¿Qué es la separación de petróleo y gas?
El proceso de separación de petróleo y gas es crucial en la industria petrolera, ya que ayuda a separar el petróleo crudo, el gas natural y el agua para su posterior procesamiento y transporte. Cuando el petróleo y el gas salen de la boca del pozo, se encuentran en un sistema multifásico compuesto por hidrocarburos, agua y, en ocasiones, sólidos. Cuando no hay separación, el refinado y el transporte posteriores se ven afectados, lo que provoca problemas operativos y costes elevados.
El objetivo principal del proceso de separación de aceites es maximizar la pureza de cada componente con el menor gasto de energía y tiempo. Una separación eficaz mejora la productividad, reduce el desgaste de los equipos y ayuda a cumplir los requisitos legales de impacto ambiental. Funciona como el sistema de semáforos de una ciudad, donde cada componente es guiado al lugar que le corresponde para evitar atascos y retrasos. Esto no sólo salvaguarda la infraestructura, sino que también mejora la eficacia de la recuperación de hidrocarburos, que es un elemento clave de la actual industria del gas.
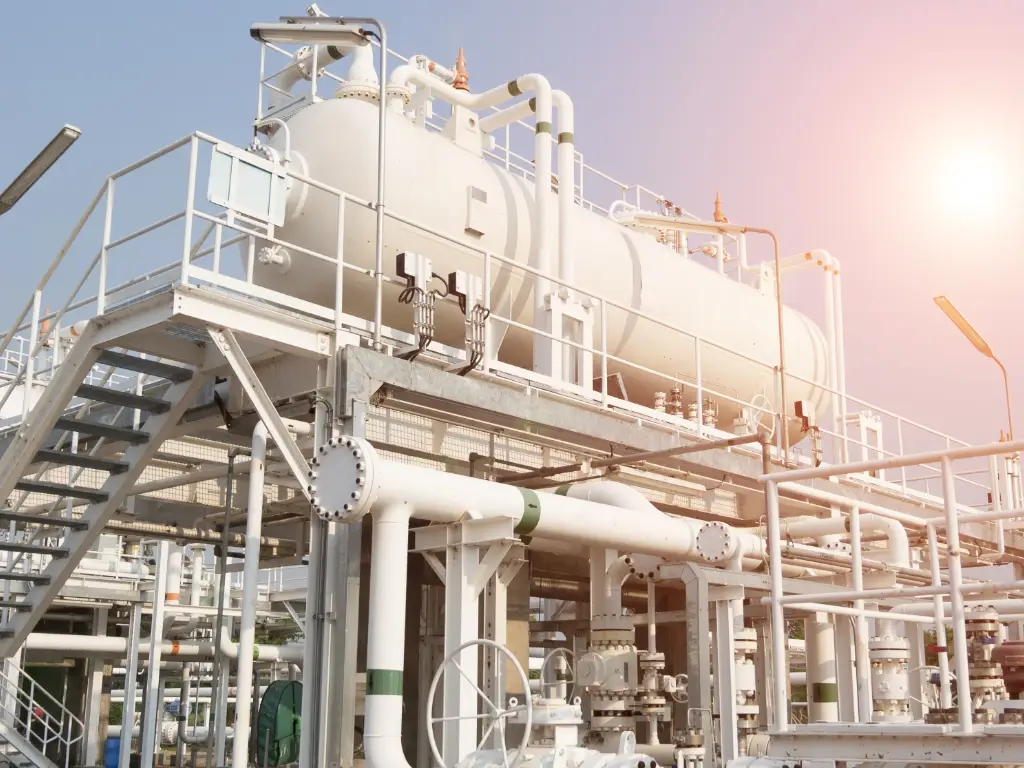
Tipos de equipos y funciones clave
Separadores bifásicos
Los separadores bifásicos se utilizan para separar el fluido del pozo en dos fases, que son gas y líquido, que en este caso son petróleo y agua. Funcionan sobre la base de la diferencia de densidad y el desplazamiento por gravedad. Cuando entra la mezcla, el gas sube a la sección de gas y se libera, mientras que el líquido se queda en la base del depósito. Estos separadores se utilizan en la primera etapa de separación en la industria del petróleo y el gas. Se utilizan en tanques de almacenamiento, boca de pozo e instalaciones de producción donde el contenido de agua es bajo. Su diseño sencillo los hace rentables, pero pueden necesitar un tratamiento posterior si se va a eliminar una gran cantidad de agua.
Separadores trifásicos
Los separadores trifásicos dividen la corriente del pozo en gas, petróleo y agua, lo que resulta esencial en yacimientos con un alto contenido de agua. Funcionan según el principio de que el agua, más densa, se hunde en el fondo, el petróleo forma la capa intermedia y el gas flota en la superficie. Por eso es importante controlar los niveles del líquido y el flujo del gas para lograr la mejor separación. Estos separadores se utilizan mucho en plataformas marinas, yacimientos petrolíferos y plantas de procesamiento de gas donde se desea una separación de gran pureza. Aunque son más complicados que los separadores bifásicos, ofrecen un mejor nivel de separación y mejoran la eficacia del procesamiento posterior.
Separadores ciclónicos
Los separadores ciclónicos funcionan según el principio de la fuerza centrífuga para separar el gas del líquido. La mezcla entrante se encuentra a gran velocidad y las partículas líquidas más pesadas se desplazan hacia las paredes del separador y luego hacia abajo, mientras que el gas más ligero sube. Debido a su pequeño tamaño, son adecuados para su uso en plataformas marinas y otras zonas donde el espacio y el peso son limitados. Son eficaces para manejar caudales de gas elevados y se ven menos afectados por las fluctuaciones del caudal. Pero pueden no ofrecer una eficacia de separación tan alta como los separadores por gravedad en casos de niebla fina o diferencias de densidad bajas.
Separadores verticales
Los separadores verticales se basan en el principio de la gravedad para permitir la separación del gas del líquido. El gas sube a la parte superior del recipiente mientras que el líquido se acumula en la base del recipiente debido a la fuerza de la gravedad. Su diseño es especialmente ventajoso cuando la relación gas-líquido es elevada, ya que el flujo ascendente del gas ayuda a la eliminación del líquido. Ocupan menos espacio en el suelo, lo que los hace ideales para entornos marinos y con limitaciones de espacio. Sin embargo, su eficacia de separación puede ser inferior a la de los separadores horizontales. Se aplican ampliamente en la separación en boca de pozo, donde la producción de gas suele ser elevada.
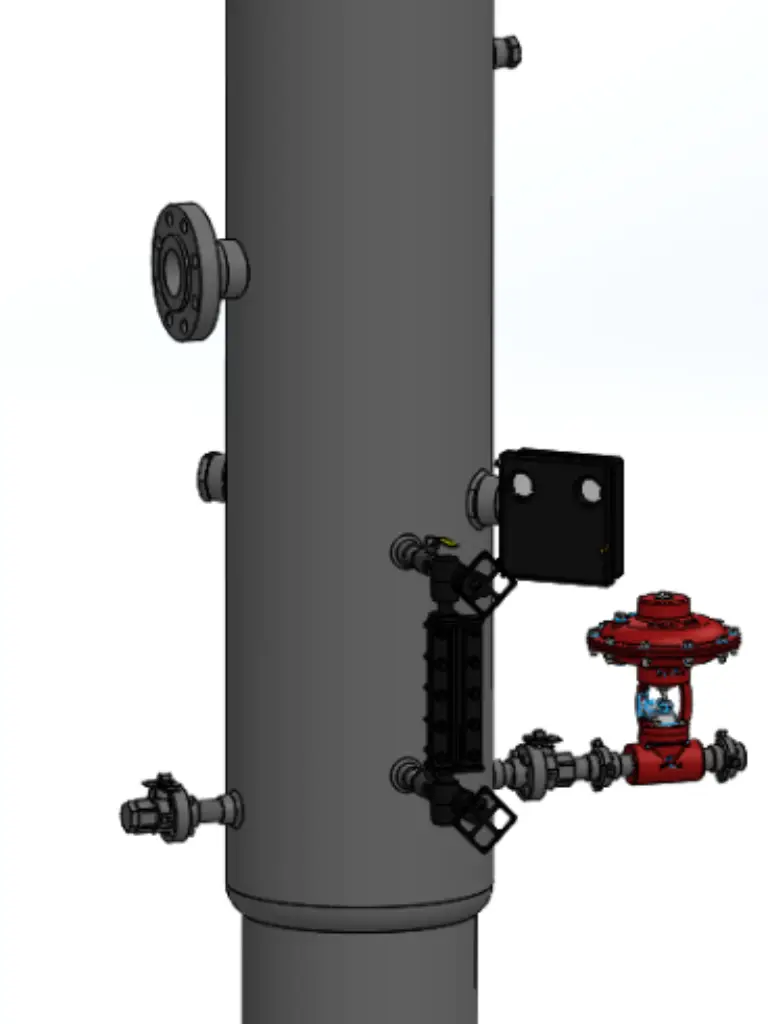
Separadores horizontales
Los separadores horizontales también ofrecen mayores longitudes de flujo, lo que mejora la separación de petróleo, gas y agua. Esto se debe a que el mayor tiempo de retención permite una mejor separación de las distintas fases. Estos separadores son adecuados para su uso en sistemas que manejan grandes volúmenes de líquido y tienen proporciones relativamente estables de petróleo y gas. Tienen un tamaño mayor que les permite manejar más volumen, por lo que son adecuados para instalaciones centrales de procesamiento y centros de recolección de yacimientos petrolíferos. Sin embargo, necesitan más espacio y soporte estructural que los separadores verticales. Se utilizan mucho en instalaciones de producción de petróleo en tierra, donde la separación eficaz de fases es crucial para el procesamiento posterior.
Proceso de separación de petróleo y gas
Separación de entrada
Cuando el fluido del pozo entra en el sistema de separación, suele consistir en una mezcla de petróleo, gas y agua, a menudo a alta presión. El fluido se dirige a través de la tubería de entrada al separador de primera etapa, donde comienza el proceso de separación. Dispositivos mecánicos como los desviadores de entrada ayudan a distribuir el fluido uniformemente, evitando turbulencias y garantizando un proceso de separación eficaz. El paso inicial es crucial, ya que prepara el terreno para las fases posteriores al reducir el arrastre de gas en el líquido y garantizar un flujo estable para un procesamiento eficaz aguas abajo.
Separación primaria de gas-líquido
En esta fase, se utiliza la fuerza de la gravedad para ayudar en la separación de las fases fluidas en función de sus densidades. El gas, al ser más ligero, sube a la sección de gas, mientras que los hidrocarburos líquidos se depositan en el fondo del tanque. Algunos separadores de gas emplean la separación ciclónica o la separación centrífuga como forma de aumentar la eficacia, especialmente en los casos en los que la separación debe realizarse rápidamente. El gas se deja subir a la parte superior del separador y se canaliza al siguiente proceso, mientras que el líquido se canaliza a la siguiente fase de separación. Una instrumentación adecuada también ayuda a controlar el caudal y las variaciones de presión.
Separación de agua y aceite
Tras la etapa inicial de eliminación de gases, el líquido que queda es una mezcla de aceite y agua, por lo que es necesario separarlo. En los separadores, el agua, al ser más densa, se deposita en el fondo, el aceite forma la capa intermedia y el gas restante flota en la parte superior. En algunos casos, es necesario romper emulsiones estables con la ayuda de demulsificantes. A continuación, los hidrocarburos líquidos separados se transportan a las instalaciones de procesamiento, mientras que el agua se trata para volver a utilizarla o se inyecta de nuevo en el yacimiento. La optimización de la separación de agua y petróleo aumenta el nivel de cumplimiento de las normas medioambientales e incrementa el rendimiento de los hidrocarburos.
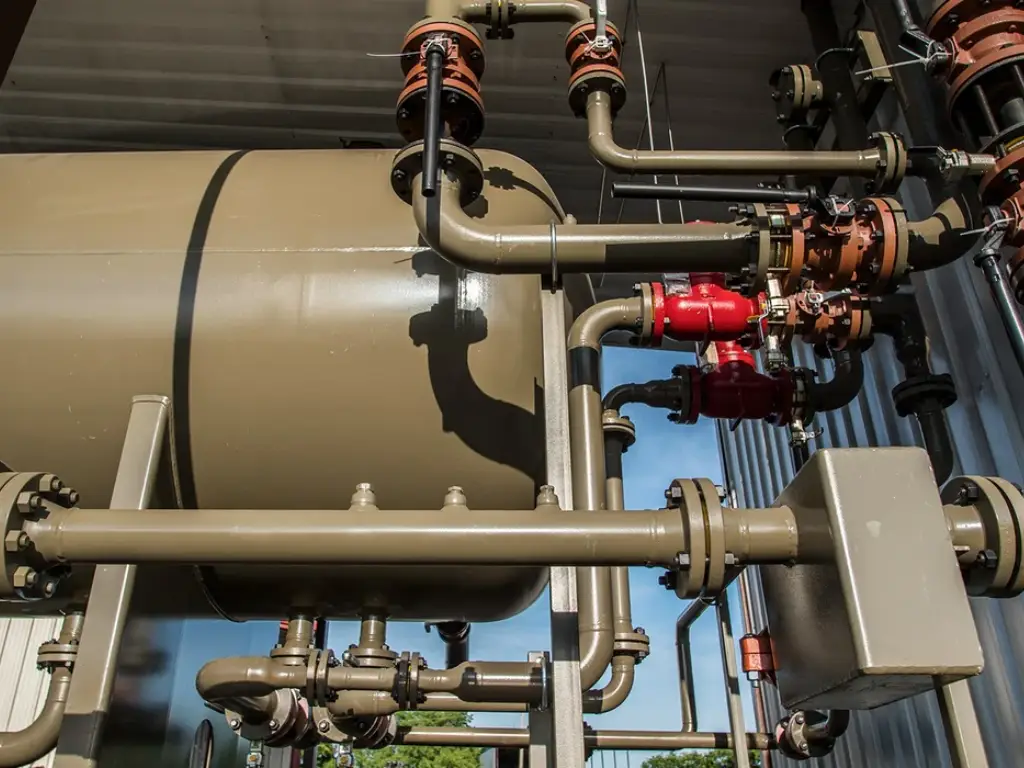
Acondicionamiento y deshidratación de gases
El gas separado puede contener vapor de agua y dióxido de carbono (CO₂) que deben eliminarse para evitar la corrosión de las tuberías y la formación de hidratos. La deshidratación profunda se consigue normalmente utilizando tamices moleculares y sistemas de deshidratación con glicol. También puede comprimirse mediante compresores para elevar su presión y transportarlo al lugar deseado. Junto con los procesos de calentamiento o enfriamiento, el acondicionamiento del gas garantiza que se encuentre a la psi adecuada para su posterior procesamiento o venta. Este paso es muy importante en la purificación del gas y también en su transporte por gasoductos.
Almacenamiento y transporte de líquidos
Después, el petróleo procesado se guarda en tanques de almacenamiento antes de ser enviado a las refinerías para su posterior procesamiento. El agua que se separa de la corriente de petróleo se trata y luego se deja salir o se inyecta de nuevo en el depósito para mantener la presión. Las válvulas y los sistemas de control del calentamiento ayudan a mantener la estabilidad del petróleo y a evitar la formación de cera o hidratos durante el almacenamiento y el transporte. El proceso de transporte también debe cumplir requisitos de seguridad y medioambientales para evitar vertidos y mejorar el flujo de petróleo en las redes de distribución.
Segunda fase y separación final
En algunos casos, hay una segunda etapa de separación, especialmente en yacimientos de petróleo a baja presión o con un corte de agua elevado. Esta etapa puede incluir el flasheo, en el que una caída repentina de la presión hace que los gases disueltos pasen a la fase de vapor y aumente la estabilidad del petróleo. También puede utilizarse el calentamiento para eliminar los hidrocarburos ligeros residuales, como el propano, el etano, el butano, etc., para cumplir los requisitos de calidad de los oleoductos. La purificación final se realiza mediante depuradores avanzados y separadores secundarios para garantizar la eliminación de cualquier impureza restante antes del almacenamiento o el transporte.
¿Qué papel desempeña el tamiz molecular en el proceso de separación?
Del proceso anterior de separación de petróleo y gas se desprende que los tamices moleculares son muy importantes en el proceso de deshidratación hasta alcanzar las especificaciones requeridas tanto del petróleo crudo como del gas natural. Durante la separación, los hidrocarburos crudos contienen vapor de agua que provoca la corrosión de las tuberías, la formación de hidratos y la reducción de la eficacia del procesamiento.
Los tamices moleculares 3A, 4A, 5A y 13X se utilizan en unidades de adsorción para eliminar el agua de las corrientes de gas natural con el fin de evitar la formación de hidratos y mejorar el tratamiento posterior. Los tamices moleculares se utilizan en combinación con compresores en plantas de separación para lograr el mejor resultado en el tratamiento del gas. También puede utilizarse la deshidratación con glicol, pero los tamices moleculares proporcionan una deshidratación más profunda, necesaria en el procesamiento de propano, etano y butano.
A continuación se comparan los distintos tipos de tamices moleculares utilizados en la deshidratación del gas natural:
Tipo de tamiz molecular | Tamaño de poro (Å) | Aplicación | Ventajas |
3A | 3 | Deshidratación de gas natural y GLP | Alta selectividad del agua, evita la coadsorción de hidrocarburos |
4A | 4 | Deshidratación general de gases, eliminación de CO₂ | Adsorción eficaz del agua, uso versátil |
5A | 5 | Separación de hidrocarburos, secado de gases | Adecuado tanto para la deshidratación como para la separación de hidrocarburos |
13X | 10 | Eliminación de CO₂ y H₂S, deshidratación profunda. | Gran capacidad de adsorción, polivalente |
Tamices moleculares Jalon para un rendimiento superior
Jalon es un fabricante de tamices moleculares que ofrece una serie de tamices moleculares de alto rendimiento para la separación de petróleo y gas con el fin de satisfacer las necesidades de deshidratación y eliminación de impurezas. Su tamiz molecular 3A es ideal para la deshidratación de gas natural, no adsorbe hidrocarburo y, por tanto, no altera la composición. Los tamices moleculares 4A y 5A adsorben mejor el agua y los hidrocarburos ligeros para aumentar la pureza del gas. Cuando es necesario separar tanto el CO₂ como el H₂S, el mejor adsorbente es el tamiz molecular 13X. Han utilizado sus tamices moleculares en diferentes plantas de petróleo y gas de todo el mundo y han ofrecido las siguientes ventajas:
- Absorción de humedad superior para ciclos de deshidratación prolongados.
- Soluciones personalizables adaptadas a necesidades operativas únicas.
- Riguroso control de calidad que garantiza la coherencia y la fiabilidad.
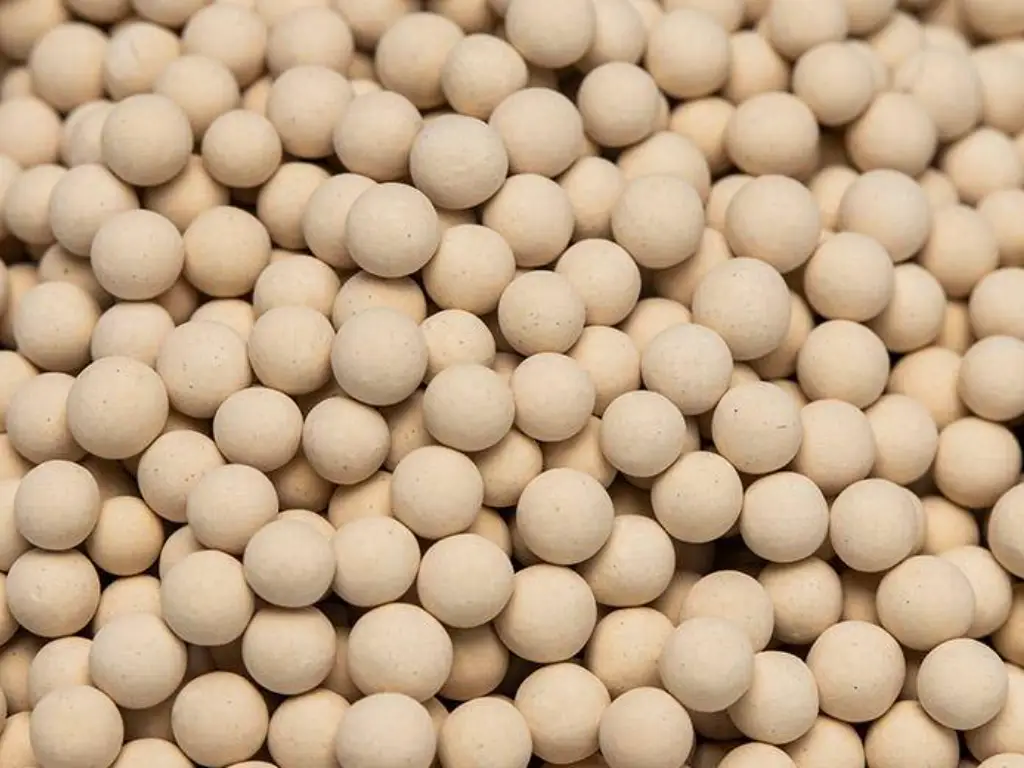
Optimización de los procesos de separación y tendencias futuras
La optimización de la separación de petróleo y gas es un proceso que debe realizarse de forma continua. Algunas de las formas de conseguir eficiencia y ahorrar energía son la separación en varias etapas, la automatización de los controles del proceso y la supervisión continua. En el futuro, la industria está cambiando gradualmente hacia el uso de métodos de separación más limpios, más sostenibles y menos peligrosos para el medio ambiente. Los tamices moleculares serán el componente principal de la nueva generación de tecnologías de tratamiento de gases, que serán más eficaces y rentables.
Conclusión
La separación de petróleo y gas es un proceso importante que se aplica para aumentar el rendimiento de los hidrocarburos y la fiabilidad del sistema. Comprendiendo el proceso de separación, seleccionando el equipo adecuado y utilizando nuevos tamices moleculares, los operadores pueden obtener altos índices de producción a bajo coste. Los tamices moleculares de Jalon ofrecen el máximo nivel de deshidratación, mejor calidad del gas y productividad para su empresa. A medida que el sector avanza hacia la sostenibilidad y la eficiencia energética, soluciones innovadoras como los tamices moleculares seguirán dando forma al futuro del petróleo y el gas.