What Is Butane and Where Does It Come From? Understanding Its Properties and Sources
Butane is an interesting hydrocarbon that has a wide application in various industries and in homes. It is an alkane that is composed of four carbon atoms and ten hydrogen atoms, which is represented by the chemical formula C4H10. Butane exists in two structural forms: n-butane and isobutane, which are structurally different but chemically similar types of butane.
This hydrocarbon is usually in the liquid state under pressure but becomes a gas at room temperature. It is usually produced from natural gas or petroleum, which are known to contain a variety of hydrocarbons. Butane is one of the gases that are found in crude oil and is separated during the refining process that yields petroleum gas and other energy related products such as propane and methane.
Butane has many uses because of its properties. Due to its ability to burn cleanly and efficiently, it is a major source of energy, as a refrigerant, a propellant, and as a feedstock for chemical products, it is an important industrial commodity. However, butane has its drawbacks: it is flammable and its combustion can release carbon monoxide and other dangerous substances if burned inadequately.
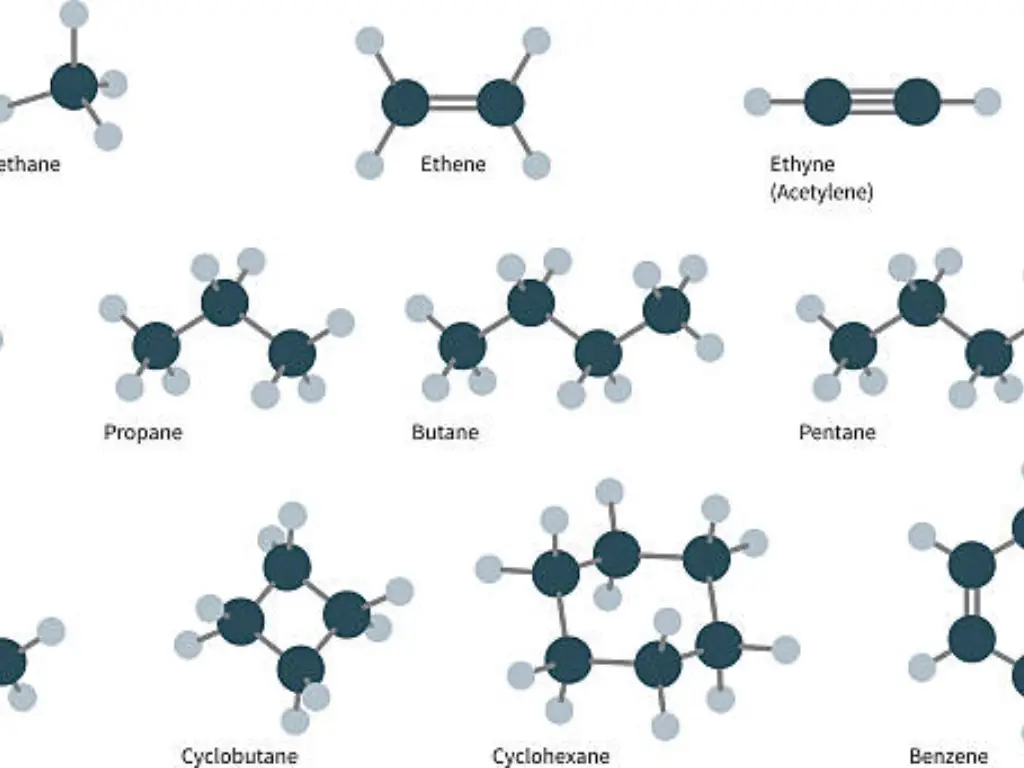
The Extraction Process: How Butane Is Separated From Natural Gas
Butane is mainly extracted from natural gas which is a combination of light hydrocarbons such as methane, ethane, propane, and butane. The process begins with the extraction of natural gas from subterranean reservoirs. This raw gas is not only composed of hydrocarbons but also contains other components like water vapor, sulfur compounds, and other undesirable components. Before it can be used in the next stage of the process, these impurities are taken out and the gas is cooled to very low temperatures. At these temperatures, the heavier hydrocarbons such as butane turn into liquid form and hence easier to extract.
The next step is cryogenic separation where the gas is taken through a low temperature separation column. In this column, components are divided according to their boiling point. Butane, which has a higher boiling point than methane and propane, condenses lower in the column and is collected. After isolation, butane goes through other processes such as absorption and distillation to purify it to meet industry standards.
The final product can then be fractionated to the required forms, normal butane or isobutane as the case may be. High-tech monitoring systems are employed throughout to guarantee the effectiveness of separation and quality. This elaborate process makes it possible to obtain butane that can be used in various industries and commercial activities.
Refinement and Purification: How Crude Butane Is Processed for Industrial Use
Processing crude butane into high-purity butane for industrial applications is a multi-step process requiring precision, advanced technology, and careful separation techniques. Each step in this process plays a critical role in transforming raw materials into a refined product suitable for uses in petrochemicals, refrigeration, and fuel industries. Here’s an in-depth look at how this transformation occurs:
Step | Objective | Techniques Used |
Cleaning and Differentiation | Removing impurities and separating natural gas liquids (NGLs) | Water scrubbing, desulfurization, drying equipment (e.g., molecular sieves 4A, 5A types) |
Isomerization | Converting n-butane into isobutane | Catalysts (e.g., platinum or HZSM-5 molecular sieves) |
Catalytic Cracking | Breaking down heavier hydrocarbons into butane and other light hydrocarbons | High-temperature operation, zeolite catalysts, drying equipment (e.g., molecular sieves 5A, 13X types) |
Hydroprocessing | Removing residual olefins, sulfur, and other impurities | Hydrogen treatment with catalysts (e.g., nickel-molybdenum or cobalt-molybdenum) |
Final Purification | Achieving high-purity butane (typically 99.5% or higher) | Cryogenic distillation, molecular sieves (e.g., 5A and 13X types) |
Step 1: First Cleaning and Differentiation
In separation process of crude butane, the first step involves the purification step in order to eliminate the contents that are in liquid state such as; water, sulfur, and the heavier hydrocarbons. Such impurities may deteriorate equipment that lies downstream, affect catalysts within the process and even degrade the quality of the final product. Usually use basic techniques include water scrubbing. and desulfurization units that get rid of corrosive matters like hydrogen sulfide (H₂S), particulates and soluble impurities that would otherwise harm the catalyst used at the subsequent process.
A critical part of these steps is drying where it is a requirement that the content of the water within the material needs to be less than 0.1 percent for industrial uses. Molecular sieves especially the 4A and 5A types are the most suitable desiccants for this purpose. Their uniform pore structure selectively adsorbs water without affecting hydrocarbons, which makes the process accurate and stable. Compared to the other desiccants for instance silica gel or activated alumina, the molecular sieves can custom fit for even the tiniest levels of moisture, and can function optimally at high temperatures without degrading, thereby reducing the expense on maintenance.
Crude butane is also subjected to fractional distillation, to remove it from other natural gas liquids (NGLs) such as propane and pentane. This differentiation is necessary to avoid contamination since each NGL has its use in the industrial process. Fractionation columns work under well regulated conditions to separate n-butane and isobutane streams for further treatment.
Step 2: Isomerization – Transforming n-Butane into Isobutane
After crude butane is cleaned and separated, the next major process is isomerization. In this process, normal butane (n-butane) is converted into isobutane which is a more branched isomer of the molecule and has more value in industrial uses. Isobutane is one of the most preferred feedstocks in alkylation processes for generating high octane gasoline.
The isomerization process is carried out by passing n-butane through a reactor containing a catalyst which is platinum or chlorinated alumina at temperatures between 100-250°C and moderate pressures. Some of the acidic molecular sieves like HZSM-5 which can also be used as catalysts for isomerization. While they are less effective than platinum or chlorinated alumina, they are more economical and suitable for low pressure environments.The catalyst changes the molecular configuration of n-butane but does not alter its composition. This conversion rate tends to be in the range of 85–95% depending on the process conditions.
The produced blend of n-butane and isobutane is then fed to a separation section where isobutane is separated by distillation. The unconverted n-butane is returned to the reactor to increase efficiency and minimize loss of product.
Step 3: Catalytic Cracking – Producing Butane from Higher Hydrocarbons
However, not all butane is derived from raw materials. Sometimes catalytic cracking is used in order to obtain butane from the heavier hydrocarbons including naphtha or gas oil. It is especially useful for when the raw butane supplies are wanting or when the objective is to optimally use feedstocks. The formation of valuable material from large hydrocarbon molecules is the main advantate of catalytic cracking which produces butane, propane and ethylene.
It takes place at elevated temperatures (500–550°C) and pressures and employs zeolite-based catalysts that favor the cleavage of carbon-carbon bonds. Zeolite catalysts are preferred because of their effectiveness and durability. They are able to generate and maintain high returns and productivity together with high selectivity which is necessary for this process.
Once the cracking is done, the crude product mix comes through a distillation tower where butane is separated from other fractions. At this stage, it’s crucial to remove moisture by either air-drying or oven drying. For this purpose, molecular sieves, especially the 5A and 13X types, are preferred because of their high water adsorption selectivity and thermal stability under severe conditions.
Although activated alumina can also be used as a secondary drying agent, and it is effective in treating acidic impurities, molecular sieves are more effective and selective. The integration of efficient cracking and effective drying guarantees a steady source of high purity butane to meet industrial demand even when direct sources are scarce.
Step 4: Hydroprocessing
Hydroprocessing steps are then used to treat the rich butane stream to enhance the quality of the product and to address any remaining impurities. This process involves mixing of hydrogen with butane with addition of a catalyst like nickel-molybdenum or cobalt-molybdenum at a temperature of between 300 – 400 degree Celsius and pressure of between 2000 psi and higher.
The main purpose of hydroprocessing is to remove any residual levels of olefinic material, sulfur, nitrogen and oxygen containing compounds. Thus, fluctuations of olefins even in quantities smaller than 0.01% can affect butane stability when stored and utilized. Hydroprocessing brings down these levels to nondetectable levels to meet the required industrial standards of the product.
Further, this step also improves the chemical stability of the butane so as to allow for its storage and transport over long distances. Hydroprocessing reduces the risks of degradation or polymerization, which are important in determining the quality of the final product since it eliminates reactive impurities.
Step 5: Separation and Purification
The last step in refining crude butane involves performing such processing as is necessary to achieve the likely levels of purity of butane needed for any specific application, ranging from as low as 99.5% for commercial uses down to 99.9% and lower for more specialized uses such as in pharmaceuticals or aerosol props. At this stage, small amounts of water, carbon dioxide, and some hydrocarbons must be separated in order to meet increasingly high quality and performance requirements.
Further separation of butane from propane ethane and heavier hydrocarbons is by the use of more complex processes like cryogenic distillation. These systems run in very high vacuum and normally, the temperature range used is as low as – 100 °C in order to condense butane. For instance, cryogenic columns can bring down propane concentrations to well below 50 ppm which is important for many applications that necessitate highly purity levels.
In this phase, molecular sieves, particularly 5A and 13X types, are essential for the elimination of such minor contaminants as water and carbon dioxide. Due to their homogeneous pore size distribution, the structure enables selective adsorption to ensue during which the butane is safely contained and does not get contaminated. Molecular sieves are preferred more than other adsorbents. For instance, activated carbon solutions that have low selectivity for adsorbing substances like water. Activated carbon is sometimes used for odor control or hydrocarbon removal, but due to its lower thermal stability and adsorption capacity, it is not used for achieving ultra high purity.
The integration of cryogenic distillation with molecular sieve technology ensures that only high quality butane is produced. High quality check and balance, for instance through gas chromatography analysis, ensures that the final product produced is up to industrial and regulatory standards, as it is packaged ready for distribution.
The refining of crude butane into a high purity product requires a series of steps each of which is designed to remove a particular type of impurity or to modify a chemical characteristic of the butane. Starting from washing to more complex processes such as isomerisation, catalytic cracking and cryogenic distillation, refiners make sure that butane is fit for use in today’s world. One of the most important steps in this process is drying, and molecular sieves are still the best solution for this problem because of their effectiveness, wear-resistance, and reasonable price. This capability to continuously eliminate trace contaminants such as water and carbon dioxide cements its role in the petrochemical and energy industries in producing dependable, high purity butane.
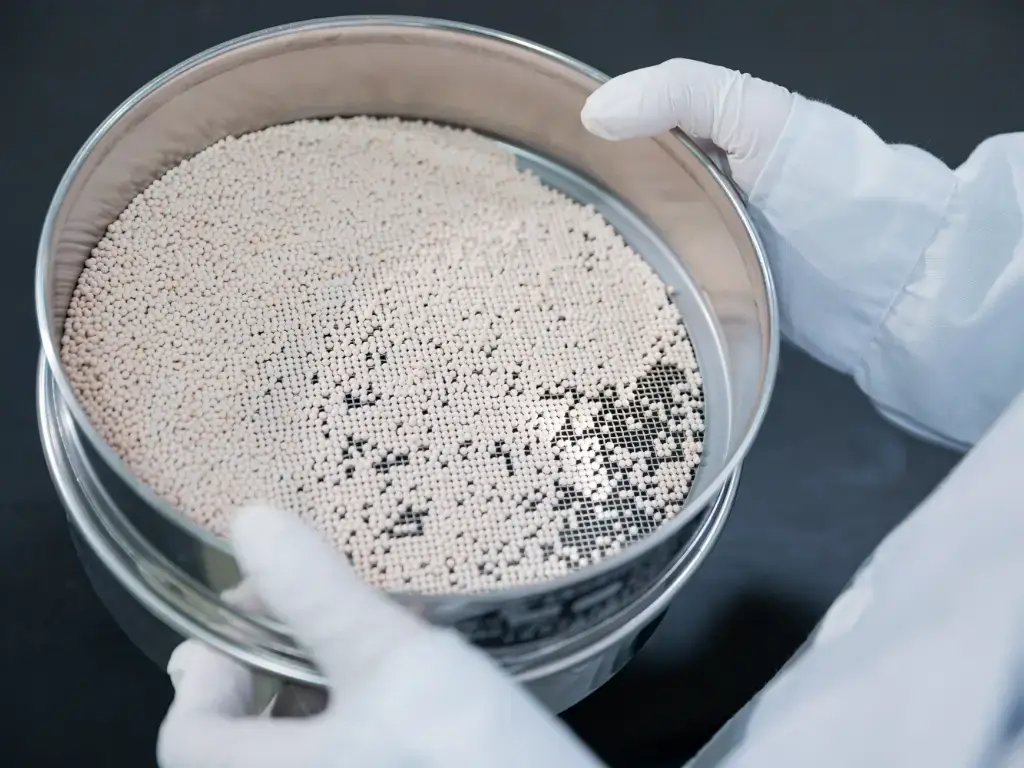
Why Choose Jalon for Your Molecular Sieves Needs?
Jalon is one of the leading molecular sieve manufacturers in China and globally, with more than 20 years of experience. Our mission is to deliver high quality molecular sieves to meet the exact requirement of our customers. We have 112 registered patents and our products are exported to 86 countries and regions, and our customers come from 20 industries. The ISO 9001 and ISO 14001 seals reflect our strict adherence to quality and environmental standards. Our products undergo rigorous testing and we retain samples for 3 years to guarantee that our products are fully traceable and perform optimally. Selecting Jalon is selecting a trusted supplier to fulfill your specific molecular sieve needs and ensure your success.
Understanding the Importance of Butane: Major Applications Across Industries
Butane is used in many industries because of its versatility and efficiency in its use in industries. It is a major constituent of LPG which is used for heating, cooking and as a cleaner fuel for automobiles. It is a friendly energy source since its combustion produces fewer toxic emissions than other fossil fuels.
In the industrial field, butane is used as a feedstock in the production of butadiene which is used in the production of synthetic rubber. It is also used to manufacture propylene glycol that is used in food, drugs and other products such as cosmetics. Also, butane and isobutane are widely used in contemporary refrigeration systems as environmentally friendly substitutes for conventional refrigerants.
Butane also finds its application in consumer products where it is used as a propellant in aerosol sprays used in personal care and cleaning products. It is easily compressible and can turn from liquid to gas under pressure which makes it very versatile and essential in many uses in our daily lives and industries.
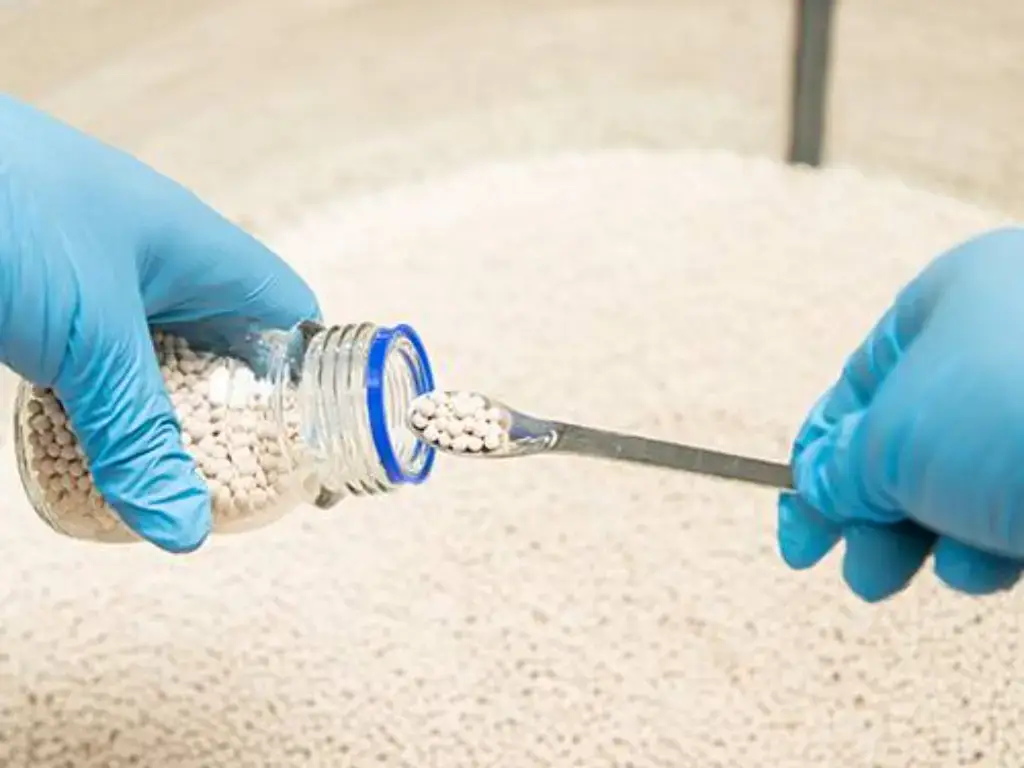
Environmental and Safety Considerations in Butane Production
In environmental context, extraction and refining of butane falls under the energy sector and thus contributes to emissions. As butane is mainly extracted from natural gas and crude oil, its manufacture depends on natural and scarce resources, and thus it is critical to strive to limit emissions and resource consumption toward reasonable levels.
In a bid to overcome these challenges, today’s refineries and processors integrate sophisticated technologies in their refineries and follow very rigorous safety measures. Measures include enhanced absorption apparatus that effectively collects waste gases and enhanced equipment that strongly discourage leakage and blast. Also, storage and transport measures have been improved to make sure that butane is well handled and not abused in transport or local supply.
Knowing the knowledge of butane production is a good example of how progress in the industry is closely connected with the preservation of the environment. New research and sustainable efforts will help to reduce the harm that the industry provides while preserving the need for butane in energy and production.