En las operaciones a mediana y gran escala, las tecnologías de separación criogénica del aire se utilizan con frecuencia para crear nitrógeno, oxígeno y argón como gases y/o salidas líquidas.
Para fabricar oxígeno y nitrógeno ultrapuros, la separación criogénica del aire es el método recomendado. Para instalaciones de alto índice de fabricación, es la técnica más económica. La tecnología criogénica se utiliza en todas las operaciones que producen productos básicos de gas industrial licuado.
La cantidad de productos gaseosos y líquidos que deben generarse, la pureza necesaria de los productos y las presiones de suministro requeridas afectan a la complejidad del sistema. separación criogénica del aire procedimiento, así como las dimensiones físicas del engranaje y la energía necesaria para hacerlo funcionar.
Este artículo contiene la guía del proceso de separación criogénica del aire. Manos a la obra
¿Qué es la separación criogénica del aire y la destilación?
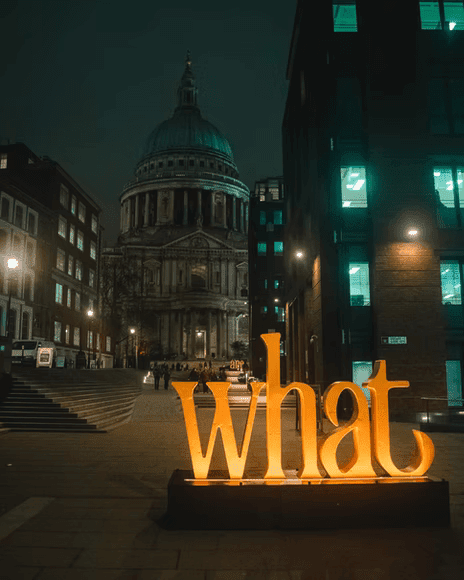
La técnica para separar el nitrógeno y el oxígeno del aire se conoce como destilación criogénica. El Argón también se aísla en algunas circunstancias. El término "criogénico" hace referencia a las bajas temperaturas, mientras que "destilación" se refiere al desacoplamiento de elementos de una combinación utilizando el punto de ebullición de los elementos. Como resultado, los componentes con puntos de ebullición muy bajos se extraen preferentemente a bajas temperaturas en las destilaciones criogénicas. Este proceso produce sustancias de gran purezapero también consume mucha energía.
La caja fría es un enorme contenedor aislado que alberga los pilares de destilación y los intercambiadores de calor que trabajan a temperaturas extremadamente bajas. En el bucle de refrigeración se utiliza el efecto Joule Thomson, también conocido como efecto de estrangulación. El gas pasa a través de una compuerta aislada o un tapón permeable aislado a lo largo de la estrangulación, y la temperatura del gas cambia a medida que se alterna la presión.
Materiales necesarios
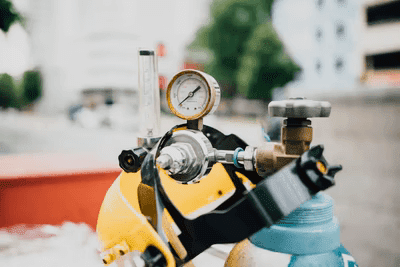
El aire ambiente puede contener hasta 5% de humedad y una variedad de otros gases (normalmente en niveles mínimos) que deben eliminarse en uno o más puntos de la separación y salida del aire. configuración de purificación.
Pasos y proceso de la separación criogénica del aire
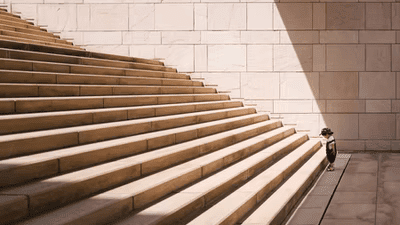
Destilación criogénica del aire: Etapas
- Pretratamiento, compresión y refrigeración del aire entrante.
- Eliminación del dióxido de carbono.
- Conducción de calor para bajar la temperatura de alimentación del aire a niveles criogénicos.
- Destilación por aire.
- Refrigeración
1. Pretratamiento, compresión y enfriamiento del aire entrante
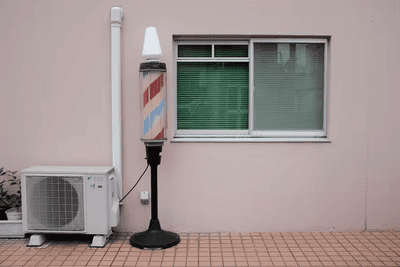
Basado en el mezcla de productos prevista y una fuerza de producto aceptable, el aire se constriñe a entre 5 y 8 bares (entre 75 y 115 psig) en la mayoría de las circunstancias. Tras la última etapa de compresión, el aire comprimido se enfría, y gran parte del vapor del flujo de aire se condensa y elimina, a medida que el aire pasa por una sucesión de refrigeradores de interfase y un postenfriador.
Dado que la temperatura de la canalización de refrigeración obtenible (que casi siempre está restringida por la temperatura de bulbo húmedo o seco del aire ambiente) determina la temperatura final del aire que sale de la estructura de compresión, la temperatura del aire comprimido suele estar muy por encima de la temperatura ideal para la máxima eficacia de la compresión. rendimiento de las unidades aguas abajo. Por ello, a menudo se utiliza un sistema de refrigeración mecánica para enfriar el aire de forma significativa.
2. Eliminación del dióxido de carbono y otras impurezas
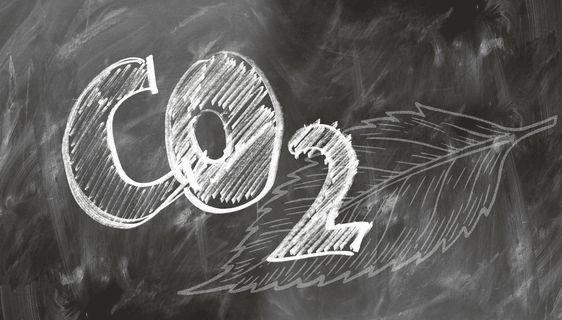
Para alcanzar los criterios de calidad del producto, deben eliminarse ciertos elementos del flujo de aire entrante. El vapor de agua y el dióxido de carbono deben eliminarse del aire antes de que entre en la sección de destilación criogénica de la planta, ya que se solidificarían y acumularían en el exterior del equipo de procedimiento a temperaturas extremadamente bajas.
Tamiz molecular y los intercambiadores reversibles son los dos métodos más utilizados para eliminar el vapor y el dióxido de carbono.
- En casi todas las instalaciones nuevas de desconexión del aire se utiliza una unidad de prepurificación de tamiz molecular para extraer el dióxido de carbono y el agua del flujo de aire mediante la adsorción de estas partículas en el exterior de sustancias de tamiz molecular a una temperatura cercana a la ambiente. Otros contaminantes, como los hidrocarburos, que pueden encontrarse en un entorno industrial pueden eliminarse fácilmente ajustando la composición de sustancias adsorbentes en estos sistemas. Las sustancias adsorbentes suelen conservarse en dos recipientes idénticos, uno de los cuales se utiliza para purificar el aire entrante y el otro se regenera con gas residual limpio. En periodos regulares, las dos láminas cambian de servicio. Cuando se busca un alto índice de extracción de nitrógeno, la prepurificación con tamiz molecular es la elección obvia.
- La otra opción es eliminar el agua y el CO2 mediante intercambiadores de calor "reversibles". Aunque los intercambiadores reversibles suelen considerarse una tecnología "antigua", podrían ser más rentables para plantas de nitrógeno u oxígeno con índices de fabricación más bajos. El suministro de aire comprimido se enfría en dos pares de intercambiadores de calor de aluminio soldado en las plantas que utilizan intercambiadores de calor reversibles.
El aire entrante se enfría mediante transferencia de calor a una temperatura lo suficientemente baja como para que el vapor de agua y el dióxido de carbono se solidifiquen en las superficies del intercambiador de calor. Un sistema de válvulas alterna el funcionamiento de los conductos de aire y gas residual a intervalos regulares. Tras la transición, el gas residual, muy seco y calentado diferencialmente, evapora el agua y sublima la escarcha de dióxido de carbono que se formó durante el intervalo de enfriamiento del aire. Estos gases se liberan de nuevo a la atmósfera, y el intercambiador de calor reversible se prepara para otra inversión del servicio de tránsito una vez que se hayan eliminado por completo.
Los sistemas de absorción en frío se utilizan cuando se emplean intercambiadores de calor inversos para eliminar los hidrocarburos que llegan a las unidades de destilación. (En las unidades de prepurificación, los hidrocarburos contaminantes se eliminan junto con el vapor de agua y el dióxido de carbono cuando se utiliza un "front end" de tamiz molecular).
3. Conducción de calor para bajar la temperatura del aire de alimentación a niveles criogénicos
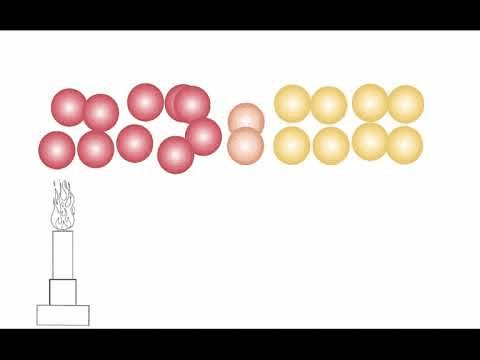
El calor se intercambia entre el aire de alimentación entrante y la salida fría y el flujo de gas residual que sale del procedimiento de destilación criogénica en intercambiadores de calor de aluminio soldado. Los canales de gas de salida se recalientan hasta una temperatura próxima a la del aire ambiente. La cantidad de refrigeración que necesita generar la instalación se reduce recuperando la refrigeración de los canales de productos gaseosos y flujos residuales.
Una técnica de refrigeración que incorpora el crecimiento de uno o más pasos de presión mejorada produce la temperatura extremadamente fría necesaria para la destilación criogénica.
4. Destilación por aire
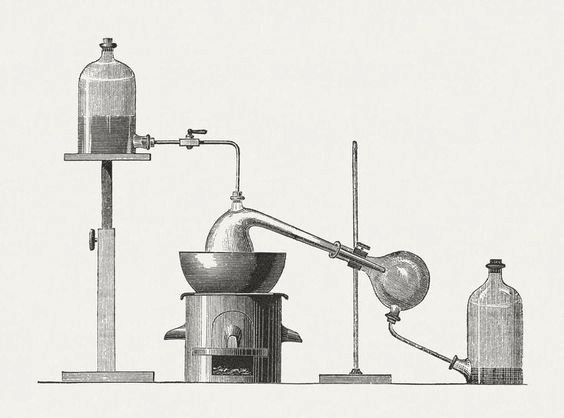
Dos pilares de destilación son utilizados sucesivamente para producir oxígeno como subproducto en el sistema de destilación. Los pilares de "alta" y "baja" tensión (o, alternativamente, los pilares "inferior" y "superior") son los términos más utilizados. Las instalaciones de nitrógeno pueden tener uno o dos pilares, en función de su pureza. Cada pilar de destilación deja salir nitrógeno por la parte superior y oxígeno por la inferior. Cuando el oxígeno contaminado producido en el primer pilar (de mayor presión) es un producto deseado, se refina aún más en el segundo pilar, de menor presión. Si se busca nitrógeno ultrapuro, se utiliza el pilar superior o de baja presión para eliminar casi todo el oxígeno que no se eliminó durante la primera fase de destilación.
El argón tiene un punto de ebullición comparable al del oxígeno, por lo que si sólo se necesitan oxígeno y nitrógeno como subproductos, se quedará preferentemente con la salida de oxígeno. En un sistema convencional de dos pilares, esto restringe la pureza del oxígeno a alrededor del 97%. Si se permite oxígeno de baja pureza (por ejemplo, para mejorar la combustión), la pureza del oxígeno podría ser tan reducida como 95%. Sin embargo, el argón debe eliminarse de la unidad de destilación si se desea oxígeno de alta pureza.
Cuando se necesita argón, se extrae en una posición de la corriente de baja presión en la que la concentración de argón es máxima. El argón extraído se trata en una torre de destilación de argón crudo de "extracción lateral" incorporada al pilar de baja presión. La corriente de argón contaminado puede ventilarse, tratarse in situ para eliminar tanto el oxígeno como el nitrógeno y producir argón "puro", o almacenarse como líquido y entregarse a una "destilería de argón" distante. La opción viene determinada principalmente por la cantidad de argón accesible y por un análisis de costes y beneficios de las distintas opciones. Como orientación básica, la purificación de argón es más rentable cuando se generan al menos 100 toneladas de oxígeno al día.
Para fabricar argón puro a partir de argón bruto se utiliza una técnica de varias etapas. El método convencional consiste en utilizar un componente "desoxo" para eliminar el oxígeno 2 - 3 % existente en el argón bruto. Se trata de un pequeño procedimiento de varios pasos que combina químicamente el oxígeno con hidrógeno en un recipiente que contiene un catalizador y, a continuación, elimina el agua subsiguiente (tras el enfriamiento) en un secador de tamiz molecular. La corriente de argón sin oxígeno se destila a continuación para eliminar el nitrógeno sobrante y el hidrógeno insoluble en una unidad de destilación de "argón puro".
Ha surgido una segunda opción de fabricación de argón como resultado de los avances en la tecnología de destilación de columna empaquetada: la recuperación de argón completamente criogénica, que emplea una columna de destilación muy alta (pero de diámetro diminuto) para lograr el difícil desacoplamiento argón/oxígeno. La variación relativamente modesta de los puntos de ebullición entre el oxígeno y el argón requiere múltiples etapas de destilación para el argón.
La cantidad de oxígeno tratado en el sistema de destilación, así como otras variables que influyen en la tasa de recuperación, limitan el volumen de argón que puede producir una instalación. Estos factores incluyen el volumen de oxígeno líquido producido y la consistencia de los parámetros de funcionamiento de la instalación. La generación de argón no puede superar el 4,4 por ciento de la tasa de alimentación de oxígeno (en volumen) o el 5,5 por ciento en peso debido a la proporción de gas existente de forma natural en el aire.
Los intercambiadores de calor frontales se utilizan para redirigir los productos gaseosos fríos y los flujos de residuos procedentes de las torres de separación de aire. Enfrían el aire entrante a medida que se calientan hasta alcanzar una temperatura cercana a la ambiente. Como ya se ha dicho, la transferencia de calor entre los flujos de entrada y de producto reduce la carga neta de refrigeración de la instalación y, como resultado, utilización de la energía.
5. Refrigeración
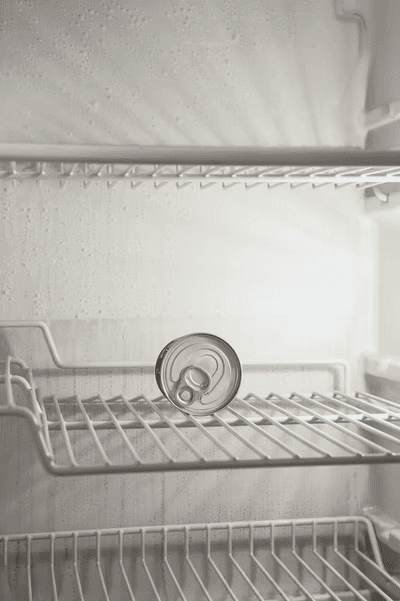
Para tener en cuenta las fugas de calor en los aparatos fríos y el escaso intercambio de calor entre las corrientes gaseosas entrantes y salientes, la refrigeración se produce a temperaturas criogénicas.
El ciclo de refrigeración utilizado en las instalaciones criogénicas de separación de aire es, en teoría, idéntico al que se aplica en los sistemas de aire acondicionado domésticos y de automoción. Según el tipo de instalación, se baja la presión de una o varias corrientes de alta presión (nitrógeno, gas residual, gas de alimentación o gas de salida), enfriando la corriente. La caída de presión (o expansión) tiene lugar en el interior de un expansor para mejorar la refrigeración y la eficacia energética industrial.
La temperatura de la corriente de gas se reduce más cuando se le quita energía durante el crecimiento que cuando simplemente se expande mediante una válvula. La energía del expansor puede utilizarse para alimentar un condensador de procedimiento, un generador eléctrico u otro dispositivo que consuma mucha energía, como una bomba de aceite o un soplador de aire.
Las salidas gaseosas de una fábrica criogénica de oxígeno/sistema de separación de aire suelen salir de la caja fría (el contenedor aislado que contiene las secciones de destilación y otra maquinaria que funciona a temperaturas muy bajas) a temperaturas cercanas a la atmosférica, pero a una presión reducida; a menudo, justo por encima de un ambiente (absoluto). El procedimiento de separación y purificación es más eficaz en general cuando se reduce la presión de salida.
Aunque una menor presión favorece una menor demanda de energía para la separación, si las salidas deben suministrarse a mayor presión, se necesitarán compresores de producto o una de las diversas alternativas de ciclo para alimentar nitrógeno u oxígeno a mayor presión de distribución directamente desde la caja fría. Estas técnicas de mayor presión de suministro pueden ser más rentables que la separación acompañada de compresión, ya que no requieren un compresor de producto ni su electricidad.
Consejos eficaces y de seguridad
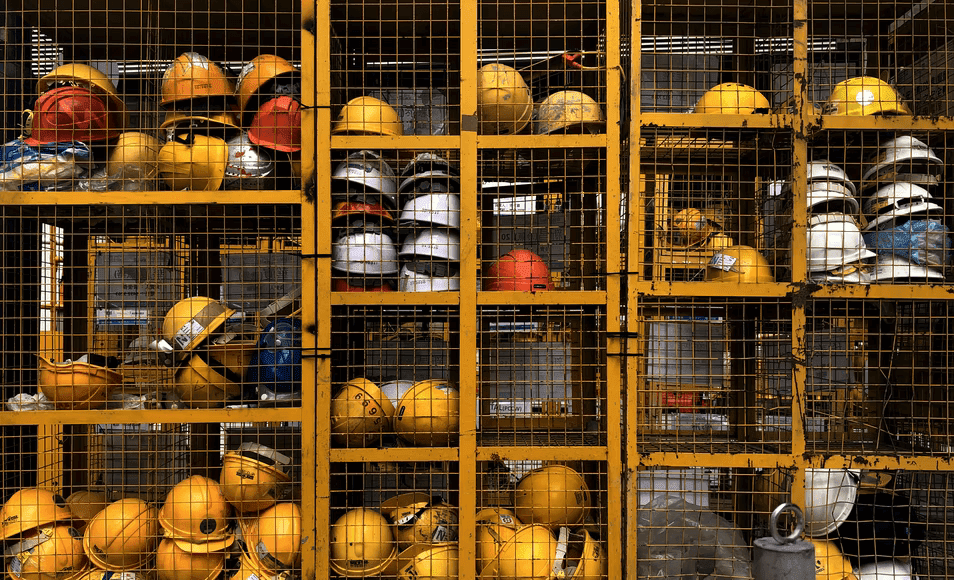
Antes de iniciar la construcción y el diseño de cualquier sistema o proceso criogénico, realice un análisis formal de riesgos. Determine los riesgos y cómo los abordará. Plantee escenarios hipotéticos. Recuerde que la maquinaria puede fallar, los fluidos criogénicos pueden convertirse en gas rápidamente, las válvulas pueden tener fugas o manipularse incorrectamente y los vacíos pueden funcionar mal. Independientemente del tamaño o la complejidad del sistema criogénico, debe realizarse esta evaluación.
Desde el principio, incluya la seguridad en sus equipos y procedimientos. Incorporar elementos de seguridad al final de la fase de diseño puede ser costoso y requerir mucho tiempo, y es posible que se pasen por alto peligros. Hay que tener en cuenta que siempre es preferible eliminar un peligro mediante el diseño de ingeniería que mejorarlo.
Incluso los especialistas pueden pasar algo por alto o cometer un error. Es fundamental que la seguridad de su sistema criogénico sea evaluada por otros, ya sean otros compañeros de trabajo, expertos externos u organismos de revisión formales, para mejorar las posibilidades de un sistema seguro.
Evalúe siempre la probabilidad de Peligros por Deficiencia de Oxígeno cuando trabaje con líquidos criogénicos o gases inertes, independientemente de lo pequeña que sea la cantidad. Establezca que dicho peligro no existe mediante la evaluación o aplique las mejoras o mitigaciones de diseño pertinentes para eliminar o reducir el peligro. Debido al enorme volumen de gas producido incluso por pequeños volúmenes de líquido criogénico y a la posibilidad de que, a niveles de oxígeno suficientemente bajos, el primer síntoma fisiológico pueda ser una rápida pérdida de conciencia, acompañada de coma y muerte, las dificultades de ODH son especialmente graves.
A temperaturas criogénicas, utilice sólo sustancias que hayan demostrado funcionar a esas temperaturas. Tenga en cuenta que las sustancias que se supone que funcionan a temperatura ambiente (como las paredes exteriores de los recipientes de vacío) podrían alcanzar temperaturas criogénicas en determinados mecanismos de fallo durante la evaluación de riesgos.
Verifique que todas las personas que operan con equipos criogénicos o cerca de ellos, incluso los usuarios ocasionales o casuales, han recibido el grado requerido de formación en seguridad criogénica y riesgos por deficiencia de oxígeno.
Lleve siempre el equipo de protección personal adecuado y respete los procesos operativos establecidos. Tomar atajos suele dar lugar a percances.
Lo esencial
En el proceso de separación criogénica del aire, los agentes secantes son una necesidad. Es necesario trabajar con un planta de fabricación que pueden ofrecerle productos de alta calidad. Póngase en contacto con nosotros y estaremos encantados de ofrecerle nuestros servicios.