The question of industrial preparation of oxygen is an important one since oxygen is used in many industries including health, manufacturing, welding and in the generation of electricity amongst other uses. Industrial oxygen generation process is based on extraction and purification of oxygen from the air to then satisfy certain requirements. What is more, what is being done at this stage is not only the separation of oxygen but also ensuring its quality, purity, and efficiency.
In this guide, we will explore the main techniques of industrial oxygen generation, the difficulties that arise during production, and the technologies that will define the future. At the end of this article, you will be in a position to understand all the stages of oxygen production.
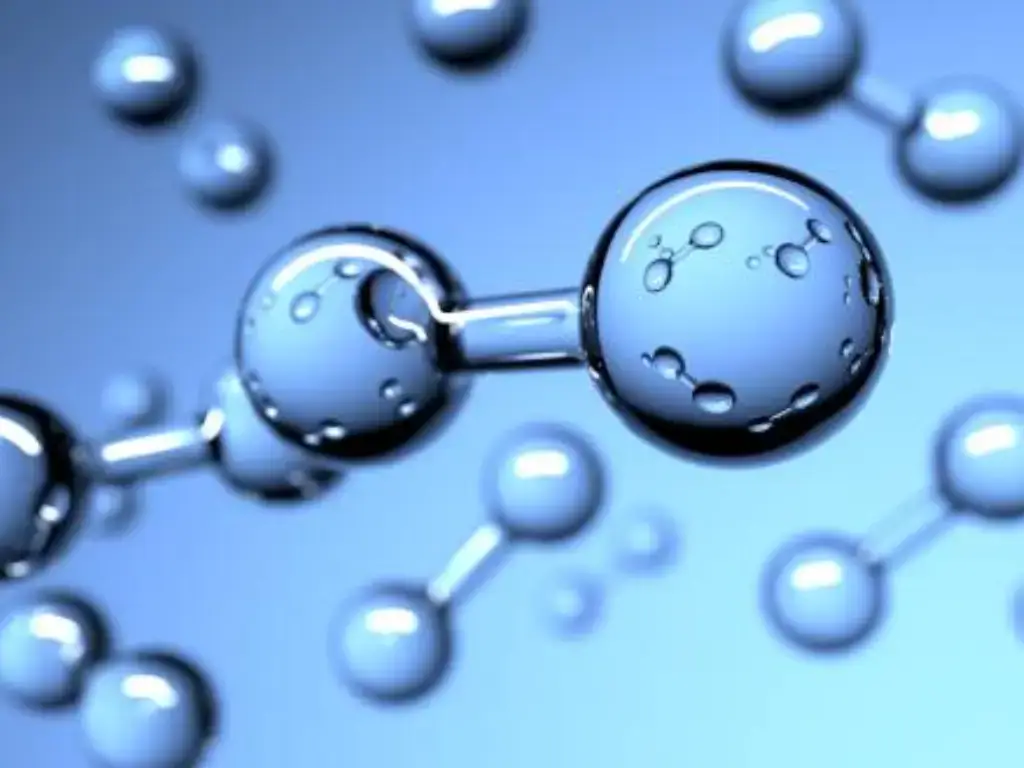
What is Industrial Oxygen Production?
Industrial oxygen production means the process of obtaining and purifying oxygen for the needs of various industries from the air. Although oxygen is present in the earth’s atmospheric air in the form of approximately 21%, it cannot be used in most industrial processes as such. This typically entails using a method to separate oxygen out of other elements constituting air where the major constituent is nitrogen, argon and other residual gases and to obtain purity and the right volume of oxygen.
The objective of industrial oxygen production is therefore to provide oxygen in required quantities and with suitable levels of purity for use in related sectors considered here as medical, metallurgical, chemicals and energy. For instance, medical oxygen used in the hospital has to be of a higher purity than 99.5%, while industrial oxygen for welding or combustion processes does not require such a high level of purity.
To this end, several complex systems and apparatus are employed in oxygen production plants. The most common setups include:
Air Separation Unit (ASU): This is the core part of many large oxygen production plants. ASUs employ technologies such as cryogenic distillation to cool air and then to isolate individual gases. In the ASU, cold boxes also find application to sustain extremely low temperature profile required for liquefaction of air.
Compressors: It is used to compress atmospheric air prior to its separation into the constituent elements of a particular gas. These machines are also useful in making the air achieve the set pressure levels for downstream functions such as adsorption or cryogenic distillation.
Adsorption Towers (for PSA systems): In pressure swing adsorption (PSA) systems, the adsorption towers must be packed with materials such as zeolites, through which the nitrogen molecules are selectively adsorbed, while the oxygen remains liberated.
Membrane Systems: For applications where smaller volumes or lower purity oxygen is required, membrane separation systems are employed. These systems use membranes that are selective to oxygen and hence allow oxygen to pass through in preference to other gases.
Cryogenic Storage Tanks: Liquid oxygen in particular is stored in cryogenic tanks after it has been generated. These tanks have very low temperatures that keep oxygen in its liquid state until it is required for use or it is pumped through the conversion process to gas.
The above equipment operates in conjunction to guarantee that oxygen production is as efficient as is relevant to the industry. The decision of this matter and the choice of equipment as well as the method depends on the application for which it is intended, on the scale of production, as well as on the degree of purity required.
Therefore, the industrial production of oxygen is a complex project that is integral to the current economy. Thus, industries can obtain the required amount of oxygen, its purity and achieve the necessary level of production efficiency with the help of most modern technologies and equipment.
The Main Methods of Industrial Oxygen Production
Oxygen production on an industrial scale relies on three primary methods: cryogenic method of oxygen production, pressure swing adsorption (PSA) and membrane separation. All of them have peculiarities and are used in the corresponding mode depending on the scale, purity, and cost of the needed material.
ethod | Key Features | Purity Range | Advantages | Applications |
Cryogenic Oxygen Production | Uses cryogenic distillation to separate air | >99% | High purity, large-scale capacity | Medical, steelmaking, chemical production |
PSA (Pressure Swing Adsorption) | Uses molecular sieves to adsorb nitrogen | 90-95% | Energy-efficient, ideal for small to medium-scale production | Medical, industrial welding |
VPSA (Vacuum Pressure Swing Adsorption) | Uses vacuum desorption to improve efficiency | 90-95% | Lower energy consumption, suitable for medium to large-scale production | Steelmaking, wastewater treatment, combustion support |
Membrane Separation | Uses specialized membranes to separate oxygen and nitrogen | <90% | Compact, energy-saving, easy maintenance | Small-scale applications, such as gas welding, chemical production |
Cryogenic Oxygen Production: Using the Process of Air Liquefaction and Distillation to Separate Oxygen
Cryogenic oxygen production is the most common method of oxygen production for large scale oxygen production due to its high purity. This process uses cryogenic distillation which is a process of cooling the air to below its liquefaction point. At these temperatures, air turns into a liquid state and the various components of air can be separated on the basis of their boiling points. For instance, oxygen boils at -183 degrees Celsius while nitrogen boils at -196 degrees Celsius.
Before liquefaction, however, the air has to be purified to remove water vapor and other contaminants such as CO₂. This step is important because at cryogenic conditions, even a small amount of water or CO₂ condenses to form ice or solid CO₂ which plugs the equipment and hampers the separation process. At this stage, the molecular sieves like 4A and 13X are very essential. They are capable of adsorbing water and CO₂ with high selectivity and the concentrations of these components are brought down to below 1 ppm. Molecular sieves are also unique in their capacity to remove both moisture and CO₂ at the same time, and their performance during multiple regeneration cycles. Other desiccants such as silica gel and activated alumina may be used prior to the molecular sieves to handle large amounts of moisture, but they cannot match the fine and deep drying provided by the molecular sieves, especially for cryogenic applications.
After the air has been dried and purified it is cooled to its liquefaction temperature and then pumped into a cold box. Here, distillation columns separate oxygen from nitrogen, argon and other minor components. The end product is very high purity liquid oxygen which can be used as such or vaporized for use in medical oxygen, welding and steel making industries. This method is more suitable for applications that need oxygen with a purity of more than 99% and large scale oxygen generation, which makes it a fundamental technology for industries with high oxygen demand.
However, cryogenic oxygen production is not without its problems. Cryogenic temperatures are difficult to achieve and sustain, and the cooling systems needed for this purpose are highly energy-intensive and expensive. But for industries that require a large and constant supply of oxygen, like steel industries, gas welding or health care industries, this method is still very useful because of its reliability and ability to produce large quantities of oxygen.
Pressure Swing Adsorption (PSA)
Pressure swing adsorption (PSA) is one of the most efficient and economical ways of producing oxygen. It employs the use of materials such as zeolites to selectively adsorb nitrogen while at the same time passing oxygen. Working at comparatively low pressures, PSA systems are suitable for on-site oxygen production, especially in such sectors as healthcare, where the availability of oxygen is essential.
In PSA systems, compressed air initially flows throughadsorbent material that captures nitrogen and other contaminants such as CO₂ and moisture. If not treated, these impurities can greatly decrease the efficiency and the life span of the system. Molecular sieves like 5A and 13X are used in this process because they are the main adsorbents that are used for both nitrogen separation and deep drying. Molecular sieves help to maintain the performance of the system and constant oxygen production by decreasing the content of moisture and CO₂ to less than 1 ppm. Some of the pre-treatment steps involve drying agents such as activated alumina and silica gel, which deal with bulk moisture and guard the molecular sieves. However, molecular sieves are absolutely essential for attaining the level of accuracy and penetration necessary for PSA operations.
When the pressure in the system is released, the nitrogen is desorbed and the adsorbent material is ready for the next cycle of operation. PSA cannot achieve the same level of purity as cryogenic distillation, but it can produce oxygen with a purity of 90-95%, which is adequate for uses such as gas welding or medical purposes.
PSA is also scalable, which is one of the significant benefits. They can be designed for small or medium scale production and thus affordable to industries that do not require the large quantities produced by cryogenic plants. However, the adsorbent material requires frequent regeneration to maintain high efficiency and effectiveness in the long run.
Vacuum Pressure Swing Adsorption (VPSA)
VPSA is a modification of PSA which improves efficiency as a vacuum is used to strip nitrogen during the desorption process. This reduces energy consumption and increases overall system performance, making VPSA a cost-effective choice for medium-purity oxygen production at higher flow rates. Commonly used in steel production, water treatment and in combustion systems.
In order to achieve a stable operation of the VPSA systems, it is necessary to use air that is free of moisture and CO₂, as these components can harm the adsorbents or decrease the performance of the system. 5A, 13X and advanced LiX types of molecular sieves are important in this process.Especially LiX molecular sieves, have higher nitrogen adsorption capacity, better water and CO₂ removal performance, and better stability under high pressure and multiple regeneration conditions.
Pre-treatment normally consists of activated alumina and silica gel for dealing with gross moisture removal and to minimize the work of molecular sieves. Nevertheless, molecular sieves are vital for achieving extremely low dew points and preserving the performance of VPSA systems in the long run. While VPSA has lower energy cost per volume of oxygen generated compared to PSA, it has higher capital costs because of vacuum systems. In this respect, VPSA is most suitable for industries that require both high efficiency and large capacity.
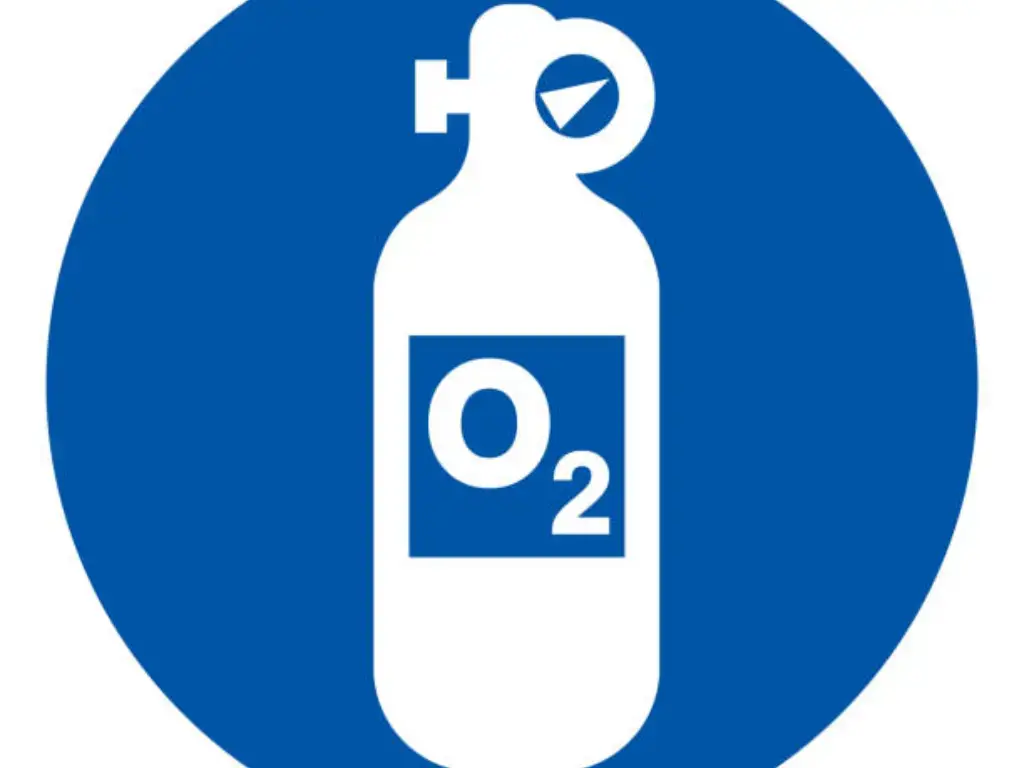
Membrane Separation: Extracting Oxygen Through the Permeability of Specific Membranes
Membrane separation is relatively a new technology in oxygen production. It employs selective polymer membranes that enable the passage of oxygen molecules rather than nitrogen molecules to produce a concentrated stream of oxygen. This method is small in size, power consumption is low, and suitable for applications that do not require high levels of oxygen purity.
Membrane systems are particularly advantageous for remote or mobile installations due to their simplicity and low maintenance. For instance, the gas welding industry or chemical production industries use this method due to its flexibility. However, due to its inability to attain the same level of oxygen purity as PSA or cryogenic processes, the use of this technique is somewhat restricted to moderate oxygen purity demands.
Before the air enters the membranes, it has to be dehumidified in order to achieve the best results. Water and CO₂ can decrease the efficiency of the membrane and decrease the lifespan of the system. Activated alumina is used as the primary drying agent in these systems to remove bulk moisture to a level sufficient for most processes. For more demanding applications where deeper drying or removal of CO₂ is needed, molecular sieves are used because of their higher adsorption capacity. 4A or 13X type of molecular sieves can remove moisture and CO₂ to ultra-high levels. Thus, the membranes are well protected and the system can perform stably under high working conditions. Silica gel is applied less frequently, but it is sometimes used in the first step to eliminate most of the moisture and to lessen the work of activated alumina and molecular sieves.
While membrane separation cannot achieve the same level of purity as PSA or cryogenic techniques, the low energy consumption, compactness, and simplicity of the method make it suitable for use where moderate levels of oxygen purity are sufficient.
Conclusion
Industrial oxygen production relies on various methods tailored to specific needs: Cryogenic distillation for high purity oxygen, Pressure Swing Adsorption (PSA) and Vacuum Pressure Swing Adsorption (VPSA) for medium purity and Membrane separation for compact moderate purity solutions. In all these methods, air drying is essential, so molecular sieves are of great importance. This is because they have a higher capacity to adsorb moisture and CO₂ hence enhancing system reliability and efficiency. Due to their accuracy, sturdiness, and versatility, molecular sieves are still a vital part of the contemporary oxygen production and help various industries to achieve reliable outcomes.
How Jalon Molecular Sieves Support Efficient and Reliable Oxygen Production
Jalon has been in the molecular sieve manufacturing business for more than 20 years, has 112 registered patents, and exports its products to 86 countries. We are ISO 9001 and ISO 14001 certified, guaranteeing our customers quality, reliability, and sustainability of our products to their needs.
Besides conventional molecular sieves, Jalon has developed enhanced products for the enhancement of industrial oxygen generation. The new generation of our molecular sieves, JLOX-500 and JLOX-103, increase the nitrogen adsorption and selectivity of nitrogen over oxygen. This guarantees higher output of oxygen efficiency, which is ideal for industrial PSA and VPSA oxygen production systems.
Backed by a modern R&D laboratory with an investment of RMB 14.5 million, Jalon guarantees constant enhancement of product performance. Whether it is for medical use, or for industrial gas separation, Jalon molecular sieves offer reliable and effective solutions to the demands of modern oxygen production.
Potential Issues and Solutions in Industrial Oxygen Production
There are several issues that are associated with industrial oxygen production and these are as follows; These challenges can be categorized into four main areas: energy consumption, purity, operation, and storage and transportation.
Energy Consumption
Cryogenic distillation which is commonly used needs a lot of energy to cool the air to below -183°C for liquefaction. In response to this, manufacturers are seeking ways of using energy efficient cooling techniques and incorporating renewable energy into production processes.
Purity Maintenance
Carbon dioxide, water or argon can contaminate oxygen and this is not good for applications that require high levels of oxygen purity such as in health facilities. High efficiency drying systems like molecular sieves and continuous monitoring and filtration guarantee that the oxygen supplied is of the right quality.
Operational Continuity
PSA systems require the adsorbent to be regenerated periodically, which results in stoppages in production. Duplicated systems and advanced adsorbent materials, including high-capacity molecular sieves, reduce the time of equipment failure and increase productivity.
Storage and Transportation
Oxygen storage and transportation also demand specific vessels like high pressure cylinders or cryogenic tanks that need frequent inspection. Advancements in lightweight and robust storage media and on-site oxygen generation eliminate the issues of supply chain management.
With the help of these challenges, industrial oxygen production is still able to meet the needs of different industries with the help of modern technologies and effective practices.
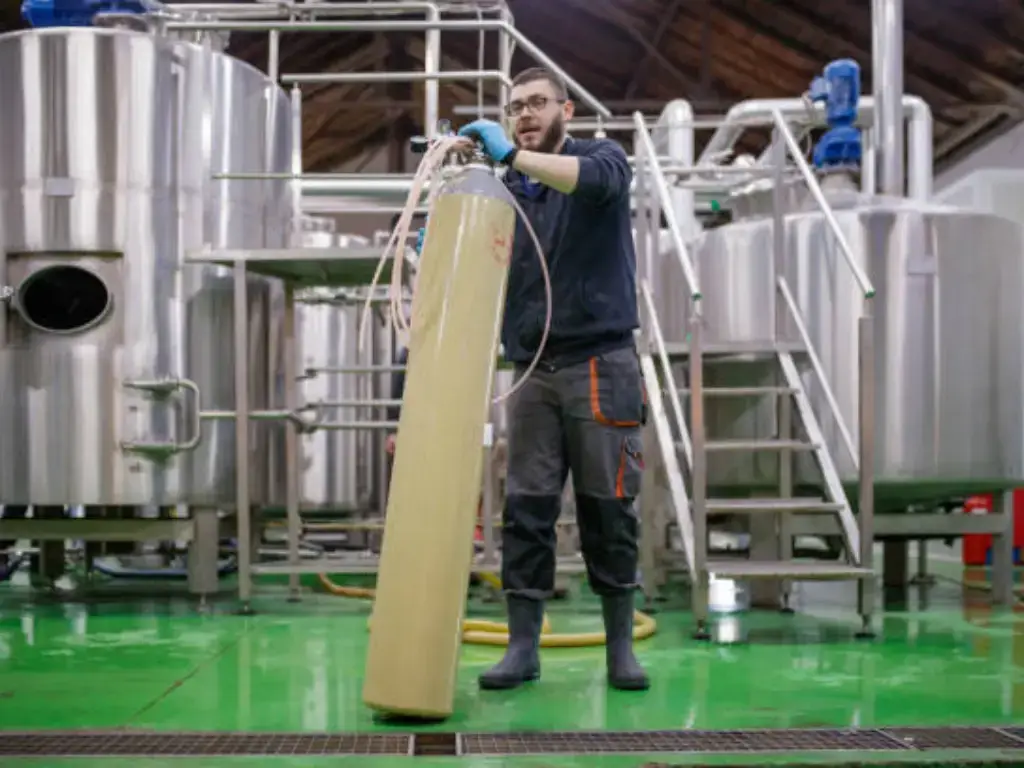
Emerging Technologies and Innovations in Industrial Oxygen Production
The future of industrial oxygen production is innovation, where efforts are made to make the processes more efficient, sustainable and cheaper. New developments in cryogenic distillation are aimed at energy use, which is one of the biggest expense factors. New cooling technologies are being developed to lower the power required to achieve sub-zero temperatures below -183°C to improve the efficiency of large-scale oxygen production.
In PSA technology, new and better adsorbent materials such as molecular sieves are being designed to enhance nitrogen adsorption and oxygen selectivity. These materials raise oxygen output, prolong the service life of the systems, and lower the maintenance expenses. There are also attempts to use a combination of PSA and cryogenic techniques to obtain high purity and relatively low costs of operation.
New AI-based monitoring solutions are already changing the oxygen production industry by providing real-time data analysis and predictive maintenance. Such systems reduce waste, guarantee the required level of performance, and contribute to environmental objectives.
Finally, the development of membrane separation technology is broadening the opportunities for oxygen generation. These systems are small and energy efficient, making them suitable for industries that require small systems at reasonable prices.
From improving on the current technologies to developing new methods of producing industrial oxygen, the world is being supplied with the gas in a more efficient and sustainable manner.