Introduction to Cryogenic Distillation
In the field of air separation, cryogenic distillation is an important process that makes it possible to produce high-purity nitrogen, oxygen and argon. This advanced technology, one of the key cryogenic technologies, operates on the premise of fractional distillation and relies on extremely low temperatures in separating air components due to their different boiling points. Cryogenic distillation is commonly used in many industries including production of industrial gases, combustion enrichment and specialty gas production.
Cryogenic air separation units (ASUs) or Air Separation Plants are the places where cryogenic distillation takes place by compressing atmospheric air, cooling and separating it into its main constituents. The process involves a combination of heat exchangers, columns for fractionating mixture at different liquids composition levels, as well as refrigeration systems that work together to achieve the target purity requirements. These cryogenic technologies are also used in the liquefaction and separation of natural gas. Molecular sieves are vital parts of this system as they help remove impurities such as water vapor, carbon dioxide and hydrocarbons from both inlet and product streams. According to a report by Grand View Research, the global market size for air separation plants was valued at $4.8 billion in 2020 and expected to grow at a CAGR of 5.2% between 2021-2028.
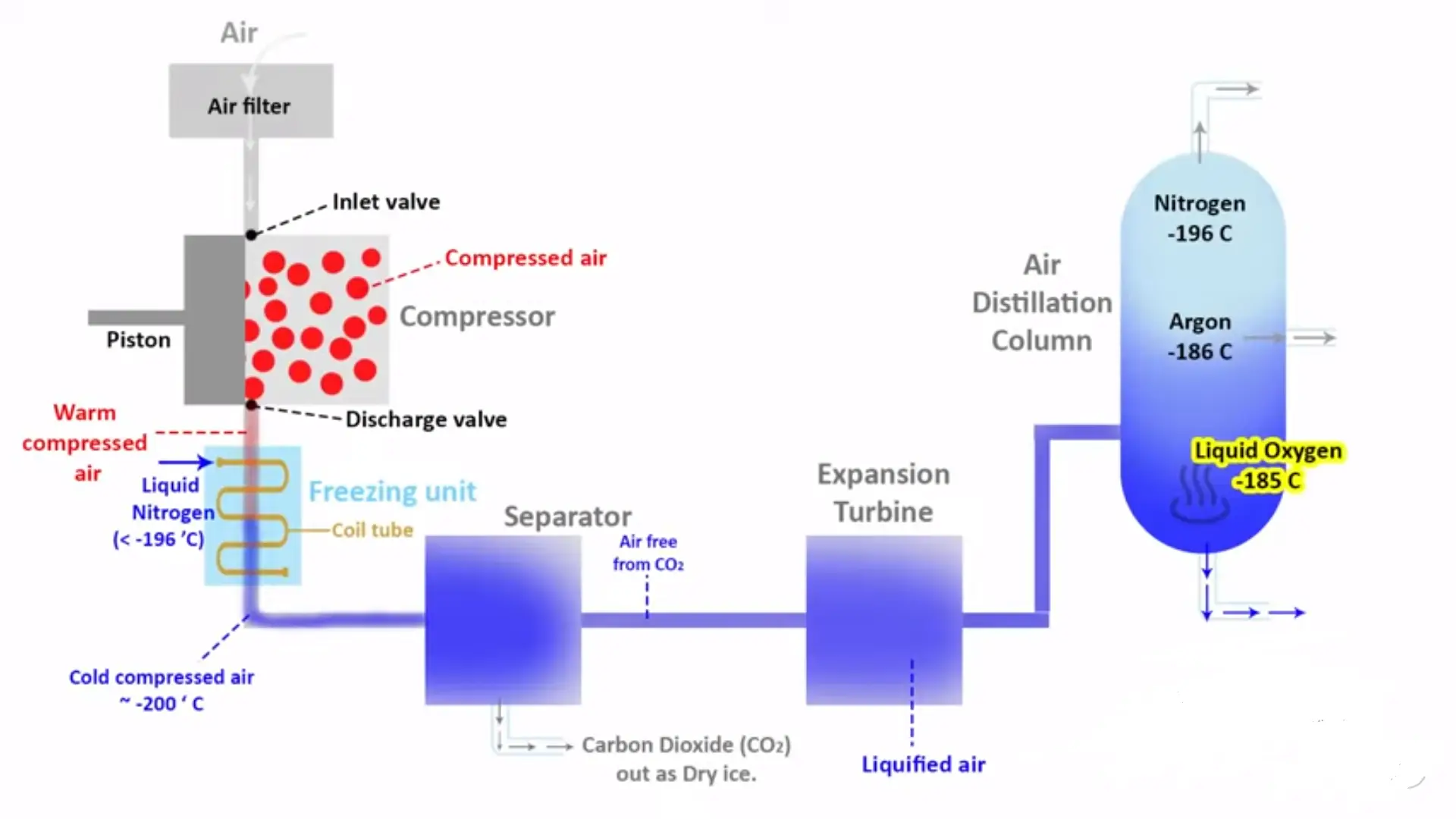
Key Components of a Cryogenic Distillation System
Air Compression and Cooling
Cryogenic distillation starts with air compression and cooling. Filtering of the air to eliminate any impurities is the first step before compressing it to high pressures often ranging between 6-8 bars. The compressed air undergoes a number of heat exchange processes, which reduce its temperatures to near ambient. The main aim of this initial cooling stage is to prepare the air for further processing while ensuring that cryogenic stages are more efficient.
Heat Exchangers in Cryogenic Cooling
The network of heat exchangers in turn cool the compressed air at cryogenic levels after an initial stage of cooling. These heat exchangers achieve gradually lower incoming temperature through utilization of cold exhaust gases from distillation columns. At around -180°C, it reaches a point where it starts liquefying. Liquefaction is a major process in cryogenic distillation since it allows for fractionation into its constituents via their different boiling points.
Distillation Columns and Refrigeration
The heart of cryogenic distillation process can be found within the distillation columns where we have separation of air into its basic ingredients. A nitrogen-rich vapor and an oxygen rich liquid are produced when liquidified air enters a high-pressure distillation column. After that, the nitrogen-rich gas is further purified using a low-pressure distillation column while oxygen-rich liquid gets rid of other impurities and recovers argon.
Refrigeration plays an important part in maintaining cryogenic conditions necessary for effective atmospheric separation. In closed-loop refrigeration systems used during cryogenic distillation processes, Nitrogen expansion cycle or Mixed refrigerant cycle are commonly employed as well. The refrigeration systems ensure that the columns are working within right temperatures required for good separation among several components of air.
The Role of Molecular Sieves in Cryogenic Distillation
Molecular Sieve Pre-Purification Units
The process of cryogenic distillation mainly consists in using molecular sieves to pre-purify air. The compressed air flows through a molecular sieve bed before entering the main air separation unit, this is aimed at removing impurities which may either hinder the cryogenic process or besmirch product quality.
One of the important functions of molecular sieves at this stage is to remove water vapor and carbon dioxide from compressed air. When not removed, these impurities can freeze and block heat exchangers as well as distillation columns causing process interruptions and reduced effectiveness. Molecular sieves are able to trap water vapor and carbon dioxide with their selective adsorption ability hence providing clean dry air feed for cryogenic distillation.
Molecular sieve pre-purification units have several advantages over classical reversing heat exchangers. However, reversing heat exchangers fall short of effectively eliminating carbon dioxide though they are competent in removing water vapor. Unlike the latter, molecular sieves can remove both water vapor and carbon dioxide simultaneously thus giving a comprehensive purification solution. Secondly, molecular sieves have better adsorption capacity and they operate at higher temperatures than reversing heat exchangers thereby leading to improved energy efficiency together with lower maintenance costs.
Molecular Sieve Applications in Air Separation
For the manufacture of pure products in cryogenic distillation, molecular sieves are very important. Molecular sieves remove substances such as water vapor, carbon dioxide and hydrocarbons from the air stream so as to make high purity nitrogen, oxygen and argon.
Molecular sieves also protect downstream equipment in cryogenic distillation. By removing impurities that may harm or impair the performance of heat exchangers, distillation columns and other key components, molecular sieves prolong equipment life and reduce maintenance. In cryogenic applications, this protection is essential because these extremely low temperatures lead to fast wear and tear of equipment due to presence of impurities.
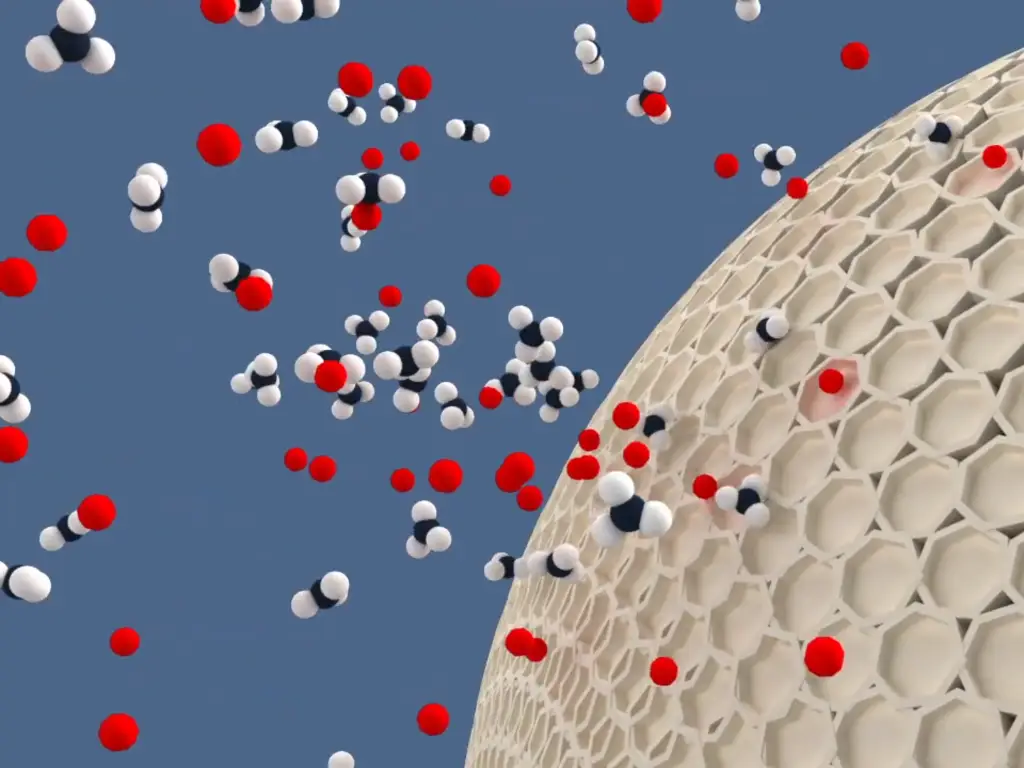
The Cryogenic Distillation Process
High-Pressure and Low-Pressure Distillation Columns
In the cryogenic distillation process, a number of high-pressure and low-pressure distillation columns are used to separate air into its main components. The high pressure column is operated at approximately 6 –8 bars where it separates air into a nitrogen-rich vapour and an oxygen-rich liquid. On top of the high-pressure column, there is the nitrogen rich vapor that feeds the low pressure column with about 1-1.5 bar as operating pressure. In the low pressure column, further purification of nitrogen occurs leaving behind oxygen and argon.
Separation of Nitrogen, Oxygen and Argon
In cryogenic distillation process, separation of nitrogen, oxygen, and argon depends on their different boiling points: Nitrogen has the lowest boiling point (-195.8°C) followed by Argon (-185.8°C) then Oxygen (-183°C). Nitrogen-rich vapour is separated from liquid oxygen in a high-pressure column while in a low-pressure one it is cleaned up for condensing it later on as highly purified nitrogen. The impurities are removed from the bottom of high pressure column where they collect pure argon again.
Refrigeration and Expansion Processes
Refrigeration and expansion processes are key to maintaining cryogenic temperatures necessary for efficient air separation. Typically, the cryogenic distillation process utilizes closed-loop refrigeration systems that involve either nitrogen expansion cycle or mixed refrigerant cycles respectively. For instance, some amount of pressurized nitrogen from the distillation columns is allowed to expand through turbines thereby producing cooling effect required for attaining cryogenics temperatures (nitrogen expansion cycle). Alternatively, mixed refrigerant cycle uses variety of coolants such as methane or ethane among others together with nitrogen gas for effectiveness purposes.
Product Purification and Argon Recovery
The cryogenic distillation process follows the separation of air into its key components, product purification and argon recovery. Further purification of the nitrogen rich vapour from the low pressure column occurs to eliminate any other impurity like oxygen and argon to obtain high purity nitrogen. This purification is done by other distillation steps or use of adsorption techniques.
Argon can be recovered as one important step in the cryogenic distillation since it is a valuable component derived from air separation. Argon recovery through a series of distillation steps and rectification processes takes place in an oxygen-rich liquid at the bottommost part of high-pressure column. Crude argon firstly concentrates in argon column before being further purified in pure argon column for suitable purity level aimed to be achieved. Argon recovery not only enhances economic viability of an air separation process but also helps to satisfy growing industrial demand for it in diverse industries.
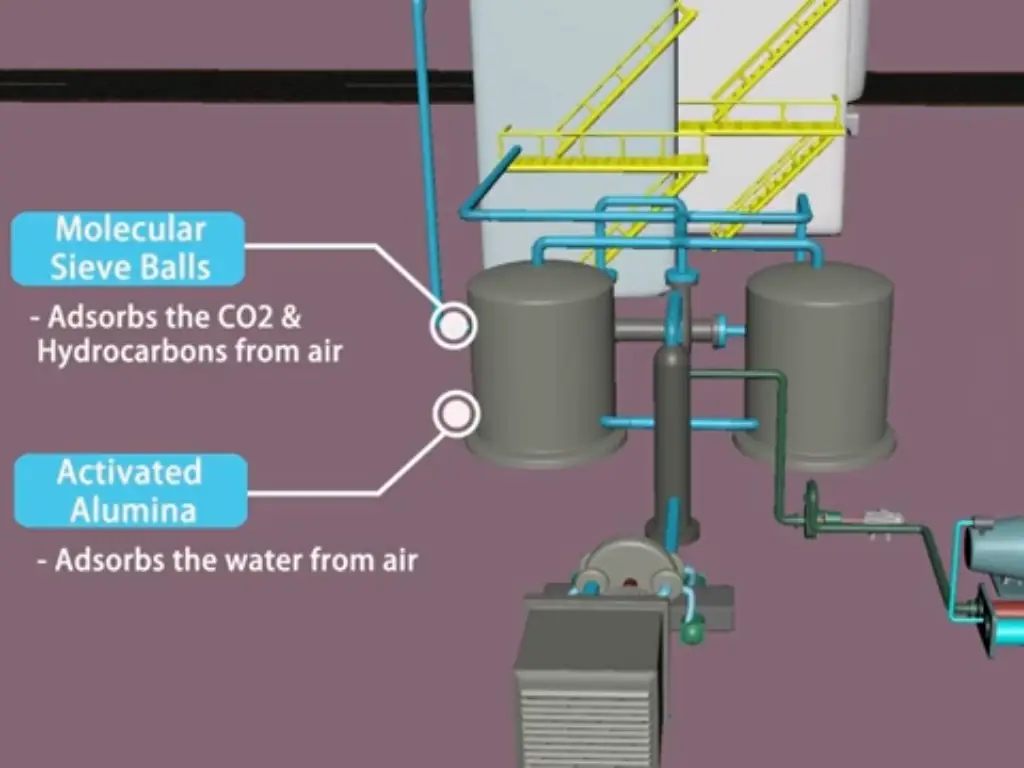
The Role of Molecular Sieves in Post-Processing
In addition, there is a crucial role that molecular sieves also play in the post-processing stage of cryogenic distillation. After air has been separated into its primary components and purification has been initially performed, molecular sieves are used to clean up any remaining contaminants that may still be found in the product streams. It could be such residual water vapor, carbon dioxide and hydrocarbons as were not completely eliminated at the pre-purification step or might have been added during distillation.
Use of molecular sieves during post-processing stages is indispensable for high purity levels required in different industrial applications. In this way, they ensure that final product streams meet strict specifications of purity according to customers’ needs through selective adsorption of any residual impurities. For example, production of high purity nitrogen for the electronics industry can employ molecular sieves to remove trace impurities that would otherwise lower its quality hence negatively affect manufacturing processes.
Energy Efficiency and Cost Reduction
The air separation process being highly energy intensive, energy efficiency becomes a critical issue in cryogenic distillation. Continuously improving on energy efficiency is important for cutting down operating expenses and reducing impact of environmental changes that come with air separation plants. Heat can be better utilized to make the cryogenic distillation process more power efficient. Energy can be saved by using cold nitrogen and oxygen streams from the process as used to pre-cool incoming air. Also, the load on downstream cryogenic equipment can be reduced if high-performance molecular sieves are employed at the pre-purification stage thereby cutting back on additional purification steps.
An alternative method to minimize costs in cryogenic distillation is to employ advanced process control systems. These have complex algorithms and real-time data analyses for optimum operation of the air separation plants so that process parameters are kept within their required ranges. Advanced process control reduces energy consumption, improves product quality and increases overall plant efficiency. A report by International Energy Agency stated that switching to advanced process control systems in air separation plants can decrease up to 10% of energy use thus indicating great potentials for cost reduction in cryogenic distillation (International Energy Agency).
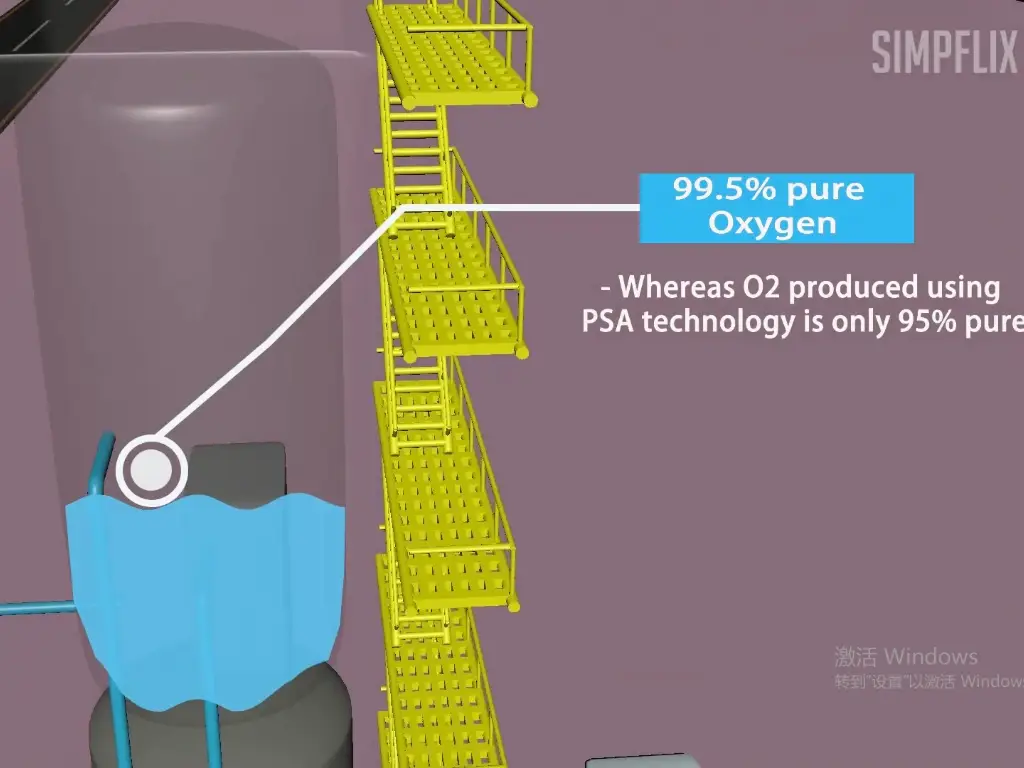
Applications of Cryogenic Distillation in Industries
At some point, many industries employ cryogenic distillation for the production of high purity gases. Before examining the specific applications, it is important to consider how cryogenic distillation compares with other methods of air separation in terms of energy consumed, product purity and plant capacity. The following table illustrates a comparison between three major air separation methods:
Air Separation Method | Energy Consumption (kWh/Nm³) | Product Purity (%) | Typical Plant Capacity (tons/day) |
Cryogenic Distillation | 0.4-0.6 | 99.0-99.999 | 100-5000 |
Pressure Swing Adsorption (PSA) | 0.3-0.5 | 90.0-95.0 | 1-200 |
Membrane Separation | 0.5-1.0 | 90.0-99.0 | 1-100 |
As shown from the table above, cryogenic distillations are the best when it comes to ultra-high purity gases (>99.999%) and are appropriate for mass scale manufacturing (5000 tons/day). It is these benefits that make cryogenic distillation popular in several industries as will be seen later on this document.
Industrial Gas Production
Cryogenic distillation method is widely used in this sector for the separation of large quantities of high purity nitrogen, oxygen and argon. In various industries such as chemical processing metallurgy, electronics and healthcare etc., these industrial gases are applied. By means of cryogenic distillation, the strictest requirements set by those industries can be met because it produces gases with purities that exceed 99.999%.
Combustion Enrichment
In combustion enrichment field also cryogenic distillation has a great role to play. Combustion processes can be optimized through the application of cryogenic distillation process that results into oxygen-enriched air. The use of oxygen-enriched air leads to increased combustion efficiency, reduced fuel consumption, and lower emissions of pollutants such as nitrogen oxides (NOx) and carbon dioxide (CO2).
Specialty Gas Manufacturing
Moreover, the manufacturing process for specialty gases is carried out using cryogenic distillation process which involves very small quantities of highly pure gases needed for specific purposes. These specialty gases include ultra-high-purity (UHP) nitrogen, oxygen, and argon besides rare ones neon, krypton and xenon. Specialty gas production requires purity levels much higher than those present in industrial gases since they may go up to 99.9999%. Cryogenic distillation combined with advanced purification techniques like molecular sieve adsorption or catalytic purification forms one pathway towards production of these ultra-high-purity gases for the semiconductors, solar cells or research industry applications that need them.
Conclusion
The cryogenic distillation process is widely used for industrial gas manufacturing and production, combustion enrichment, and specialty gas preparation. Its capability to produce gases that are more than 99.999% pure renders it an irreplaceable technology in various industries such as chemical processing, metallurgy, electronics, and healthcare.
Molecular sieves have critical roles to play in the cryogenic distillation process both at the pre-purification stage and during post-processing. In this regard, the cryogenic separation of air through distillation processes will be increasingly significant due to the continued escalation of demand for highly pure industrial gases.