Anyone that has undoubtedly worked in a lab and been taught how important that dry solvent is, but the container with the mystical molecular sieve at the base just stays completely filled and no one can recall it ever being regenerated, correct? Perhaps it’s time to replenish those pellets!
sieves are a wonderful innovation. 3A molecular sieves effectively dry each popular solvent excluding acetone as well as or greater than a solvent still at 10-20% w/v. A container of sieves/solvent is also significantly less likely to catch fire and is far less expensive to keep in good working order.
The whole process of activating a molecular sieve may seem rather confusing. That is why we are going to walk you through it in this article. Let’s get to it!
What is a Molecular Sieve?
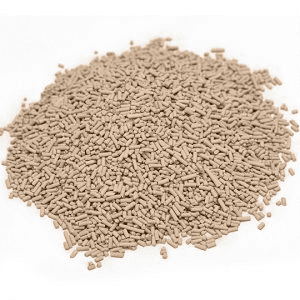
A molecular sieve is a penetrable material with pores of constant size. The diameter of these holes is equivalent to that of very small particles. As a consequence, big molecules are unable to move via these holes and are adsorbed, whilst smaller particles may.
The particles with the largest mass tend to depart first, trailed by those with lower molecular weights when a mixture of particles relocates through a packed bed of porosity and semi-solid substances (the sieve). As a corollary, these molecular sieves can help in chromatography. Particular varieties of molecular sieves can be used to make dryers.
It can be employed to dry gas flows in the petroleum sector, according to the molecular sieve material’s usage. Other solvents, as well as powerful desiccants, can be dried with this chemical. Catalytic applications can catalyze isomerization, alkylation, and epoxidation. Scuba divers and firemen wearing breathing apparatus can also utilize molecular sieves to filter their air supplies.
Why Do You Need to Activate a Molecular Sieve?
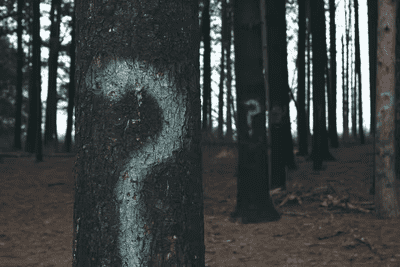
Before using, molecular sieves should be activated (dried). Put a small number of molecular sieves in the palm of your hand and add a drop of water to see if they’re dry. They are dry if they emit a significant amount of heat. The main goal of activation is to increase their functionality and to keep the product dry and stable.
What Do You Need to Activate Molecular Sieve?
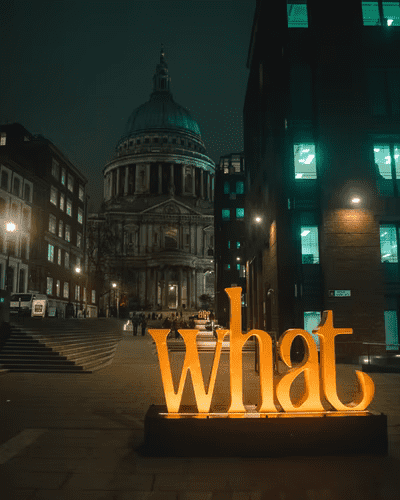
For Small Amount
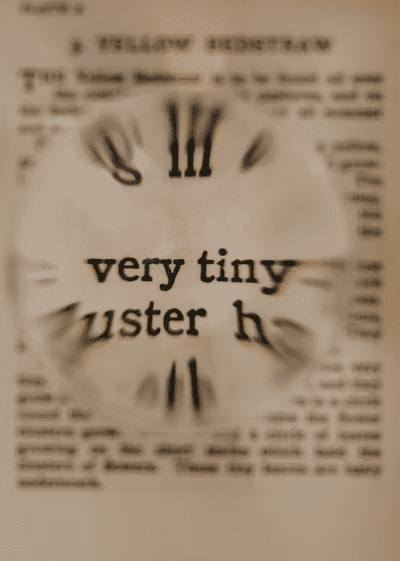
Activating a molecular sieve in smaller amounts, use a flow control adaptor, heat molecular sieves to 120 °C in an oil bath beneath a high vacuum overnight (no stirring required). Refill with argon and use as needed. Inspect sieves for heat production on a regular basis and dry as required.
For Industry/Large Amount
To activate a molecular sieve for industrial purposes, you need to heat it under a high vacuum and a temperature between 175 °C to 315 °C.
The Process of Molecular Sieve Activation
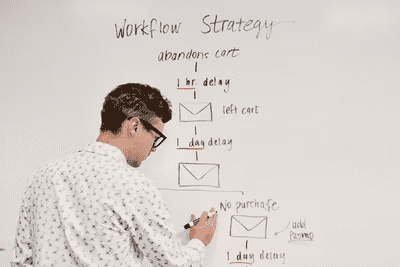
In a conventional cycle system, regeneration entails heating and purging with a carrier gas to remove the adsorbate from the molecular sieve sheet. To evaporate the fluid and offset the heat of soaking the molecular sieve exterior, adequate heat must be given to elevate the temp of the adsorbate, the adsorbent, and the vessel.
When it comes to regeneration, the temp of the bed is crucial. For type 3A, bed temps in the 175-260° range are commonly used. When olefins are prevalent in the gas, this lower range limits polymerization on the molecular sieve substrates. Most olefinic compounds will be eliminated at low temps, therefore a moderate heat up is advised; temps in the 200-315 °C range are required for 4A, 5A, and 13X sieves.
Following regeneration, the molecular sieve must be cooled to within 15° of the temp of the stream to be treated. The most straightforward way to accomplish this is to use the same gas stream as is used for heating but with no heat input. During the heat-up loop, gas flow ought to be a sequence of events leading to adsorption, and throughout the cooling cycle, it should be simultaneous (according to the procedure stream). In the lack of purge gas, tiny amounts of molecular sieves can be dried in an oven characterized by slow chilling in a closed environment, such as a desiccator.
The Activation Procedure
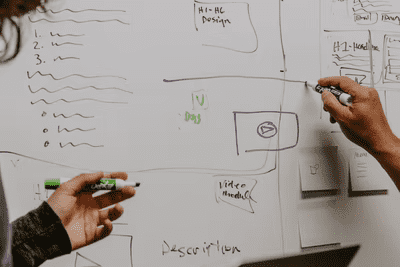
- A depressurization step is frequently included in the regeneration cycle. If the regeneration is carried out at a pressure lower than that of the adsorption stage, depressurization is needed. Because the regeneration gas is not the product gas, or perhaps another gas accessible at a lower pressure, such as N2, H2, CH4, and fuel gas, this could happen for a variety of reasons. The lower pressure can also be used to reduce the amount of energy required for regeneration.
- Draining is the second step in molecular activation. Before introducing a heating gas, all liquid must be drained from the adsorber during the draining stage. Gravity flow is usually used to drain the liquid. Omitting for a little part caught in the molecular sieve and on the exterior of the adsorber container, practically all of the liquid is drained at the end of the draining step. This liquid is eliminated during the purging stage, which involves introducing cold regeneration gas for 1–2 hours to remove any leftover liquid.
- The heating process begins with the infusion of hot regeneration gas into the vessel. To prevent thermal pressure, the temp is gradually expanded to the heating temp.
- The heating energy required for the regeneration is supplied by a hot gas with a specified flow rate, temp, and flow duration.
- The contaminant loading on the molecular sieve decreases as the temperature rises. Passing a hot gas stream has two impacts: first, the contaminant desorbs as the temp rises, and second, the desorbed pollution is transported out of the sheet. To desorb the contaminant, a particular amount of heat at a low temp should be introduced into the adsorber.
- Furthermore, if the activation gas flow rate (or period) is too low, a deposit will develop on the higher layers of the molecular sieves because of a lack of resorption energy. Owing to the favoured direction of the flow, the gas does not move through the whole sheet in laminar flow or direction, but rather via only a portion of it. This could result in a localized build-up in the bed.
- The molecular sieve is activated at the end of the heating stage. The contaminants, although, are not entirely removed. The balance conditions at the end of heating and the thermal pattern seen by the molecular sieve invariably leave a remnant content of contaminant in the molecular sieve.
- For example, towards the end of a production procedure, a new sieve is activated at 500°C–600°C and has a really low remnant water content (less than 0.5 percent). The value of this remaining impurity content is determined by the regeneration grade (temp, duration, flow rate, and other process factors) as well as the molecular sieve’s age. As a result, the next adsorption cycle will have a shorter adsorption time.
Things to be Concerned About
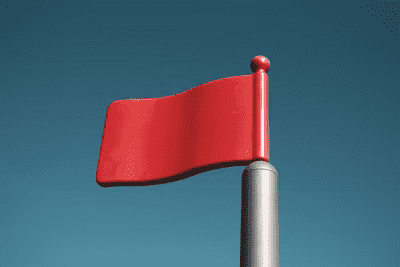
While molecular sieve activation is a simple process, you need to be cautious when handling the gases and heat. The last thing you want to do is cause a disaster.
Conclusion
Molecular sieve is the best desiccant in the market. For the highest quality, Jalon is the best choice for you. Reach out to us and We will be delighted to provide you with our expertise.