The saturated Activated Alumina is quickly dehydrated during activation, which is a core premise of drying and adsorbing by Activated Alumina. After the activation, which is a physical adsorption procedure, it might slurp up reversibly. Since it has a higher absorptivity to water, Activated Alumina has a superior drying impact than any other sorbent. It has a substantially higher adsorptive capacity even when frictional force and concentration are very low.
As a result, we may experience a deep dryness wherever it is utilized. The Activated Alumina always has a substantially higher drying efficiency underneath a larger employing scope and dynamics. It has a large adsorption capacity, a quick adsorption speed, strong heat stability, consistent working reiteration, and no crush when exposed to liquid.
If you are having trouble figuring out how you can regenerate activated Alumina, this article will answer your question. Keep reading to find out more!
Why Do We Regenerate Activated Alumina?
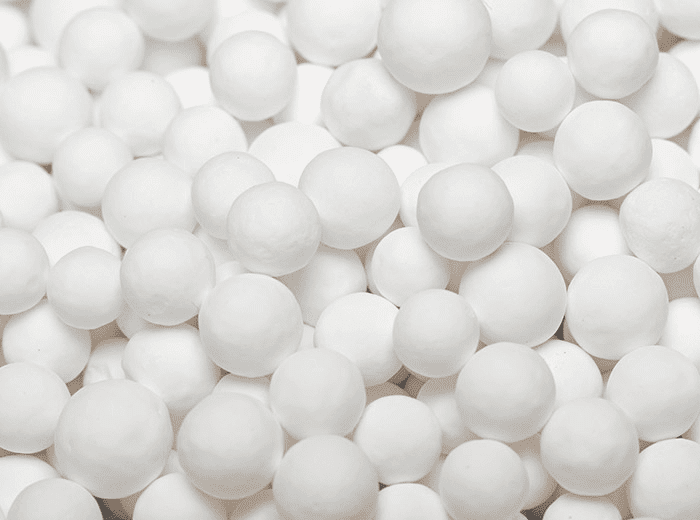
The physical and chemical characteristics of alumina, as well as the water to be purified, influence the fluoride absorption capacity of Activated Alumina. Activated Alumina becomes saturated with fluoride ions after a period of time and loses its ability to remove fluoride ions from water. “Exhausted Activated Alumina” is the name given to this level of Activated Alumina.
There are two alternatives available to users. Change out the old Activated Alumina for a fresh one. Alternatively, you can regenerate the Activated Alumina that has been depleted. The regeneration alternative is economical because it costs 1/15th as much as swapping an exhausted Activated Alumina with a new one.
What do you need for activated alumina regeneration?
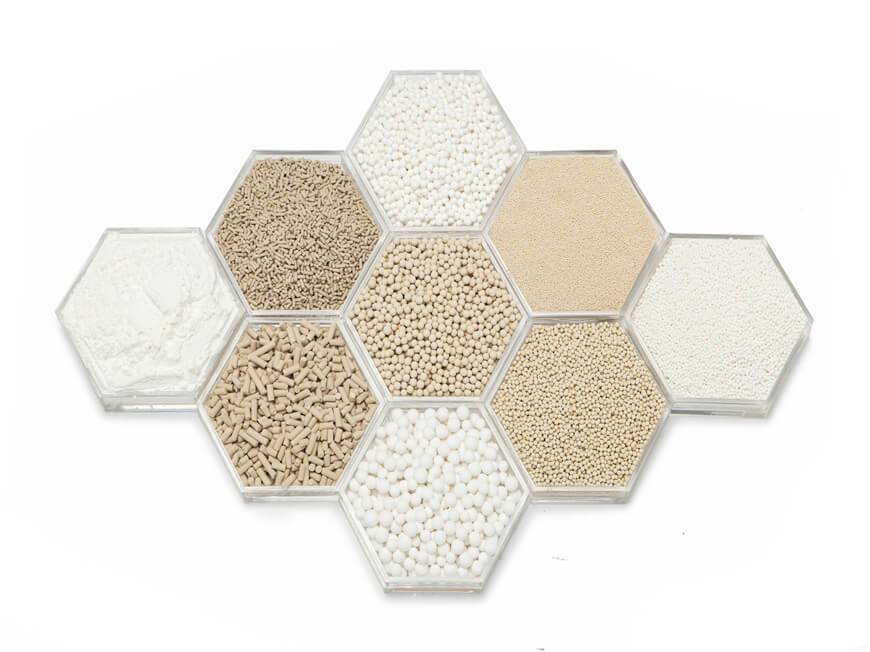
For a successful regeneration process, the following items are needed:
Chemical Requirements
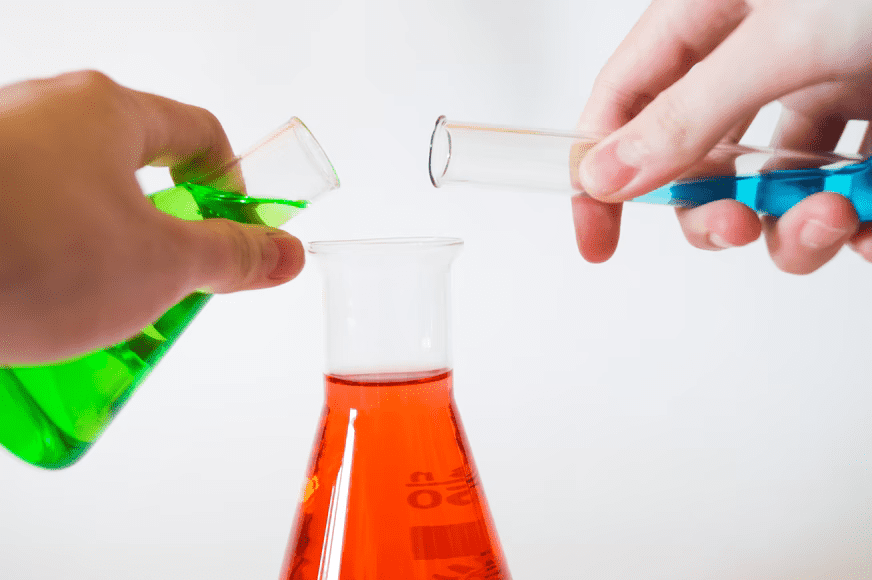
- Commercial grade Caustic Soda(Sodium-Hydroxide)
- Commercial grade Concentrated Sulphuric Acid
- Lime
- Baking Soda(Weak Base)
- Acetic Acid(Weak Acid)
- YES/NO fluoride testing kit with reagent
Equipments
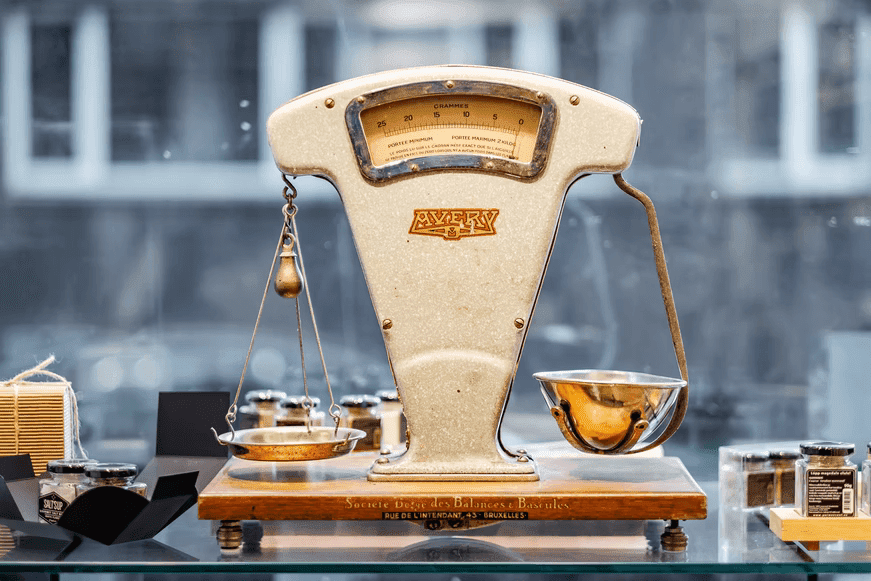
- Balancing scales
Other Things to Have
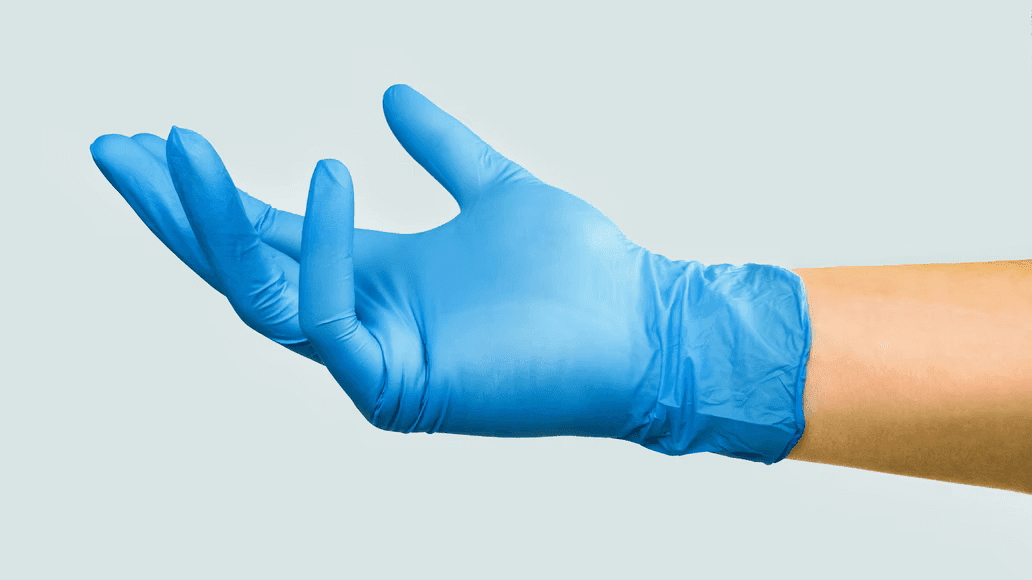
- Plastic Bucket with Graduations
- Plastic Container(200L)
- pH Strip(range of 2-10.5)
- Plastic Measuring Cylinder(100ML(2), 1000ML(2))
- Rubber Gloves
- Rubber Apron
- Plastic Rod
- Goggles
How to Regenerate Activated Alumina
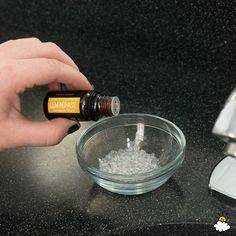
Regeneration of activated alumina is required during the drying of activated alumina. In most cases, hot nitrogen is used to purge desiccant renewal. It’s challenging to entirely desorb the adsorbed liquid in plenty of other techniques due to the powerful interaction between water and activated alumina. In 3 stages, the heating and desorption operations involve heating, cleansing, and chilling.
The more comprehensive the desorption regeneration, the greater the heating temp. Temperatures for activated alumina heating regeneration range from 180 to 350 degrees Celsius. The temperature of the activated alumina tower is usually elevated to 280 degrees Celsius for four hours. Heating at a pace of roughly 50 degrees Celsius per hour.
Because a large content of water vapour at extreme temps can significantly destroy the structure of activated alumina, the active alumina bed should be rinsed with nitrogen, air, product gas, or another acceptable gas while heating.
Water should not be present in flushing gas since the quantity of moisture in the flushing gas has a serious influence on the regeneration effect. After the active alumina bed has been regenerated, it must be chilled prior to the adsorption procedure, with the chilling gas being utilized to cleanse the bed and to avoid containing water, cold gas flow and adsorption loop in a similar direction.
When activated alumina is applied to dry liquids such as propylene, it is required to move the liquid through the active alumina bed sans any dead ends during regeneration. Otherwise, when heated, the leftover liquid will react or carbonize, reducing the adsorption cycle’s effectiveness and operating life.
The life of activated alumina will be extended if the activated alumina is of a good grade. Regardless of how awful or wonderful it is, desiccant regeneration must be used for future applications. However, the performance of high-quality activated alumina might extend the life and enhance the drying circumstances.
The Regeneration Procedure:
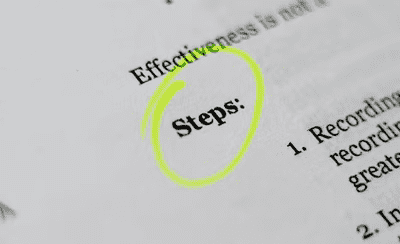
- Fill the nylon bag with the entire amount of drained AA from the domestic filter (mesh size 0.106 mm). Throughout the transference of Activated Alumina, assure there are no spills.
- Mass 100g of caustic soda flakes in a plastic plate or jug with rubber gloves.
- Carefully add caustic soda into 10 litres of water. To disintegrate the flakes, mix with a plastic rod. The resulting alkali solution is 1 percent NaOH.
- Tie the nylon sack around the neck of the weary AA. Place the nylon bag in the weakened caustic soda (NaOH) mixture in the pail. Each 2 hours, shake the bag within the pail to guarantee that the caustic soda mixture and the exhausted Activated Alumina are in contact. Lift the bag from the pail after 8 hours and drain any residual alkali into the pail. It’s worth noting that the caustic soda mixture is only needed once to cure roughly 5 kilograms of AA.
- Fill the settling tank halfway with the used caustic soda mixture from the pail.
- Fill a plastic bucket with 10 litres of clean water and place the nylon bag inside. This is where the washing process begins. As indicated in step 4, bounce the nylon bag up and down a couple of times. Perform the washing process at least twice more, using fresh water every time. This cleansing phase can be done with raw water containing fluoride.
- Transfer 100mL concentrated sulphuric acid from the acid container to a graduated cylinder while wearing gloves. Carefully add the acid down the edge of a 15-litre plastic bucket filled with 10 litres of water. When adding acid, stir the water using a plastic rod. 0.4 N sulphuric acid is the acidic mixture obtained (H2SO4). When working with acids, never add water. It has the potential to result in a major collision.
- Drain any surplus water before transferring the activated alumina-filled nylon bag to the acid solution-filled pail. To establish good contact between the Activated Alumina in the nylon bag and the acid mixture, move it up and down as specified in step 4 above. Lift the sack and pour away excess acid after 4 hours, ideally overnight.
Initiatives at the Individual Household Level
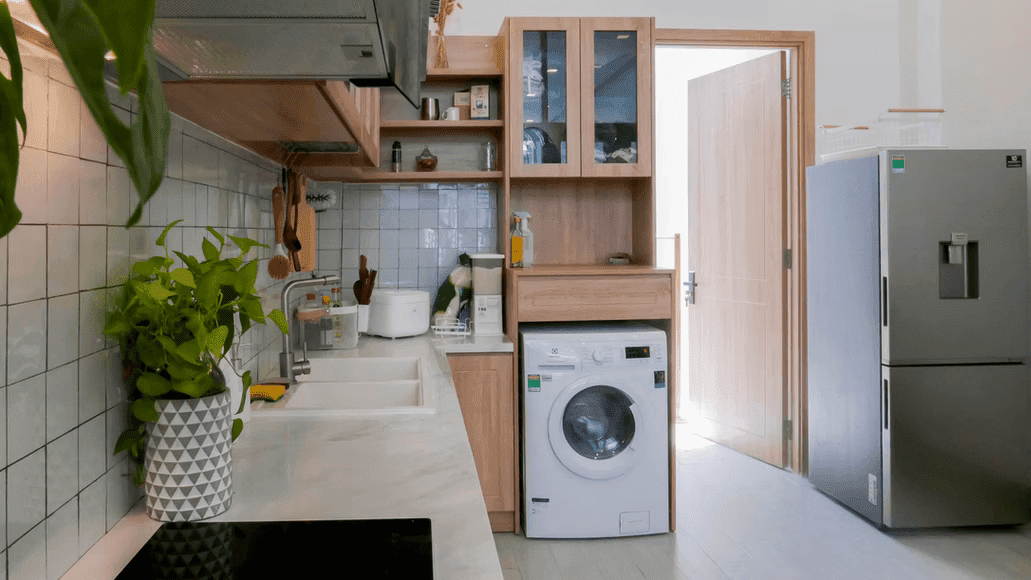
- Return the purified activated alumina to the home defluoridation unit via the nylon bag. During transference, be careful not to lose any activated alumina.
- Now you can utilize the domestic filter. Fluoride levels in treated water should be far below 1.5 mg/L.
Things to be Concerned About
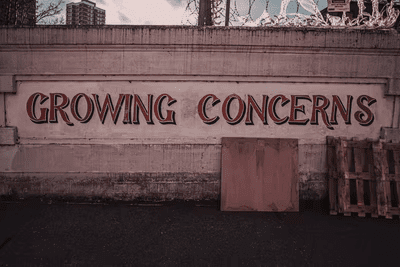
Particular precautions must be followed when working with caustic soda and acid. It is possible that you and others will be seriously injured if you do not take the following measures. To prevent harm, strictly follow the precautions mentioned below:
- When working with acid or alkali, always use rubber gloves and goggles.
- Keep chemicals out of reach of youngsters and in a secure location, such as a closed closet.
- When moving the bottles, significant caution is required. Holding the bottle by the neck can cause it to break, resulting in a serious accident. With both hands, grasp the bottle’s bottom. When transporting a bottle from the storage cabinet to the work area, always utilize a bottle carrier, such as a pail. Make use of compact bottles that are easy to handle.
- Caustic soda loses its potency when it absorbs water. As a result, the bottle of caustic soda should be firmly closed..
Conclusion
So there you go, now you are ready to regenerate your exhausted Activated Alumina. Speaking of which, you need to get quality for the next purchase you make for your Activated Alumina. This is what we, at Jalon, specialize in. Contact us and we are certain that we will meet your needs for activated alumina and any other desiccant.