中規模から大規模の操業では、窒素、酸素、アルゴンを気体や液体として生産するために、極低温空気分離技術が頻繁に利用される。
超高純度酸素と窒素の製造には、極低温空気分離が推奨される。製造速度の速い設備では、最も経済的な技術です。極低温技術は、液化工業ガスを製造するすべての事業で使用されています。
生成される気体や液体の量、必要な生成物の純度、必要な供給圧力はすべて、その複雑さに影響する。 極低温空気分離 手順、ギアの物理的な大きさ、それを動かすのに必要なエネルギーなどである。
極低温空気分離のプロセスガイド。さあ、始めよう
極低温空気分離・蒸留とは?
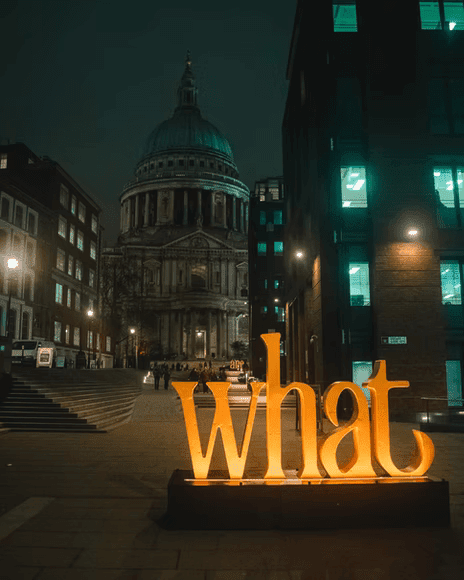
空気から窒素と酸素を分離する技術は、低温蒸留として知られている。状況によってはアルゴンも分離される。極低温」という用語は低温を意味し、「蒸留」は元素の沸点を利用して組み合わせから元素を切り離すことを意味する。その結果、極低温蒸留では、沸点が非常に低い成分が低温で優先的に抽出される。このプロセスにより 高純度物質しかし、エネルギー消費も激しい。
コールドボックスは巨大な断熱容器で、極低温で作動する蒸留柱と熱交換器が収められている。冷凍ループでは、絞り効果としても知られるジュール・トムソン効果が利用される。ガスはスロットリングの間中、断熱ゲートまたは断熱透過性プラグを通過し、圧力が交互に変化するにつれてガスの温度が変化する。
必要な材料
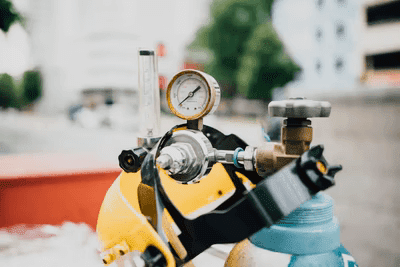
周囲の空気は、最大5%の水分と、空気分離と出力の1つまたは複数の場所で除去されなければならない他の様々なガス(通常、微量レベル)で構成されている可能性があります。 浄化セットアップ.
極低温空気分離のステップとプロセス
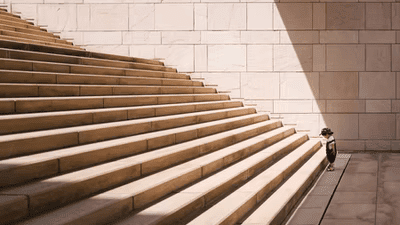
空気の低温蒸留:ステージ
- 吸入空気の前処理、圧縮、冷却。
- 二酸化炭素の除去。
- 給気温度を極低温レベルまで下げるための熱伝導。
- 空気蒸留。
- 冷凍
1.吸入空気の前処理、圧縮、冷却
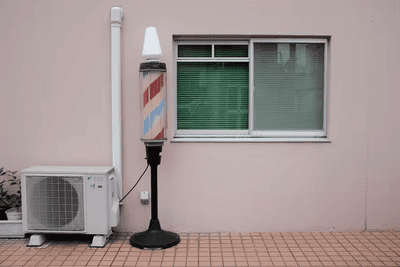
に基づいている。 企画商品ブレンド と許容可能な製品力を得るために、空気はほとんどの状況で5~8バール(約75~115psig)に収縮される。圧縮の最終段階の後、収縮した空気は冷却され、空気流中の蒸気の多くは凝縮され、空気が相間冷却器とアフタークーラーを通過する間に除去されます。
得られる冷却経路の温度(これはほとんど常に、周囲空気の湿球温度または乾球温度によって制限される)は、圧縮構造から出る空気の最終温度を決定するため、圧縮空気の温度は、最大限の効果を得るための理想的な温度をはるかに上回ることが多い。 下流ユニットの性能.その結果、空気を大幅に冷却するために機械式冷凍システムが頻繁に使用される。
2.二酸化炭素とその他の不純物の除去
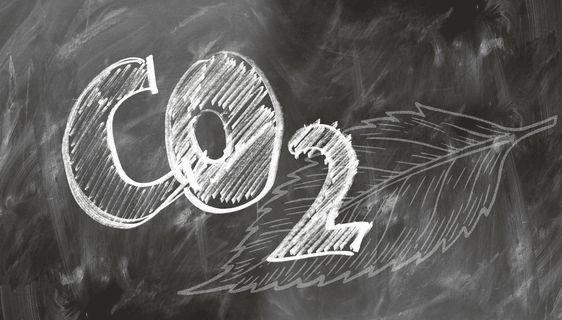
製品の品質基準を達成するためには、流入する空気流の特定の要素を除去しなければならない。水蒸気と二酸化炭素は、極低温で固化し、手順装置の外面に蓄積するため、低温蒸留セクションに入る前の空気から除去する必要がある。
モレキュラーシーブ 蒸気と二酸化炭素を除去する方法としては、ユニットと逆交換器が最もよく使われている。
- モレキュラーシーブのプレ精製ユニットは、ほぼすべての新しい空気遮断設備で使用され、常温に近い温度でモレキュラーシーブ物質の外側にこれらの粒子を吸着させることにより、空気流から二酸化炭素と水を抽出します。工業環境で遭遇する可能性のある炭化水素のような他の汚染物質は、その組成を調整することによって容易に除去することができる。 吸着物質 これらのシステムでは吸着物質は通常2つの同じ容器に保管され、一方は流入空気の浄化に使用され、もう一方は清浄な廃ガスで再生される。一定期間ごとに、2枚のシートが入れ替わる。高い窒素抽出率を求める場合、モレキュラーシーブの前精製が最適です。
- もうひとつの選択肢は、"逆 "熱交換器を使って水とCO2を除去することだ。逆熱交換器は「古い」技術だと思われがちだが、製造率が低い窒素や酸素プラントでは、コスト効率が高くなる可能性がある。逆転熱交換器を使用するプラントでは、圧縮空気供給は2組のろう付けアルミニウム熱交換器で冷却される。
到着した空気は、熱交換器の表面で水蒸気と二酸化炭素が固化するのに十分な低温まで「ウォームエンド」熱伝達で冷却される。バルブシステムにより、空気通路と排ガス通路が一定の間隔で交互に切り替わる。この切り替えの後、非常に乾燥し、温度差のある廃ガスが水を蒸発させ、空冷の間に形成された二酸化炭素の霜を昇華させる。これらのガスは大気中に放出され、熱交換器は、これらのガスが完全に除去された後、再度の通過デューティの反転に備える。
冷吸収システムは、逆熱交換器を利用して蒸留ユニットに流入する炭化水素を除去する場合に使用される。(プレ精製ユニットでは、分子ふるい「フロントエンド」を利用することで、炭化水素汚染物質が水蒸気と二酸化炭素とともに除去される)。
3.給気温度を極低温レベルまで下げる熱伝導
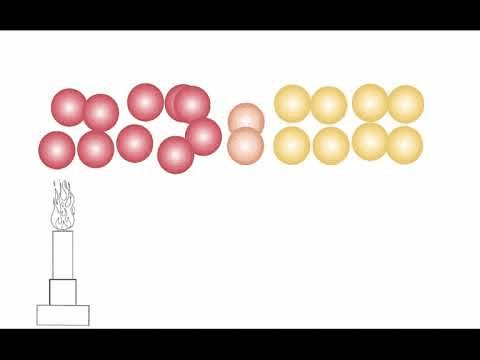
熱は、低温蒸留手順から排出される低温の出力ガスと廃ガス流と、流入する給気との間で、ろう付けされたアルミニウム製熱交換器で交換される。排出ガス流路は、周囲空気に近い温度まで再加熱される。ガス状製品流路と廃棄物流路から冷凍を回収することで、設備で生成する必要のある冷凍の量を削減します。
1つ以上の高圧ステップの流れを組み込んだ冷凍技術は、極低温蒸留に必要な極低温を作り出す。
4.空気蒸留
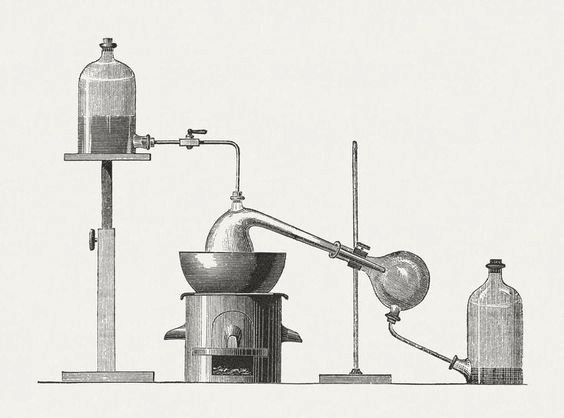
蒸留装置で副生成物として酸素を発生させるために、2本の蒸留柱が連続して使用される。高」及び「低」張力柱(あるいは、「低」及び「上」張力柱)は、最も一般的に使用される用語である。窒素設備には、純度に応じて1本または2本の柱がある。各蒸留柱は、上部から窒素を、下部から酸素を排出する。最初の(圧力の高い)柱で生成された汚染された酸素が所望の製品である場合、2番目の圧力の低い柱でさらに精製される。超高純度の窒素を求める場合は、上段または低圧のピラーを利用し、第一段階の蒸留で除去しきれなかった酸素をほぼすべて除去する。
アルゴンの沸点は酸素に匹敵するため、副生成物として酸素と窒素が必要な場合、アルゴンは酸素と一緒に出力されることが望ましい。従来の2本柱システムでは、酸素の純度は約97%に制限される。低純度の酸素が許容される場合(例えば、燃焼強化のため)、酸素の純度は95%のように下げることができる。ただし、高純度酸素が必要な場合は、蒸留装置からアルゴンを除去する必要がある。
アルゴンが必要な場合は、アルゴン濃度が最大となる低圧流の位置で除去される。取り出されたアルゴンは、低圧ピラーに組み込まれた「サイドドロー」粗アルゴン蒸留塔で処理される。汚染されたアルゴン流はベントされるか、オンサイトで処理されて酸素と窒素の両方が除去され、「純粋な」アルゴンが生成されるか、あるいは液体として貯蔵され、遠方の「アルゴン蒸留所」に送られる。選択肢は、アクセス可能なアルゴンの量と、異なる選択肢のコスト・ベネフィット分析によってほぼ決定される。基本的なガイドラインとして、毎日少なくとも100トンの酸素が発生する場合、アルゴン精製が最も費用対効果が高い。
粗アルゴンから純アルゴンを製造するには、多段階の技術が用いられる。従来の方法では、「脱酸素」成分を使用して、粗アルゴン中に存在する2 - 3 %酸素を除去する。これは、触媒を含む容器内で酸素と水素を化学的に結合させ、分子ふるい乾燥機で(冷却後に)水分を除去するという、少量の多段階手順である。次に、酸素を含まないアルゴン流を蒸留し、「純アルゴン」蒸留装置で残留窒素と不溶性水素を除去する。
パックドカラム蒸留技術の進歩により、アルゴン製造の第二の選択肢が出現した。それは、アルゴン/酸素の困難なアンカップリングを達成するために、非常に背の高い(しかし直径は小さい)蒸留カラムを使用する完全極低温アルゴン回収である。酸素とアルゴンの沸点は比較的緩やかであるため、アルゴンの蒸留には多段蒸留が必要となる。
蒸留システムで処理される酸素の量、および回収率に影響する他の様々な変数により、設備が出力できるアルゴンの量は制限される。これらの要因には、生成される液体酸素の量と、施設の運転パラメータの一貫性が含まれる。アルゴンの生成量は、空気中に自然に存在する気体の割合のため、酸素供給量(体積比)の4.4パーセントまたは重量比5.5パーセントを超えることはできない。
フロントエンド熱交換器は、空気分離塔から発生する冷たいガス状製品や廃棄物の流れを方向転換するために使用される。この熱交換器は、流入する空気をほぼ常温まで加熱しながら冷却する。前述したように、入力と製品ストリーム間の熱伝達は、施設の正味冷凍負荷を低減し、その結果、この熱交換器が使用される、 エネルギー利用.
5.冷凍
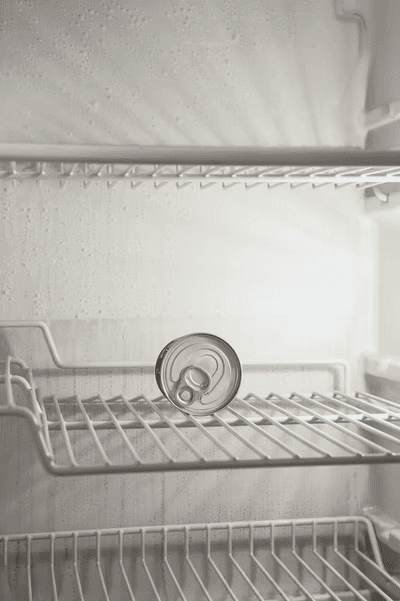
低温装置への熱漏れや、気体流の出入り口での熱交換不良を考慮し、冷凍は極低温で行われる。
極低温空気分離設備で使用される冷凍サイクルは、理論的には家庭用や自動車用の空調システムに適用されているものと同じである。プラントの種類に応じて、1つまたは複数の高圧ストリーム(窒素、廃ガス、供給ガス、出力ガス)が圧力を下げられ、ストリームが冷却される。圧力降下(または膨張)はエキスパンダ内で行われ、冷却と工業用エネルギーの効果を高める。
ガス流の温度は、単にバルブで膨張させるよりも、膨張中にエネルギーが除去される方がより低下します。エキスパンダーのエネルギーは、手順コンデンサー、発電機、あるいはオイルポンプや送風機のようなエネルギーを消費する別の装置に電力を供給するために使用することができる。
極低温酸素工場/空気分離システムからの気体出力は通常、大気圧に近い温度でコールドボックス(超低温で機能する蒸留部やその他の機械が入った断熱容器)から出るが、圧力は低下している。そのため 分離精製手順 一般に、吐出圧力が低いほど効率的である。
より低い圧力はより低い分離電力需要を促進するが、出力をより高い圧力で供給する必要がある場合、製品コンプレッサー、またはコールドボックスからより高い分配圧力で窒素または酸素を直接供給するいくつかの代替サイクルのいずれかが必要となる。これらの高圧供給技術は、製品コンプレッサーやその電力を必要としないため、圧縮を伴う分離よりもコスト効率が高くなります。
効果的で安全なヒント
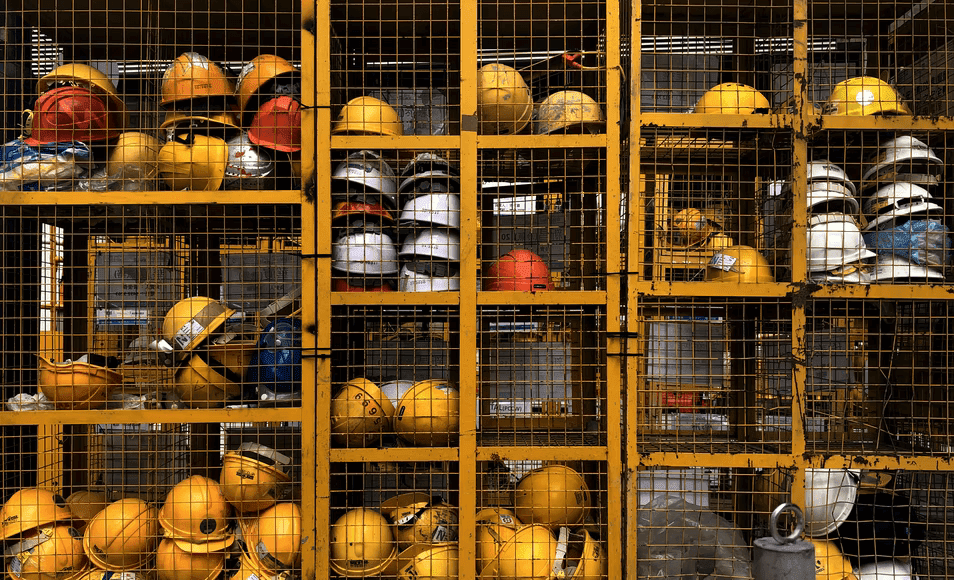
極低温システムやプロセスの建設や設計を開始する前に、正式なハザード分析を実施する。リスクとその対処方法を決定する。もしもの場合」のシナリオを想定する。機械が故障する可能性があること、極低温流体がすぐに気体に変わる可能性があること、バルブが漏れる可能性があること、取り扱いを誤る可能性があること、真空が誤作動する可能性があることを忘れないでください。極低温システムの規模や複雑さに関係なく、このアセスメントは実施されるべきである。
最初から、設備や手順に安全性を盛り込みましょう。設計の最後に安全要素を盛り込むことは、コストと時間がかかるだけでなく、ハザードが見落とされる可能性もある。ハザードを改善するよりも、エンジニアリング設計によってハザードを排除する方が常に望ましいということは、注目に値する。
専門家であっても、何かを見落としたり、ミスを犯す可能性はある。極低温システムの安全性を、他の同僚、外部の専門家、正式な審査機関など、他の人に評価してもらうことは、安全なシステムの可能性を高めるために非常に重要です。
極低温の液体や不活性ガスを扱う場合は、その量がどんなに少なくても、酸素欠乏ハザードの可能性を常に評価すること。アセスメントを通じてそのようなハザードが存在しないことを証明するか、ハザードを除去または軽減するために関連する設計の改善または緩和策を実施する。極低温液体は少量でも大量のガスが発生し、酸素濃度が十分に低い場合、最初の生理学的症状としてすぐに意識がなくなり、昏睡や死に至る可能性があるため、ODHの問題は特に深刻である。
極低温では、その温度で機能することが示されている物質のみを利用する。周囲温度で機能するはずの物質(真空容器の外壁など)が、ハザードアセスメント中に特定の故障メカニズムで極低温に達する可能性があることを念頭に置いてください。
極低温機器と共に、またはその周囲で作業する全員が、何気なく、または時々使用する人であっても、必要な程度の極低温および酸素欠乏危険の安全トレーニングを受けていることを確認する。
常に適切な保護具を着用し、定められた作業工程を守ること。近道をすると、しばしば災難に見舞われる。
結論
極低温空気分離プロセスでは、乾燥剤は必需品です。乾燥剤は 製造工場 高品質の製品を提供できる。 お問い合わせ 喜んでサービスを提供させていただきます。