What Is Natural Gas Reforming and Why Does It Matter?
Industrial steam methane reforming is one of the oldest and most widely used methods of pure hydrogen production and is a critical component of the global energy supply. Of these techniques, steam methane reforming (SMR) is the most popular because of its high efficiency and the availability of the required infrastructure. The main difference is that this gas stream process is particularly important as hydrogen gas is one of the most important components of the transition to cleaner energy systems as it has a great potential for reducing greenhouse gas emissions.
Natural gas reforming hydrogen is used in different industries and applications as follows. It is a strategic fuel for operating fuel cells that are used in electric cars and other renewable energy applications. In addition to energy, hydrogen is used in the manufacturing of ammonia for fertilizers, methanol for chemicals, and even aircraft fuel andjet fuel. The capacity to generate hydrogen at industrial scale guarantees its position as the key enabler of the global shift to sustainable energy.
However, this process is not without challenges. Although it is cheap and commonly used, it depends on fossil fuels such as methane, which leads to high carbon footprint. To counter this, carbon capture and storage (CCS) technologies are required to reduce its effects on the environment. Also, natural gas reforming produces hydrogen and carbon dioxide, and the hydrogen produced must be further purified for commercial use. The main challenge that has to be addressed in order to further develop this technology is the ability to achieve the right balance between efficiency of the process, scalability, and sustainability.
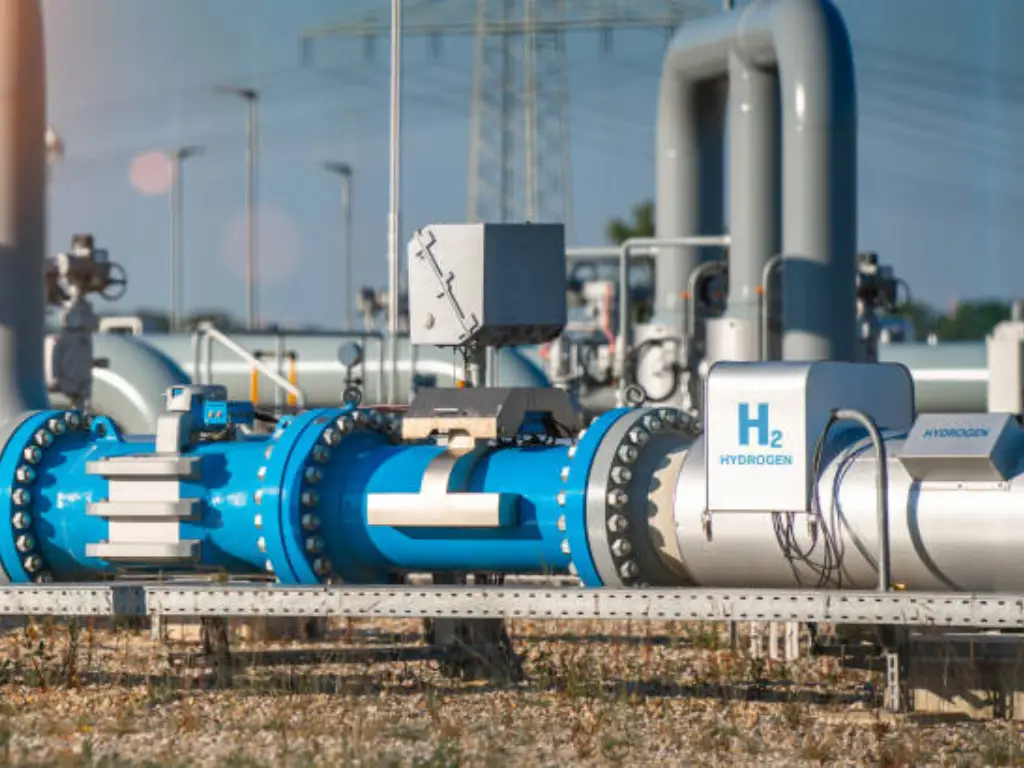
How Does It Work? Exploring the Science of Natural Gas Reforming
Natural gas reforming is a critical process for producing hydrogen, which is used across industries like chemicals, energy, and fuel cells. The process consists of three main stages: raw gas pretreatment, reforming reaction and syngas purification. It is thus pertinent to discuss every stage as follows.
Stage 1: Raw Gas Pretreatment
Raw natural gas is largely methane but comprises between 0.1 and 2% impurities like sulfur compounds, water vapor, and other heavy hydrocarbons. When ingested by the catalysts, they will poison the catalysts and lead to contamination and negatively impacting the process downstream, therefore the need for an initial pretreatment process to ensure the process is smooth and the catalyst’s lifespan is not shortened.
Removal of sulfur containing compounds is one of the most critical activities in this stage. Impurities like hydrogen sulfide (H₂S) are adsorbed by substances like zinc oxide (ZnO), which react with sulfur to give solid zinc sulfide (ZnS). This process effectively brings the sulfur content below 0.1 ppm to guard sensitive reforming catalysts.
Drying is equally important as moisture hinders the reforming reactions as well as subsequent purification steps. Of all the drying agents, molecular sieves (4A, 5A, 13X) are preferred because of their high selectivity, thermal stability, and capability to remove moisture to very low levels. They perform better than other materials such as activated alumina, which is more suitable for low moisture or high temperature applications, and silica gel, which is used as a second layer desiccant. Molecular sieves are preferred because they have a longer life span and are more effective in the removal of water, thus providing a very dry methane feed.
Finally, the high molecular weight hydrocarbons are removed to avoid coking on the catalysts and thus making the downstream process more dependable and durable. At the end of this stage the natural gas is a purified methane stream ready for the reforming reaction to take place.
Stage 2: Reforming Reaction
Now, the purified methane passes through conversion to syngas, which is a combination of hydrogen, carbon monoxide, and carbon dioxide. This step takes place at elevated temperature normally between 800 – 1000°C and uses nickel based catalyst to promote the reactions.
Steam methane reforming (SMR) is the most popular reforming process used in industries. Syngas is produced from methane by conversion of steam using a catalyst. This reaction is very efficient and yields methane conversion greater than 95%.
There are other types of reforming processes like auto thermal reforming (ATR) which may be employed in place of (or in addition to) SMR. ATR integrates partial oxidation with steam reforming, and generates heat within the process, thus reducing the external energy demand. This method is preferred in applications where carbon credits and energy saving are of paramount importance.
The reforming stage also contains the water-gas shift reaction (WGS). This is a secondary reaction whereby carbon monoxide reacts with water and forms more hydrogen and carbon dioxide. The WGS reaction optimizes hydrogen yield while decreasing the content of carbon monoxide in syngas to facilitate purification in a subsequent step.
Stage 3: Syngas Purification
Step | Goal | Method | Advantages |
Water-Gas Shift (WGS) | Increase hydrogen yield, reduce CO | Reaction of CO with water to produce H₂ and CO₂ | Enhances hydrogen production |
CO₂ Removal | Remove CO₂ | Chemical absorption with amines or PSA | High hydrogen recovery rate (>85%) |
Methanation | Convert residual CO to methane | Reaction of CO with hydrogen to produce methane and water | Increases purity (<10 ppm CO) |
Drying | Remove residual moisture | Molecular sieves (5A, 13X) | Delivers ultra-low dew points, ensures product stability |
The final step of natural gas reforming is the purification of syngas to the level of ultra pure hydrogen with the purity level often above 99.99 %. This means that undesired species like carbon dioxide, carbon monoxide, methane, water and others are stripped off because these may affect further uses.
The procedure starts with water-gas shift optimization, whereby residual carbon monoxide in the syngas reacts with steam to generate additional hydrogen and carbon dioxide. This step apart from improving hydrogen yield also serves to decrease levels of carbon monoxide for enhanced ease of removal.
Next, carbon dioxide removal is done either by chemical absorption with amines or by pressure swing adsorption (PSA). Amine scrubbing reacts with CO₂ with chemical solvents while PSA uses adsorbent materials such as zeolites to selectively adsorb CO₂ and recover more than 85% of the hydrogen.
Methanation then removes residual carbon mon oxide by converting it into methane and water using hydrogen. This step ensures that the CO level is reduced to less than 10 ppm, making the hydrogen stream safe for sensitive applications such as fuel cells.
Most people overlook drying in purification but the fact that as even trace moisture can damage equipment. Molecular sieves (5A, 13X) are the most widely used desiccants because of their high water adsorption capacity, thermal stability, and long service life. Low moisture or high temperature applications require other materials such as activated alumina while silica gel is used as a backup desiccant. Nonetheless, molecular sieves are more desirable due to their effectiveness in delivering extremely low dew points and thus, the quality and stability of the hydrogen stream.
Last but not the least, there remains a feature like cryogenic distillation or membrane technology to eliminate the loss of impurities. In facilities employing CCS technology, CO₂ is captured and stored after being compressed the move minimising emissions by as much as 90%.
Natural gas reforming is a process of hydrogen production which is slightly complicated but very effective. In the catalyst regeneration process, every step in conjunction with the pretreatment and the post reforming and purification stages are critical to high yields, equipment protection and product purity. Pre-ventative reactions such as the WGS and methanation reactions help to enhance efficiency and minimize contaminants. Of the critical technologies, molecular sieves continue to be the most popular drying agent, especially in high-temperature, low moisture, and precision adsorption applications. This is particularly due to a number of advantageous over other heat exchangers which include superior performance stability as well as well as ultra low moisture levels all of which are vital if the reforming process is to be guaranteed. With advancements in autothermal reforming and carbon capture, this technology remains relevant and continues to develop with the help of new developments in autothermal reforming and carbon capture.
Why Choose Jalon Molecular Sieves for Hydrogen Purification?
Jalon is one of the leading molecular sieve manufacturers in China and globally. With over 20 years of excellence, we offer unparalleled solutions to customers in 86 countries and regions, backed by 112 registered patents. Quality lies at the heart of Jalon’s brand, integrating ISO 9001 and ISO 14001 standards to ensure consistency and continuous improvement in every production stage.
Our cutting-edge R&D team, comprising 56 highly qualified experts, collaborates with leading scientists from academic workstations, this enables us to develop state-of-the-art molecular sieve technology, delivering superior hydrogen purification solutions. When you choose Jalon, you’re not just selecting a product—you’re investing in innovation, unmatched quality, and a partnership that will drive your success in the hydrogen industry.
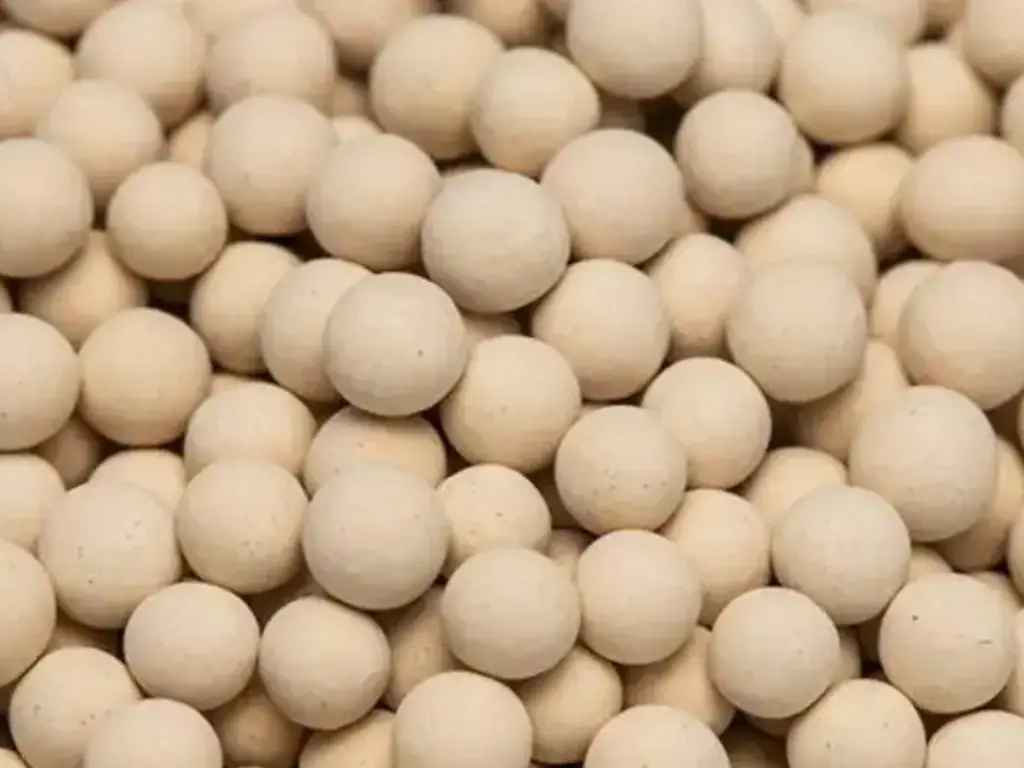
Why Is This Pathway Being Considered?
The most popular and effective technique for hydrogen production is natural gas reforming because of its effectiveness, flexibility, and integration with the existing facilities. Compared to other methods such as thermochemical water splitting or electrolysis, it is far cheaper, thus suitable for short to medium term hydrogen uses.
Today, most of the hydrogen is produced by natural gas reforming because natural gas is cheap and easily available especially in the United States. New developments in carbon capture and storage (CCS) have improved the process by reducing the effects of the process on the environment. Natural gas reformation can generate low carbon hydrogen also known as ‘blue hydrogen’ by trapping CO₂ emissions, thus supporting global decarbonization efforts.
This method is also very flexible and can be used for both medium scale applications and large scale hydrogen production. Its versatility enables it to satisfy the needs of various industries such as transportation (fuel cells and electric vehicles) and industrial processes including ammonia and methanol synthesis. Although the renewable sources like solar and wind energy are growing fast, they are not stable enough to replace the fossil fuel based hydrogen completely. Therefore, natural gas reforming plays an important role of a transition fuel, which is a step towards a cleaner and more sustainable energy.
What Are the Environmental Impacts and Challenges of Natural Gas Reforming?
However, natural gas reforming is not without its problems, and these are mainly environmental. The process also produces a significant amount of CO₂ emissions, which exist chiefly in the use of methane, a fossil fuel. These emissions, if not captured and stored, directly contribute to climate change, which is counterproductive to hydrogen’s function as a clean energy vector.
The process is also very energy consuming, as it needs a lot of heat to fuel steam methane reforming (SMR) at elevated temperatures. This energy is frequently produced by burning more fossil fuels, which means that the process of hydrogen production – an environmentally friendly fuel – is based on carbon-intensive processes.
However, small amounts of carbon monoxide (CO) are produced during reforming, which is hazardous to the workers and needs stringent environmental measures. Applying the process at a smaller scale adds additional inefficiencies and economic issues, as the technology is most effective at large scales.
To overcome these problems, improvements in SMR and water gas shift reactors are in the pipeline. Possibilities to enhance the efficiency of heat recovery systems and the conditions of the reaction might be the key factors. Besides, it is crucial to increase CCS technologies’ use to capture CO₂ emissions necessary for producing “blue hydrogen.” These are important because they help to reduce the relative environmental cost of natural gas reforming.
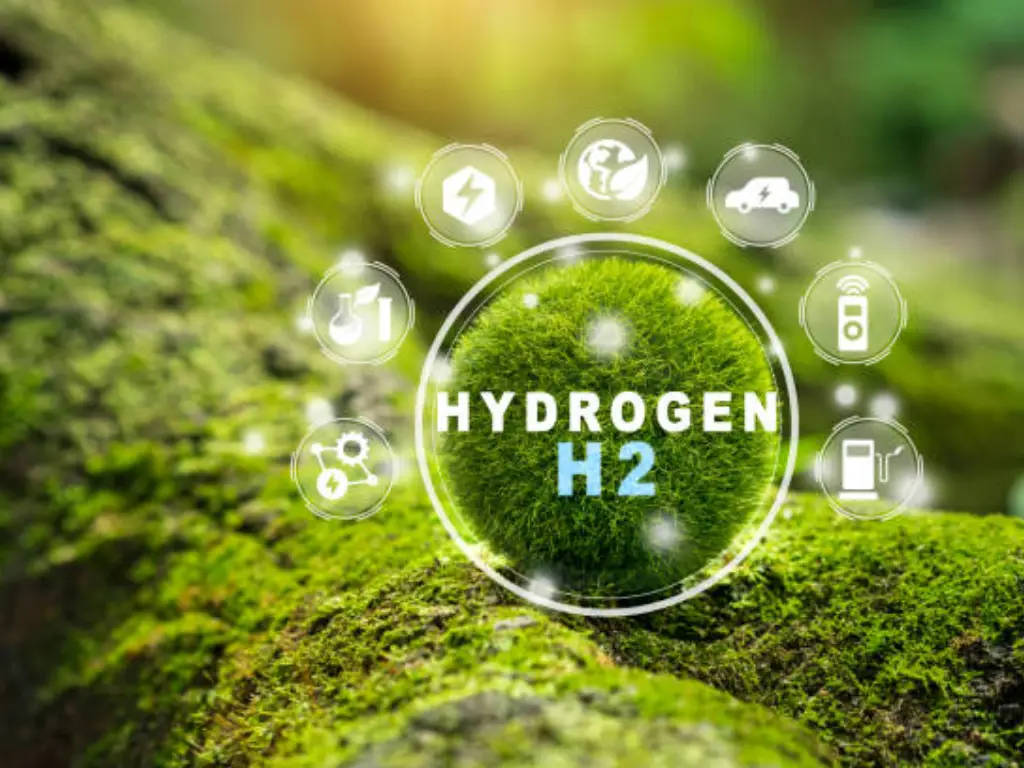
What Does the Future Hold for Natural Gas Reforming?
The future of natural gas reforming depends on the technological development and the trends towards decarbonization around the world. As hydrogen consumption increases in strategic markets such as electric vehicles and renewals, natural gas reforming will continue to be the leading method of production in the short future. However, its long-term sustainability is still questionable depend on harnessing carbon capture technologies, and changing towards cleaner ones.
Renewable hydrogen which is generated by the electrolysis of water which is driven by solar or wind power is expected to significantly change the current structure of hydrogen production and marketing. This is because the cost of renewable technologies is expected to reduce in the future and hence the use of natural gas reforming may reduce. It is also possible to find a symbiosis between renewable energy inputs and reforming systems as a potential intermediate solution for mass production of hydrogen.
Steps to make processes more efficient, cutting carbon, and pursuing heat recovery will continue to be valued in the industrial sector. Moreover, government incentives and the development of hydrogen infrastructure will determine further perspectives of this technology, especially in the USA and different countries in Europe.
While environmental issues remain an issue, natural gas reformation will remain a part of the hydrogen production process as a bridge from the current fossil fuel infrastructure to a future hydrogen economy.