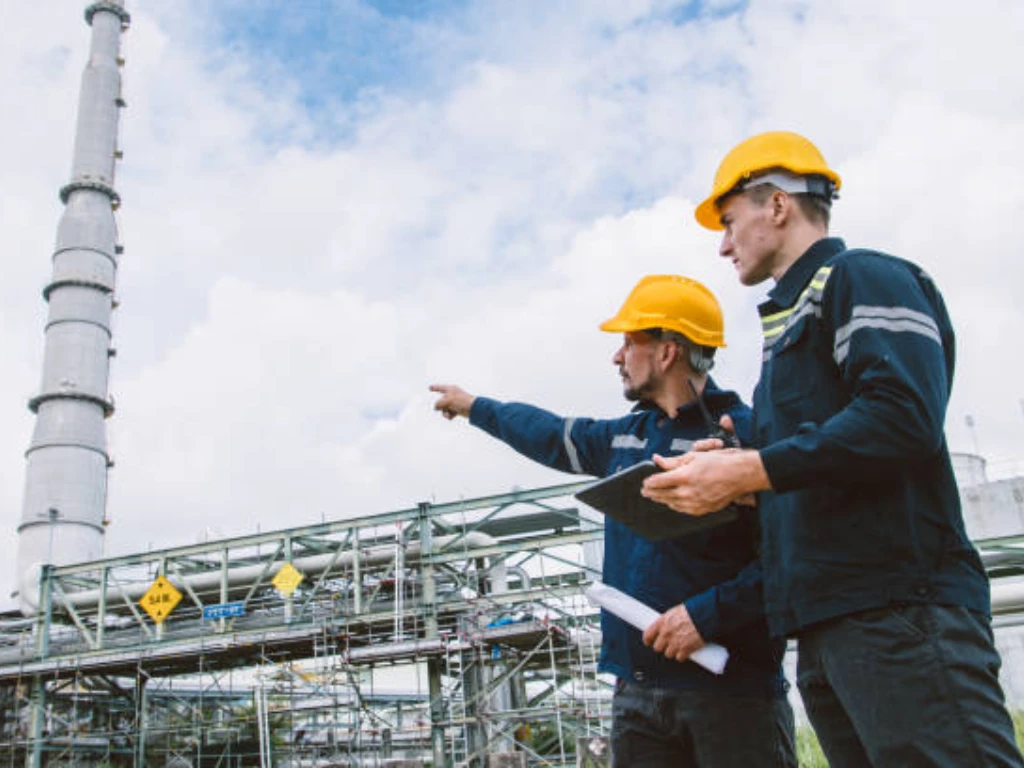
Selecting the Right Generator for Your Needs
Selecting the right nitrogen generator is crucial for the proper functioning, cost-effectiveness, and the required nitrogen output for the process. Below is a guide that can be followed in order to make the selection easier:
Understand the Technology Options
First of all, it is necessary to distinguish between two main types of nitrogen generation – PSA and membrane. PSA generators are particularly suitable for generating high purity nitrogen (greater than 99.9%) by employing molecular sieve for separation. They are most suitable for use where there is need to maintain high purity of the fluid being processed, but they are more energy intensive because of the need to regenerate them periodically. Membrane systems are more energy efficient and less complex and therefore suitable for applications where high purity is not required (up to 99.5%).
Know Your Purity Requirements
Secondly, identify the level of purity that is needed. In industries such as the pharmaceutical or semiconductor, purity levels above 99.9% are often required and this is where PSA nitrogen generators come in handy. On the other hand, applications such as food packaging may only need nitrogen with a purity of up to 99.5% which is well suited for the membrane nitrogen generators.
Calculate Your Flow Rate Needs
Secondly, assess your nitrogen usage in terms of flow rate, which is normally expressed in liters per minute (LPM) or cubic meters per hour (Nm³/h). Both your current requirements and your future requirements should also be taken into consideration. PSA systems are ideal for applications that require high purity of the gas and high flow rates while membrane systems are ideal for low and stable flow rates.
Consider Installation and Operating Environment
Membrane generators are compact in size and thus occupy less space than PSA systems which require space for the adsorption vessels. Also, check the quality of the compressed air used in your facility and the temperature of the environment since they affect the system.
Energy Efficiency and Future Growth
Energy is also a major cost factor in operation, so look for models that are more energy friendly. PSA systems are generally more energy intensive because of the regeneration process while membrane systems are continuous processes with lower energy requirements. Also, it is advisable to select a generator with enough capacity for future growth or go for a modular system.
Total Cost of Ownership
Apart from the initial cost, think about the costs of using the product in terms of energy consumption, maintenance, and replacement of parts such as filters. Select manufacturers that have a good reputation for providing quality equipment and good customer service after the sale.
Thus, by considering these factors, you can select the nitrogen generator that will suit your operation’s requirements in terms of performance and cost.
Maintenance for Optimal Nitrogen Generator Performance
Maintenance is crucial in order to keep your nitrogen generator reliable, efficient and long-lasting. Maintenance reduces the chances of having to spend a lot of money on repairs, avoids disruption of operations, and guarantees a steady production of nitrogen for important applications.
Regular Filter Replacement
Filters are very important in the protection of your nitrogen generator. They eliminate water vapor, dust, and oil from the compressed air, thus providing high purity nitrogen supply. These filters get blocked over time, which can lead to reduced efficiency of the system and internal parts. It is recommended to change the pre-filters and post-filters as often as stated by the manufacturer to ensure that the system is working efficiently and the nitrogen is of high purity.
Molecular Sieve Regeneration (PSA Systems)
In PSA nitrogen generators, molecular sieves are used in the process of separating nitrogen from oxygen. These sieves need to be regenerated from time to time so as to restore their adsorption capacity. If the regeneration is not done properly, the nitrogen purity is likely to drop to below the recommended 99.9%. It is important to ensure that the regeneration cycles are carried out properly in order to maintain a constant production of nitrogen.
Monitoring Pressure and Flow Rates
Pressure and flow rates should be kept constant to ensure that the nitrogen is produced at the right rate. Ensure that the air compressor, PSA systems, and membrane units are frequently calibrated to avoid pressure changes that may hamper the separation of gases. Maintaining the system within these ranges reduces the likelihood of failure and guarantees that the nitrogen is of the right quality.
Addressing Leaks and Vibration
Small leaks or excessive vibration can cause a huge problem to the generator since it will consume more energy and produce less nitrogen. Check for any signs of leakage especially around joints, valves, and pipes and repair them as soon as possible. Vibration is detrimental to the system and its components and thus minimizing it is beneficial for the longevity of the system.
Maintain the Air Compressor and Dryer
The air compressor and air dryer are two important components in the nitrogen generation process. The compressor should be maintained as per the manufacturer’s recommendations, that include oil change and filter replacement. Also, check on the air dryer as moist air affects both the PSA and the membrane systems. For desiccant-type dryers, always adhere to the recommended regeneration or replacement schedule to avoid the accumulation of moisture.
These practices will help you to get the most out of your nitrogen generator in terms of performance, durability and cost of nitrogen supply to your operations.
Conclusion
In summary, nitrogen generators are more advantageous than supply methods such as liquid nitrogen, and these include; cost, reliability and safety. Thus, it is crucial to understand the two main types of generators, PSA and membrane that can be chosen depending on the nitrogen purity, flow rate, and energy consumption desired by the business. Proper maintenance can help to make sure that the system is running optimally, delivering high purity nitrogen and at the same time, reducing the frequency of downtimes and the costs of running the system.
As for the future, the nitrogen generation industry is expected to experience further development in terms of technology and performance. New developments in membrane materials, and the molecular sieves for PSA systems are expected to increase nitrogen purity and decrease energy use. Moreover, the increasing automation and IoT integration may bring more accurate control, condition monitoring, and energy management. As industries focus more on sustainability, nitrogen generators will also change in a way that will help reduce the impact on the environment while offering a reliable source of nitrogen on demand.
In other words, nitrogen generators are a long-term investment that not only helps to make the work easier but also contributes to environmental and cost objectives.
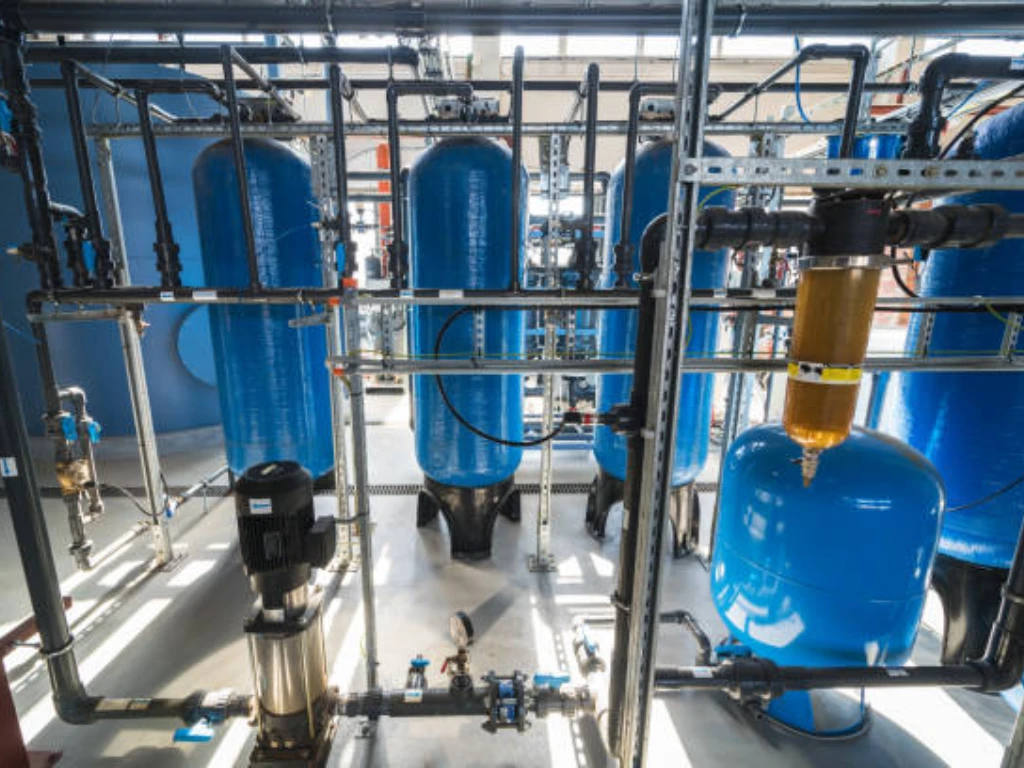
FAQS
Q: Can the flow rate and purity of nitrogen be adjusted as needed?
A: Many nitrogen generators allow users to adjust the flow rate and purity of the nitrogen to meet different application requirements.
Q: Can nitrogen generators operate in extreme environments?
A: Most nitrogen generators can operate in various industrial environments, but extreme temperatures, humidity, or contamination may affect their performance. Special designs or additional protective measures may be required in such conditions.
Q: Is on-site nitrogen generation environmentally friendly?
A: Yes, on-site generation reduces transportation emissions, minimizes nitrogen loss, and can be integrated with renewable energy sources for greener production.