Introduction to Oil-Water Separation
Today in the world, oil and water separation is an important issue to deal with especially when processes in the industry are involved that greatly affect the environment. Be it cleaning up an oil spill, or treating effluent from the industry, the importance of oil water separation methods is immense. In this how-to article, we will investigate the fundamentals of oil and water separation, illustrate the different techniques available, and present their use in various industries. Therefore, let us go one step at a time and learn how we can address this convoluted problem in the best possible way!
Understanding the Science of Oil-Water Separation
In order to successfully separate oil from water, it is important to know their basic properties first. Oil and water do not mix, and in the field of material science, they are referred to as immiscible liquids. This is as a result of the structural differences in their molecular composition and the intermolecular forces present in them. Water molecules are polar and can bond with each other using hydrogen bonds, whereas molecules of oil are non-polar and tend to bond with themselves using van der Waals forces. These different attributes set will determine the oil water separation process further.
Still another fundamental principle of oil and water separation is the variation in specific gravitys of the oil and water. Water has a greater density than oil, therefore oil sits comfortably on the top of water. This principle is used in various separation methods, for instance, gravity settling tanks. Also, the law of stokes which defines the settling velocity of a particle in a fluid does come into play. In general , the larger the oil droplets and the greater the density difference with water, the quicker the separation.
One of the most common problems related to oil water separation is that it is difficult to separate oil from water emulsions, such as crude oil emulsion. Emulsions are blended fluids that contain droplets of one liquid that are usually too small to be distinguishable when in another liquid. They are classified as either oil-in-water (O/W) or water-in-oil (W/O). An example of an oil-in-water emulsion is milk, which contains fat globules dispersed in aqueous media. To make effective separation easier, it is necessary to break these emulsions and different techniques such as thermal, chemical, mechanical methods, and centrifugation are used for this purpose, especially in the natural gas industry.
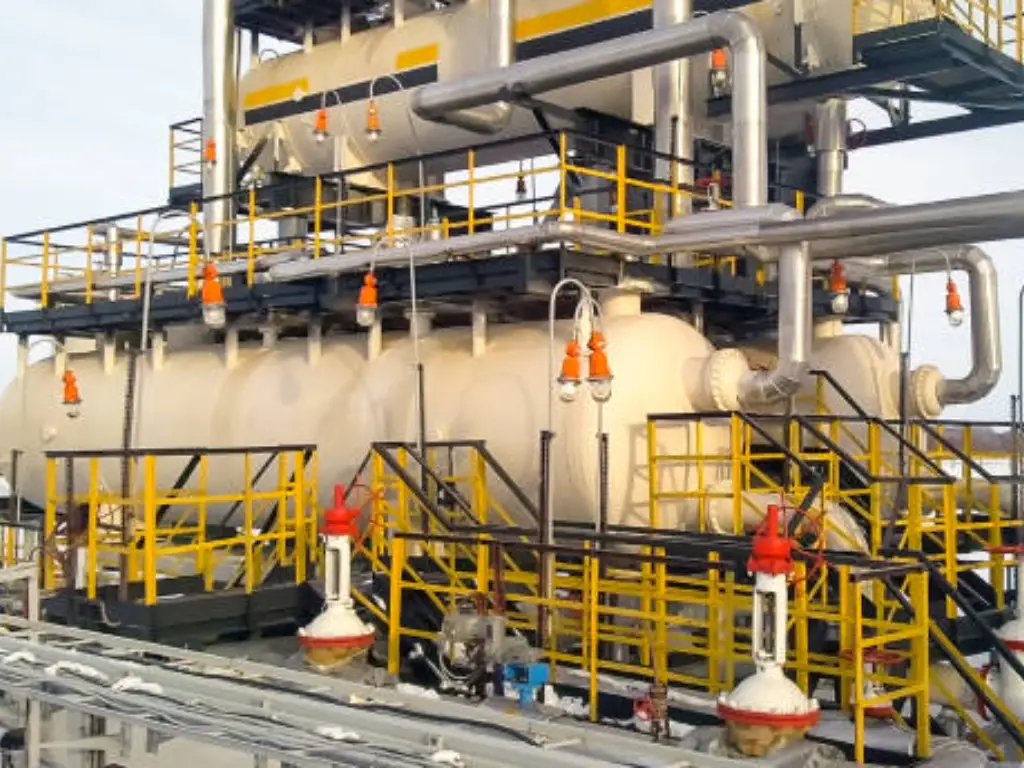
Gravity-Based Oil-Water Separation Techniques
One of the most widely employed techniques for separate oil from water is the gravity-based separation. It is a technique that uses the principle that oil is less dense than water, and as a result, it will rise to the surface and form a layer while the water remains at the bottom. A commonly used gravity type oil water separator is the American Petroleum Institute (API) separator in which there are a number of compartments within a large tank that performs the function of oil water separation in stages. When an emulsion of oil and water passes through such a separator, the oil always comes out on the top surface of the water while the water is at the bottom and is active from the bottom opening. Many are of the view that gravity type separators are quite rudimentary, less expensive, and appropriate for the separation of large amount of oil in water.
Mechanical Approaches of Separation of Oil and Water
Centrifugal Separation: Principles Of Centrifuges And Equipment
Separating oil and water can also be done easily using centrifugal separation. This method employs centrifugal energy to enhance the separation process. The oil and water mixture is fed into the fast turning centrifuge and since water is heavier than oil, it is forced to the edge while oil is kept in the middle. For this purpose, disc stack centrifuge and decanter centrifuge are often used. Centrifugal separation is very efficient, and more so, emulsions with small sized oil droplets can be utilized more than in gravity-based methods.
Oil Filtration Systems for Oil Integration with Water
Filtration is the commonest approach of oil and water separation and primarily considers the presence of smaller oil drops or emulsification. Depending on the specific application type being worked on, coalescence, multimedia and membrane filters are used. Small drops of oil can be made larger through the use of coalescence filters and this makes separation easier. Multi-media filters use sand, anthracite and garnets among other materials to capture oil particles. There are membrane filters which include ultrafiltration and nanofiltration that use semi permeable membranes to remove oil from water.
Coalescing Separators: Aiding in the Separation of Water and Oil
Providing unequaled efficiency to the separation of water and oil, coalescing separators are specialized equipment primarily designed to enhance the merging of oil droplets. The basic function of coalescence plate separation is to provide a large surface area such that particles can collide and merge. With increasing droplet size, they tend to rise to the surface quicker enabling easier separation. Coalescing separators are typically used in conjunction with one or more separation techniques, including gravity settling or centrifugal separation.
Separation Method | Efficiency (%) | Capacity (m³/h) | Droplet Size (μm) | Energy Consumption (kWh/m³) | Maintenance Requirements |
API Gravity Separator | 60-80 | 10-200 | 150-1000 | 0.02-0.05 | Low |
Parallel Plate Interceptor | 70-90 | 50-500 | 60-100 | 0.05-0.1 | Moderate |
Corrugated Plate Interceptor | 75-95 | 50-500 | 30-60 | 0.05-0.1 | Moderate |
Hydrocyclone | 80-95 | 10-200 | 10-50 | 0.2-0.5 | Low |
Centrifugal Separator | 90-99 | 5-100 | 2-20 | 1-3 | High |
Multimedia Filter | 80-95 | 10-100 | 5-20 | 0.1-0.3 | High |
Coalescing Filter | 90-99 | 5-50 | 1-10 | 0.2-0.5 | High |
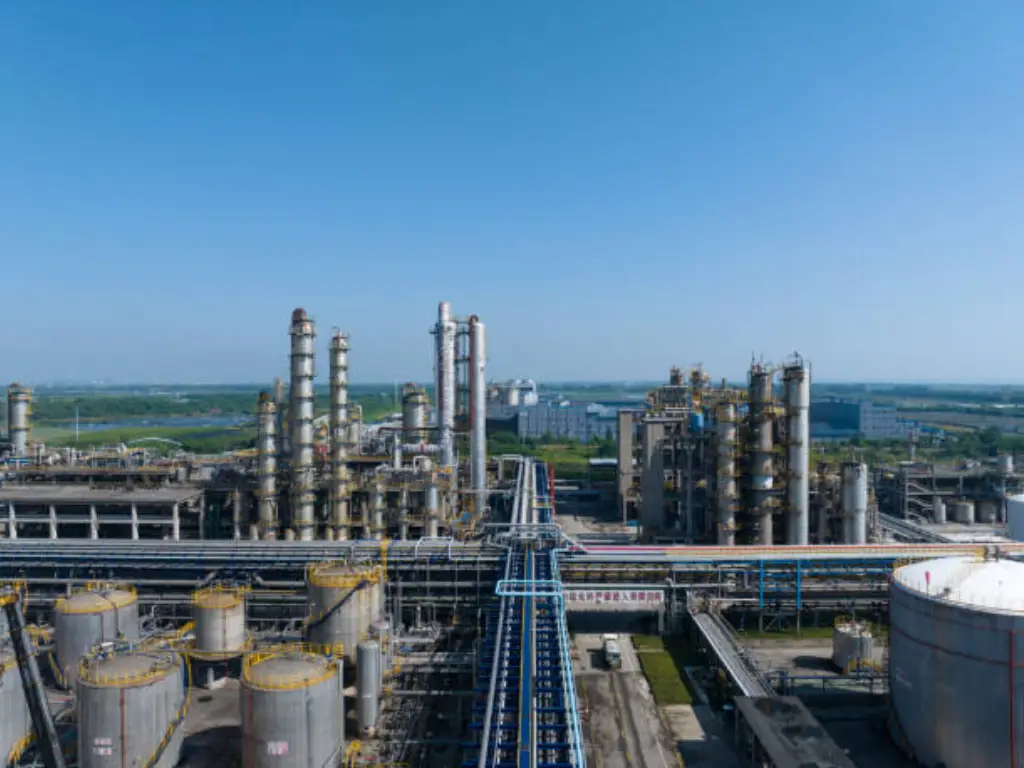
Chemical and Biological Methods for Oil-Water Separation
Chemical Demulsifiers and Emulsions
Demulsifiers are chemical agents which are used in oil and water separation and in emulsions breaking. These chemicals work on the principle of making the stability of the emulsions weak so that the two phases of oil and water can be separated with ease. Installation of Demulsifiers depends on the emulsion type as well as the characteristics of the oil and water. They may be placed in the oil-water mixture sequentially or may be injected into the separation device. Their application dramatically increases the efficiency of oil water separation processes.
Flotation Techniques: Microbubbles and Oil Recovery
Flotation utilizes microbubbles to lift oil droplets to the surface which facilitate the separation of the oil. In this type of the method, microair bubbles are mixed with the oil and water mixture and when they move up, they carry along with them the oil droplets. Such foams containing oils are then skimming, leaving clean water on the bottom sinks. Dissolved air flotation (DAF) and induced gas flotation (IGF) are two common flotation techniques which is employed in oil water separation. For the removal of small oil droplets, flotation is exceptionally effective and, if necessary, can be combined with other modes of separation.
Biological Treatment: Oil Pollutants Removal With Microorganisms
Biological methods include bioremediation, which employs microorganisms to eliminate oil pollutants in water. Some specialized bacteria and fungi can use hydrocarbons as food and transform them into water and harmless carbon dioxide. Biological treatment can either be in-situ, where the oil-contaminated water is injected with microorganisms, or ex-situ where the water is removed and placed in a bioreactor. However, it is worth mentioning that biological treatment is a slower method of seemed possible in all cases as compared to physical and chemical methods although it provides an efficient and economical way for oil water separation.
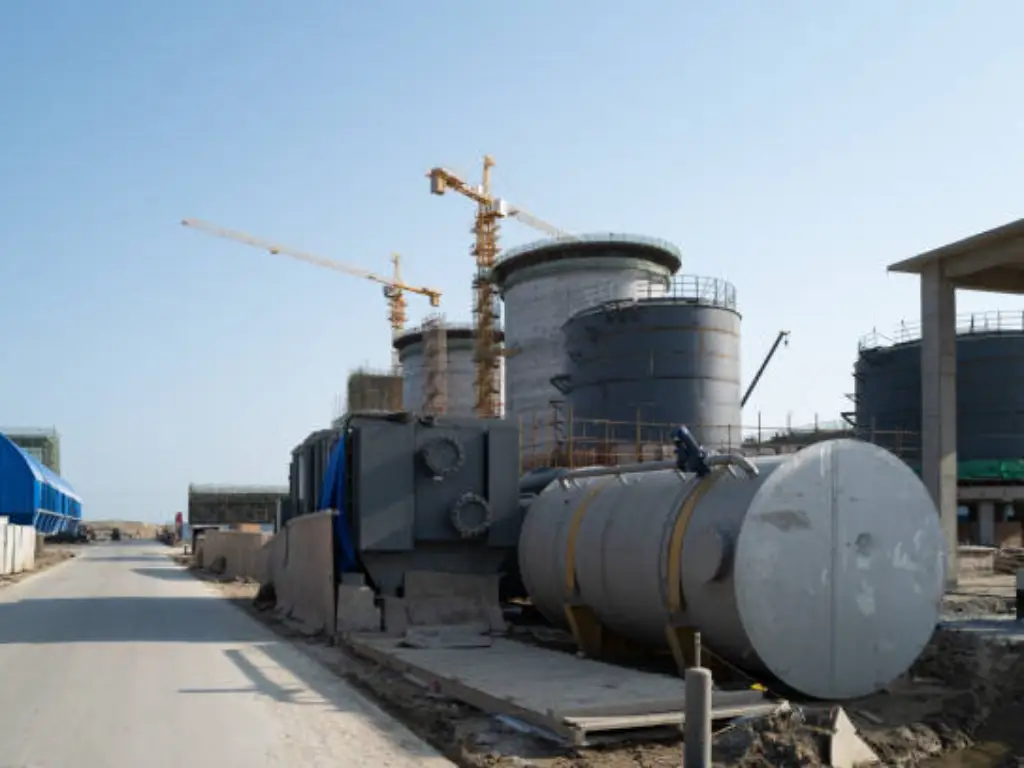
Thermal and Advanced Technologies
Thermal Methods: Distillation and Evaporation
Thermal techniques such as distillation and evaporation can be applied to separate oil from water due to the difference in their boiling points. In distillation the emulsion of oil in water is boiled under heat until the water is vaporized and the oil is stripped off. The vaporized water is then collected separately by condensation. On the contrary, evaporation is the technique that employs s heat where the water in the mixture is evaporated and removed by either vacuum or by air. Thermal methods are costly in energy but when applied, are effective in separating oils with high boiling points from water.
Membrane Technology for Complete Oil Removal
Membrane technology has been the focus of many researchers within the last couple of decades due to its potential for complete oil removal from water. Membrane technologies employ the principles of phase separation based on the selective passage of water while retaining the oil through membranes. Depending on oil droplet size, microfiltration, ultrafiltration, and nanofiltration different kinds of membranes are used. Membrane technology has characteristics of high separation efficiency, low energy requirements and can suit a wide range of oil concentrations. However, the disadvantage of membrane technologies is that they are subject to membrane fouling and therefore require regular cleaning and maintenance.
Molecular Sieves in Oil-Water Separation
Molecular sieves are crucial in oil water separation processes since they remove water from oil, improving the condition of the oil, thus its translocation and refining is easier. What makes them so effective is the fact that they have areas that attract hydrogen and oxygen atoms as well as pores that are optimized and only allow certain water molecules to pass while oil molecules are too large. Due to the high surface area and the pore volume of molecular sieves, they are able to absorb quite large amounts of water making them efficient water reduction so that oil is within the standards required.
Molecular sieves are typically used together with conventional oil water separation methods to achieve best results in practical situations. For example, in the processing of crude oil, molecular sieves can be utilized as a polishing operation after gravity settling or centrifugal separation to extract residual water content. Similarly, in the case of the treatment of oily waste water from refineries, molecular sieves may be applied together with flotation or filtration in order to adsorb dissolved water, thus increasing the efficiency of the overall separation process. Thus, by carrying out effective oil water separation through implementing specific molecular sieves as well as traditional separation techniques, great improvements in the quality of the oil products can be obtained.
Industries looking for durable and effective molecular sieve solutions should look no further than Jalon. Having an insight into the market and the customer needs, Jalon provides customized molecular sieves for various oil water separation processes. The ability to provide high quality molecular sieves at competitive prices combined with great service has further entrenched Jalon as a go to solution partner in the industry.
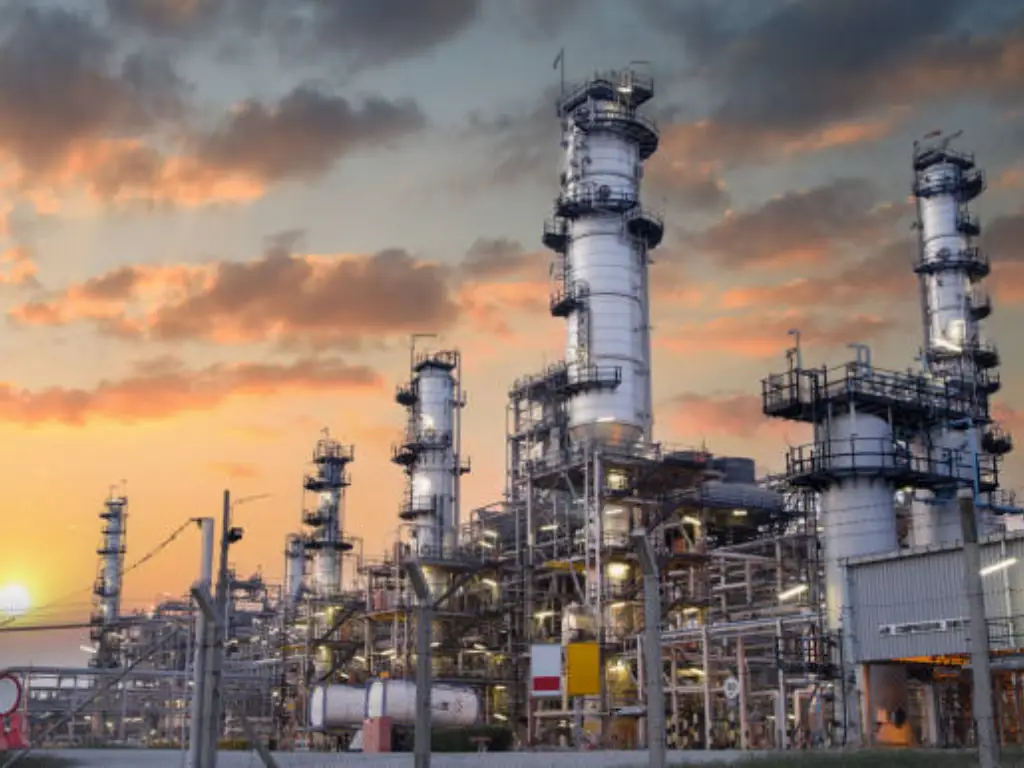
Oil-Water Separation in the Oil and Gas Industry
Oil water separation is one of the key processes employed in the oil industry. There is always a high percentage of water co-produced during the exploration and production process of petroleum which has to be separated from the oil before further processing or transport. Produced water refers to the oily water obtained after oil has been extracted and includes various forms of contamination including oil, grease, and salts. Environmental challenges set the framework to ensure oil water separation and the produced water can either be reused or disposed of in a safe manner. For separating oil and water effectively, the industry makes use of gravity separators, hydro cyclones, flotation units etc. These techniques are ineffective, thus continuous research is conducted in order to develop more efficient and economical separation processes with improved retention time for various industrial applications.
Conclusion and Future Trends in Oil-Water Separation
To conclude, oil-water separation is an important process that is used in various industries namely oil and gas, industrial wastewater treatment, etc. The method of separation mainly depends on the type of oil, oil concentration, required efficiency of separation and available resources. Oil-water separation offered through techniques like centrifugal separation and gravity settling are some of the commons practices, as newer technologies such as membrane filtration or molecular sieves are emerging due to their increased selectivity and effectiveness.
In the next decades, there will certainly be a significant advancement in oil-water separation techniques because there will be an urgent need for greener, more sustainable techniques. The enhancement of separation performance can be achieved through the development of innovative materials such as functionalized membranes and well-structured advanced adsorbents. Smart sensors technology more so integrated with automation technology can aid in separation optimization and minimize human input. The oil-water separation industry will have to adapt in order to address weaknesses regarding oil-water separation in an environmentally responsible manner because environmental policies will be stricter than before.