Introduction: Importance of Nitrogen in Industry
Such is the power of nitrogen, a fundamental resource in various industries for its inertness. The manufacturing sector is heavily reliant on it and this cuts across various fields such as agriculture, pharmaceuticals among others. Industries that know how to remove nitrogen from air efficiently are able to generate pure nitrogen gas. Ammonia production, chemical processes, food packaging and pharmaceuticals are some of the applications where this pure nitrogen is required.
Most controlled environments utilized in different manufacturing settings could not be realized without pure nitrogen brought out from atmospheric air. Isolating nitrogen does not only involve isolating it from other gases but also includes dividing oxygen, carbon dioxide and water vapor amongst others. This separation ensures that the highest standards of quality and safety can be met across all industrial uses. In recent past, ways of removing nitrogen from air have improved significantly due to increased industrial demands. This article seeks to unpack critical methods used when extracting nitrogen in order to enable you make informed decisions based on your specific requirements.
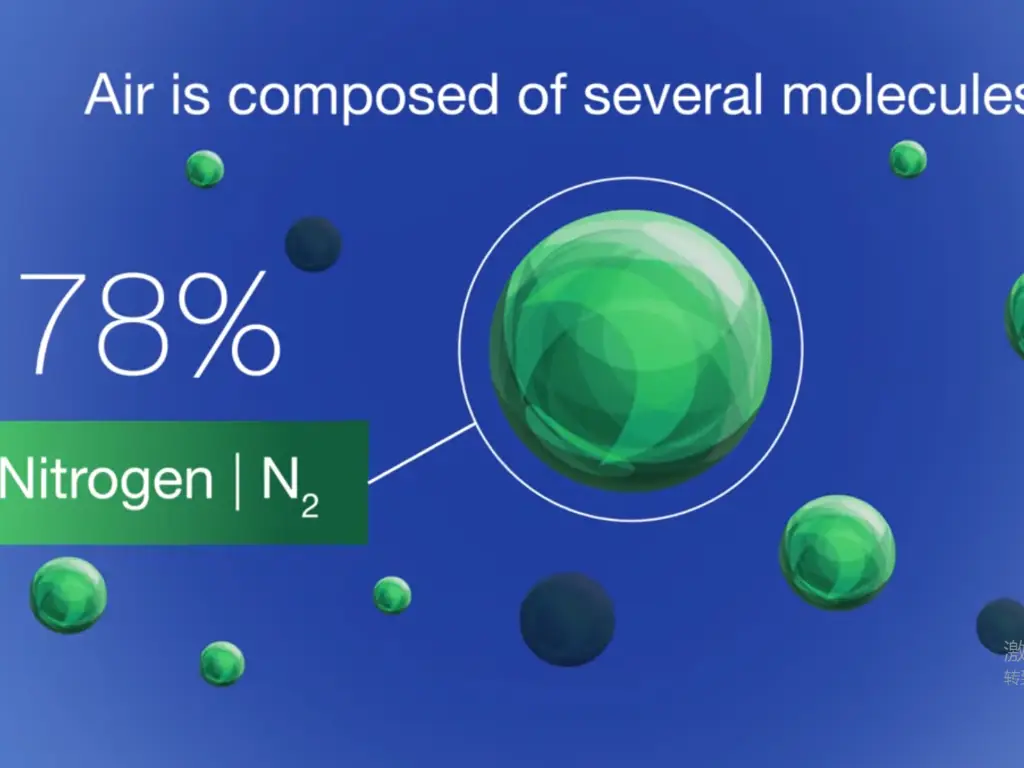
Overview of Nitrogen Extraction Methods
It has been a long time since fractional distillation and other traditional nitrogen extraction methods have been the most commonly used and highly effective ones for producing high-purity nitrogen. Fractionation is complicated having several steps: firstly, atmospheric air is cooled down until it liquefies. In a distillation column, this liquid air is then gently heated after which gases separate on the basis of their boiling points. Nitrogen, which boils at -195.8°C, evaporates faster than oxygen that boils at -183°C. Such detailed temperature regulation allows for efficient isolation of nitrogen.
Fractional distillation possesses noticeable disadvantages notwithstanding its high effectiveness. This process heavily depends on electricity since it requires a lot of electrical power to sustain extremely low temperatures needed for liquefaction of air resulting in high operational costs. On top it all, setting up and maintaining fractional distillation plants is complex and expensive thus they are less affordable to small operations.
Energy efficiency and cost-effectiveness are major advantages gained from recent advancements in technology. At times PSA systems require lower energy consumption because they can be installed onsite thereby saving logistic costs as well as being flexible Membrane systems have simplified even more so that they need very little maintenance while scaling them up is easy With these techniques therefore, although not achieving the ultra-high purity achievable through fractional distillation, many industrial applications benefit making them suitable options for businesses that wish to optimize their nitrogen production operations
Cryogenic Distillation
Process Explanation
This advanced process of fractional distillation is cryogenic distillation, which is often referred to as the gold standard for gas separations. In this procedure, atmospheric air cools down until it gets to -196°C and eventually liquefies. The liquid air is then carefully heated so that it gradually reaches its boiling point which leads to a dramatic change as nitrogen, oxygen, phosphorus among other inert gases like argon continue separating. This entire method however relies much on the difference in boiling points between nitrogen (-195.8°C) and oxygen (-183°C). High purity levels can be achieved by extracting liquid nitrogen first before purifying further to remove impurities.
It should be noted that cryogenic distillation can achieve high pure nitrogen production with 99.999% purity sometimes being accessible making it useful especially in industries where gas purity is sacrosanct. Furthermore, this strategy may also be applied to enhance the effective manufacture of other gases such as oxygen and argon which could serve as valuable products of this technique. Numerous studies have been conducted aimed at improving the efficiency of this process. However, this method consumes more energy than any other alternative but requires complicated machinery and extensive maintenance that raises costs of operations significantly. Again, the initial capital required for setting up a cryogenic distillation plant may be very high making this approach impractical for small-scale businesses in certain instances. Similarly, they corrode and wear out easily hence reducing the lifespan and effectiveness of such devices.
Industrial Applications
Cryogenic distillation is predominantly used in industries requiring ultra-pure nitrogen. It’s the go-to method for producing nitrogen for the semiconductor industry, medical-grade gases, and specialized chemicals. High-purity nitrogen is essential in these fields to prevent contamination and to ensure product quality and safety. In essence, this technique is best suited for large-scale operations that can justify the high capital and operational costs.
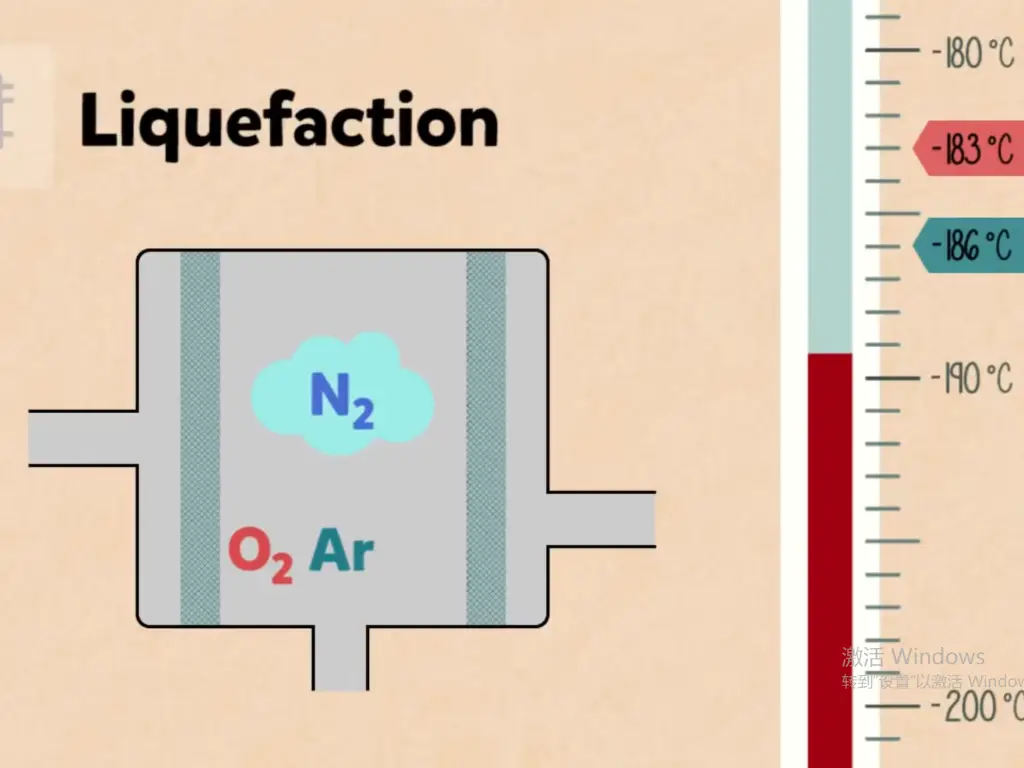
Pressure Swing Adsorption (PSA)
Working Principle
Pressure Swing Adsorption (PSA) is one method that is used to eliminate nitrogen from air, and it involves the use of zeolite molecular sieves or activated carbon. Zeolite molecular sieves are aluminosilicate crystals which have uniform pores. These materials possess selective adsorption capabilities, thus being perfect for isolating nitrogen. Atmospheric air is compressed in the first place before passing through any adsorbent bed, which mostly comprises of zeolite. Nitrogen molecules selectively adsorbed by the molecular sieve due to their smaller kinetic diameter while allowing oxygen and other larger molecules to pass through. When the adsorbent gets saturated with nitrogen, pressure reduction steps cause release of nitrogen that was adsorbed as high purity product gas. PSA systems work in a cyclical manner with several adsorbent beds operating alternately so as to maintain continuous production of nitrogen gas. For consistent nitrogen output and efficient system operation there must be effective cycle management and precise control on pressure swings.
Suitable Applications
The primary benefit of PSA systems is its relatively low energy consumption as compared to cryogenic distillation. Furthermore, they can be installed on-site hence lower logistic charges associated with pure nitrogen transportation. The compactness of the PSA units make them ideal for small areas. In addition, PSA systems offer moderate to high purity nitrogen service that are cost-sensitive for industries that require such gas; among these include applications in food packaging where it is used in displacing oxygen to extend shelf-life and metal processing where it functions as a cover gas.
Industries interested in ultra-pure nitrogen would not consider PSA systems since nitrogen can have only 95% up to 99.9% purity. However, these levels of purity are sufficient for some markets like metal processing and food packaging.
Jalon: A Trusted Provider of Molecular Sieves for PSA Nitrogen Separation
Jalon is a leading manufacturer of first-class molecular sieves, zeolites and activated alumina, which are indispensable for nitrogen separation in PSA. In particular, they manufacture oxygen-enriched molecular sieves that belong to JLOX-500 series and possess superb nitrogen adsorption properties as well as selectivity between nitrogen and oxygen. Thus, these have become vital components for efficient and consistent nitrogen separation within PSA oxygen generator plants.
Membrane Nitrogen Generation
How It Works
Another recent method of nitrogen removal from air is through membrane nitrogen generation. In this process, compressed air passes through a polymer membrane with microscopic openings. Oxygen, carbon dioxide, water vapor and any other gases are not allowed to pass through while nitrogen permeates, resulting in a continuous flow of nitrogen gas. The efficiency of the method can be easily scaled up by paralleling multiple membranes. The purity of nitrogen can be manipulated by changing the pressure and airflow rate across the membrane system.
Advantages and Disadvantages
The most important benefit of membrane nitrogen generators is their simplicity and adaptability. They use less energy; have fewer moving parts; and require less attention as compared to other methods. Moreover, they can also be adjusted very easily to match different requirements for pureness of nitrogen gas hence making them highly adaptable devices. Membrane Nitrogen Generation is best suited when moderate levels of Nitrogen purity are required such as in fire suppression systems within commercial kitchens or tire filling stations used in automobile shops or even some food packaging industries where low maintenance costs are key.
However, membrane systems typically achieve purity levels ranging from 90% – 99%, which may not satisfy certain high-purity applications. Furthermore, time causes deterioration in performance which necessitates periodic replacement of modules that make up these systems.
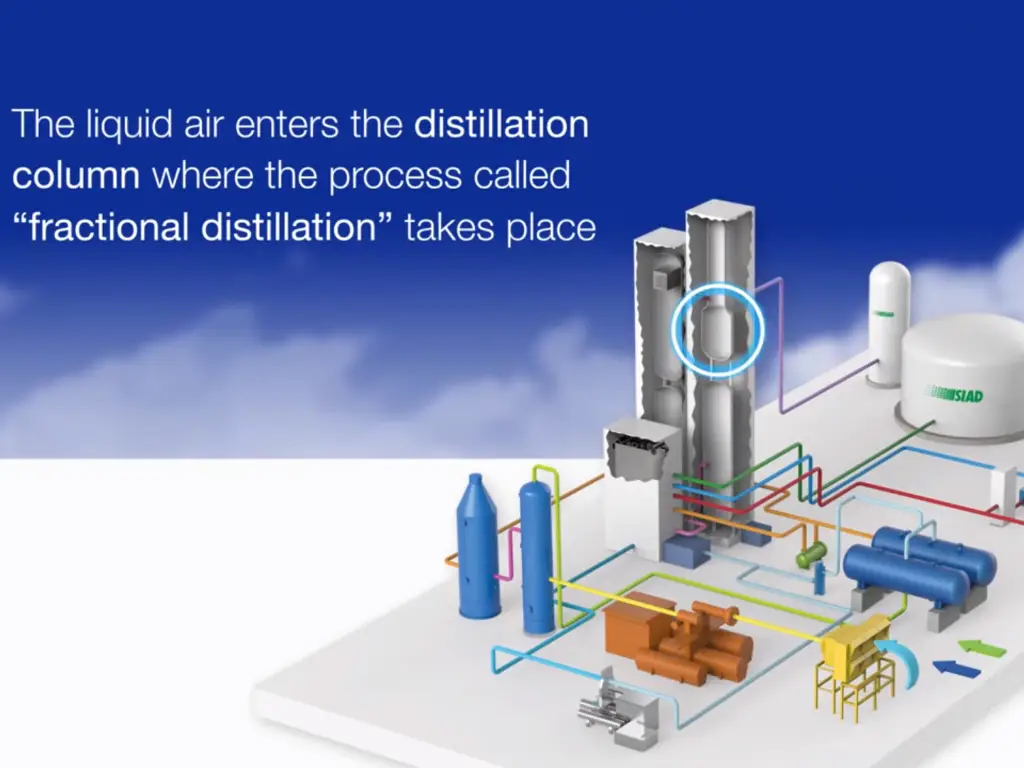
Comparison of Extraction Methods
Purity Levels
The purity levels of nitrogen produced are a crucial factor for the selection of an extraction method. Cryogenic distillation has the highest achievable levels of purity often surpassing 99.999% making it preferable for high accuracy applications like those in semiconductor manufacturing and medical application fields. In contrast, PSA systems achieve lower but significant levels of purity ranging from 95-99.9%, which are useful in many industries. On the other hand, membrane systems give nitrogen purities between 90% and 99%, being most appropriate for such applications where highest possible purity is not mandatory.
Cost Efficiency
Methods vary in terms of their cost effectiveness. Membrane systems are generally the least expensive to operate due to their simplicity and low energy consumption rates. PSA systems strike a balance between cost and purity, making them suitable for many industrial applications. However, cryogenic distillation is always associated with the highest costs since it requires a lot of energy and intricate tools that are very costly.
Maintenance Requirements
There exist major discrepancies among maintenance requirements as well. Membrane systems have less/more moving parts than others therefore they tend to be easier/more complicated to maintain leading to decreased/increased operational complexity respectively, compared with other methods such as adsorption on solid materials used in PSA system (adsorbent replacement). Maintenance for cryogenic distillation calls for more efforts due to its complex nature involving specialized equipment that can withstand extremely low temperatures.
Feature | Cryogenic Distillation | Pressure Swing Adsorption (PSA) | Membrane Nitrogen Generation |
Process | Cools air to -196°C, separates gases based on boiling points | Uses zeolite to selectively adsorb nitrogen | Uses membranes to allow nitrogen to pass through |
Purity | Highest (99.999%+) | Moderate-High (95%-99.9%) | Moderate (90%-99%) |
Cost (Operation) | Highest (High energy consumption) | Moderate | Lowest (Low energy consumption) |
Cost (Setup) | Highest (Complex equipment) | Moderate | Lowest (Simple equipment) |
Maintenance | High (Specialized equipment) | Moderate (Adsorbent replacement) | Low (Few moving parts) |
Applications | Ultra-high purity needs (Semiconductors, Medical) | Moderate-high purity needs (Food packaging, Metal processing) | Moderate purity needs (Fire suppression, Tire filling) |
Scalability | Moderate | High | High |
Energy Efficiency | Low | Moderate | High |
Footprint | Large | Moderate | Small |
Benefits of Using Nitrogen Generators
Employing nitrogen generators can lead to substantial savings. On-site nitrogen production eliminates the need for buying, transporting and storing nitrogen cylinders or liquid nitrogen which may be expensive and difficult in logistics. This is especially relevant for industries having high nitrogen needs, where cost gains can be significant over time.
On-site Nitrogen generators guarantee continuous supply of nitrogen hence no production process interruption due to failure in supply chain. Also, they are space-friendly as they will often take up considerably less space than that required by large storage tanks or cylinder racks allowing businesses to utilize their floor area effectively on other essential activities
The use of nitrogen generators helps reduce environmental impacts connected with the manufacture and transportation of nitrogen. In addition, business that generate their own nitrogen are able to avoid carbon emissions from long distance transport of liquid nitroge or hig pressure gas cyinders. Also, modern-day Nitrogen Generators are designed with energy sufficiency in mind thus reducing their overall impact on environment even more.
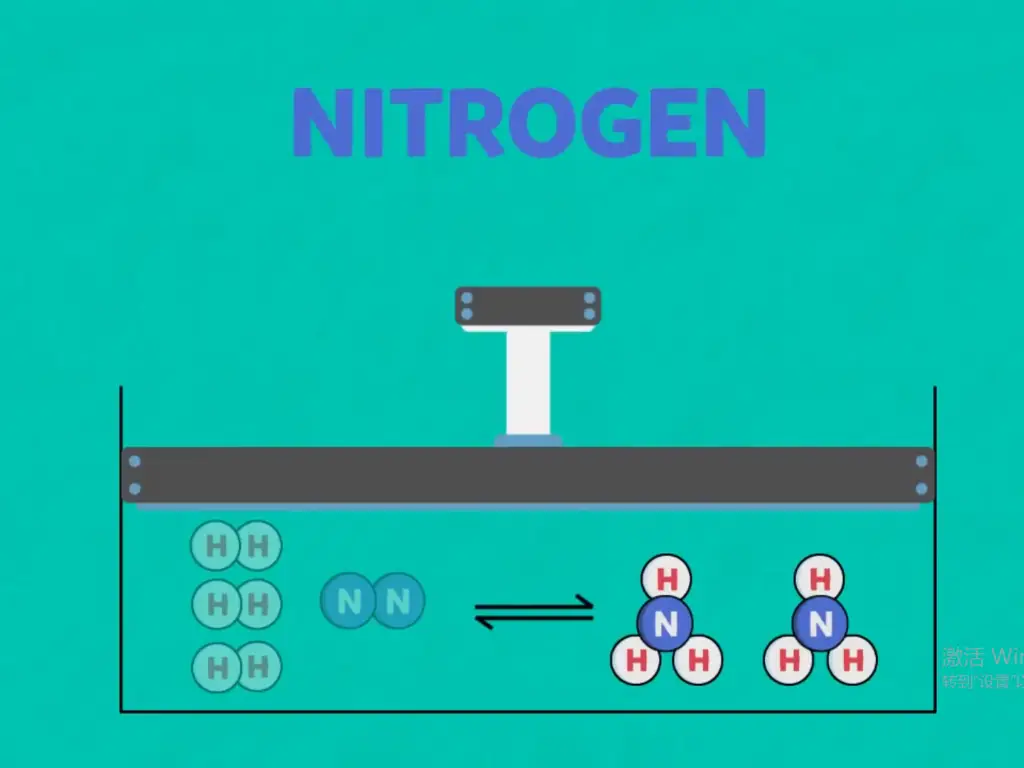
Choosing the Right Nitrogen Generator for Your Business
For your operation, it is necessary to consider some things while choosing a nitrogen generator, such as the specific purity requirements, budget constraints, and production volume. Mostly commonly used PSA systems are appropriate for a variety of industrial applications because they offer a good balance between cost and level of purity in terms of nitrogen fixation. Nevertheless, if one’s operations require ultra-high-purity nitrogen, then cryogenic distillation may be preferable, even though it is more expensive. On the other hand, membrane-based systems would be ideal where purities are not restrictive and maintenance costs must be kept low. Extensive research has shown that while there are simple ways to achieve nitrogen production, a revolutionary new method like cryogenic distillation stands out for high-purity needs despite higher costs.
Conclusion
The extraction of nitrogen from the atmosphere is vital to many industrial processes and depends on specific needs like cost effectiveness, purity levels and maintenance. This knowledge allows companies to choose a nitrogen generator based on their special needs thus ensuring that they have a dependable, pocket friendly, environment friendly supply of nitrogen for their facilities. By adopting this approach, industries will be in a position to optimize their manufacturing processes, improve product quality as well as cut down on operational costs.