Introduction
From the pharmaceuticals industry to oil and gas, nitrogen has become an integral part of numerous sectors. With nitrogen generators, nitrogen can easily and cost-effectively be sourced for blanketing or purging. Like all precision machines, however, nitrogen generators require proactive care and maintenance to work effectively and within their intended lifespan.
This article provides a brief description of the most important measures to follow in order to maintain the nitrogen generator and guarantee a constant nitrogen supply. By following these best practices, you protect your equipment investment and ensure operational reliable, which is critical for sustained performance in challenging industrial applications.
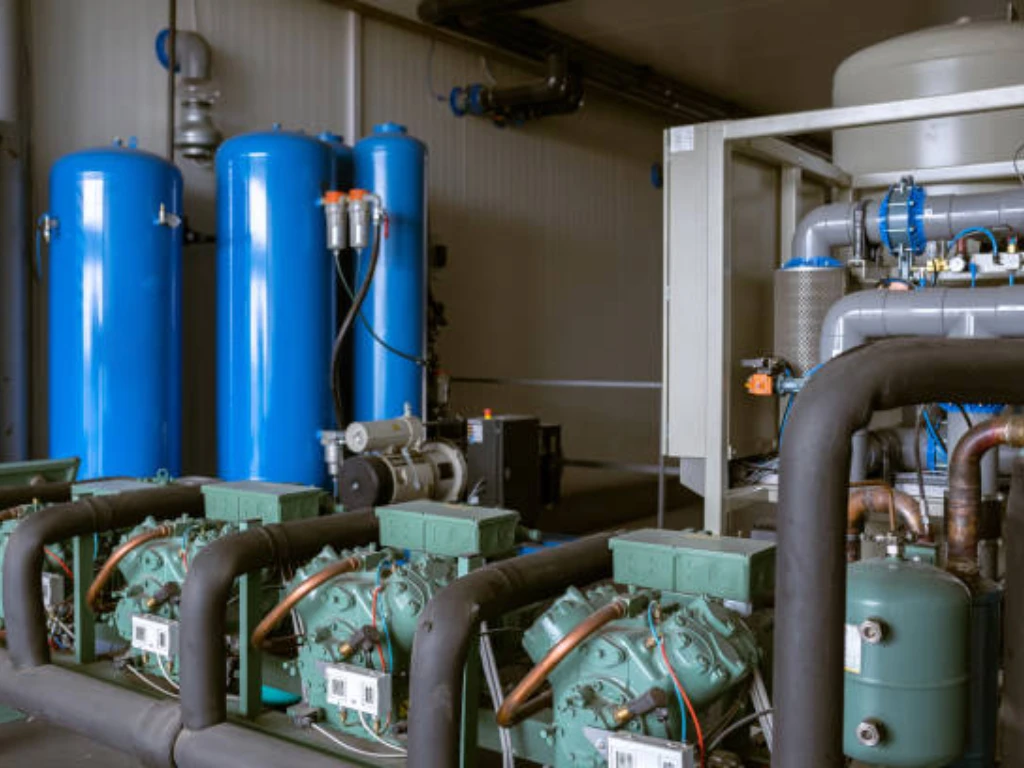
Why Regular Nitrogen Generator Maintenance Matters
Envision your nitrogen generator as an instrument that has been crafted to perfection. Just as a musician maintains their instrument to produce the best sound, consistent maintenance is central to ensuring that your nitrogen generator continues to provide the desired purity and flow of nitrogen. Ignoring generator maintenance can have a spiral of adverse consequences. Efficiency can decline, causing the system to work more and harder, and as a result, consume more energy. This increase in energy consumption raises operational costs. In due course, small problems may develop into major problems, which means that the company will have to spend a lot of money on repairs and, in the worst-case scenario, have to deal with downtimes that affect important processes.
Furthermore, the longevity of your investment hinges on proper upkeep. A well maintained nitrogen generator will just last longer and this will give you more value for your money that you used to purchase it. This is because regular checks and replacement of worn out parts ensure that they do not fail prematurely and thus increase the life cycle of the system.
Apart from the savings aspect, the safety of the operations seems to also benefit from consistent maintenance. Most risks associated with a poorly maintained system can be avoided through effective due inspections that help mitigate incidents before they turn into big problems. In short, expenses incurred through regular maintenance of a nitrogen generator can be seen as investments geared toward enhancing operational efficiency and safety over a certain stretch of time.
Essential Maintenance Aspects for Nitrogen Generators
The tasks required in the maintenance of a nitrogen generator are broad in scope, consisting of routine maintenance chores common to all systems and more specialized ones associated with the particular technology. These vital aspects guarantee that all necessary systems and parts are operational in a complete and dependable manner to the process of nitrogen generation.
Fundamental Maintenance Practices
To keep a nitrogen generator running efficiently, some general maintenance practices are necessary. Every generator regardless of type, requires maintenance and care to be performed on a regular basis for optimum work and prolonged durability.
- Visual Inspections: Early opportunities to detect concerns are defined by both scheduled and unscheduled inspections. Some qualified personnel shall search for leakage, rusting, and abnormal sounds. All gas holding connections, fittings, hoses, and administrated parts must be checked for physical deterioration to prevent outflow of gas and pressure retention.
- Air Intake and Exhaust Systems: These systems are key to the power plant functioning. Performance repercussions are caused by the blockage of air intakes since they restrict air there. On the same note, the exhaust being obstructed results in backpressure causing a reduction in efficiency. Both systems having unobstructed clear ends is necessary for easy operation.
- Pressure and Temperature Checks: An unscheduled pressure and temperature check has to be done on a frequent basis to catch system anomalies. Take noting for example, if a pressure reading is stabilising above 6 bar, there is a probable system defect. The level of pressure and temperature should be within specified limits at all times for them to function smoothly.
- Cleaning: The generator can be affected by cooling debris and dust. To ease contamination and keep heat build up at bay, the outside surface should be cleaned regularly using a moist cloth. Too much water should not be used especially in the vicinity of electrical components.
- Maintenance Schedule: Following the scheduled maintenance as proposed by the manufacturer within the operator’s manual is important because it tells you what maintenance is to be performed, and when it is to be performed to maximize efficiency on the equipment.
Complying with these guidelines will increase the service life of the nitrogen generator and also reduce maintenance downtime.
Technology-Specific Maintenance Guidelines
General maintenance practices serve as the cornerstone of an effective maintenance plan, however, the specific technology used by the nitrogen generator requires specially tailored maintenance considerations. Different technologies rest on different bases for nitrogen generation which confirms that their maintenance needs differ.
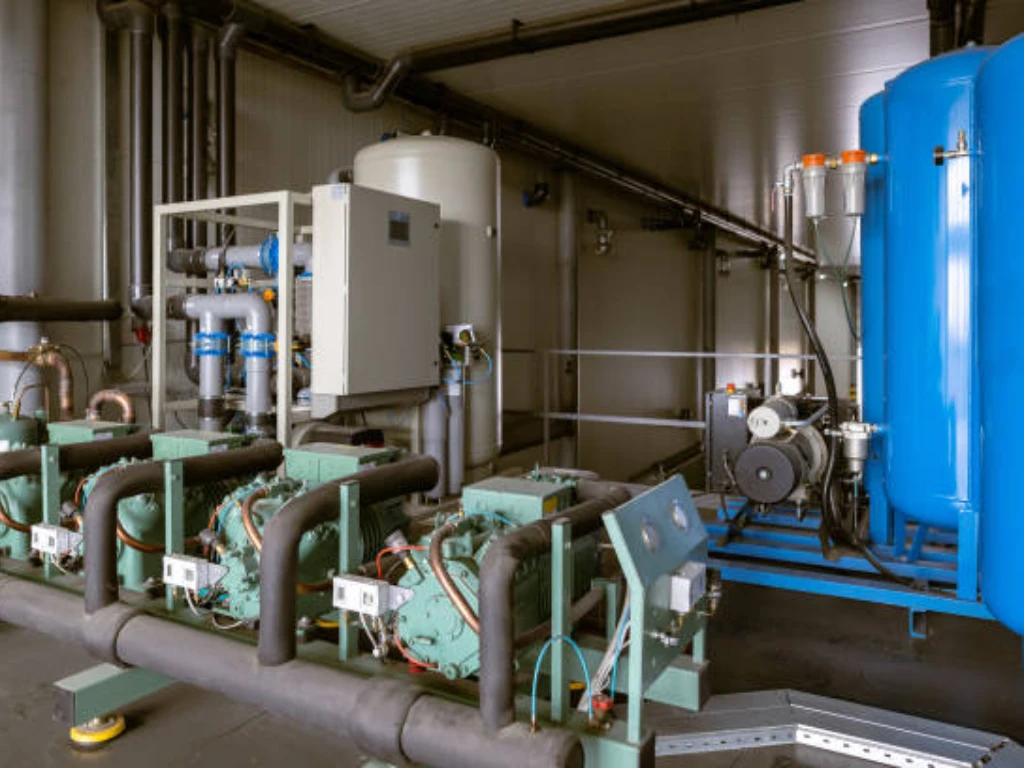
Membrane Nitrogen Generators
Membrane nitrogen generators employ the use of semi-permeable membranes to separate nitrogen from air. The membrane modules require constant care and attention, and the most important aspect is to ensure that they are clean and functional.
- Leak Checks: It is important to check for leaks around the membrane housing and connections on a regular basis. Leakages are always a problem that can lower the nitrogen purity and the efficiency of the system and must be addressed as soon as possible.
- Air Quality and Pre-Filtration: The quality of the compressed air that enters the system is directly proportional to the life of the membrane. It is important to keep the pre-filtration system in good condition, which is the coalescing filters and the activated carbon filters. These filters help to eliminate such substances as oil and water vapor that may harm the membranes.
- Flow Rate and Purity Monitoring: It is also important to monitor the flow rate and the purity of the nitrogen gas. Either of the two may decrease and this may be an indication that the membranes are not functioning optimally and may require cleaning or replacement.
- Membrane cleaning: Mild cleaning of the membrane surface may restow performance in specific membranes and prolong its longevity, contrary to popular belief. However, the membranes will deteriorate over time, usually after a period of 5-7 years and will need to be replaced to achieve the desired output.
The capability and effectiveness of membrane nitrogen generators can be achieved by affirmatively constructing these maintenance steps.
Cryogenic Nitrogen Generators
Cryogenic nitrogen generators, which are suitable for high purity applications, work by cooling air and then liquefying and distilling to separate nitrogen. Because of this, it is essential to perform routine and thorough maintenance on the equipment since they are complicated.
- Refrigeration System: It is important to monitor the condition of the compressors and the heat exchangers frequently. Leakage of refrigerant affects the cooling process and therefore it is important to detect and repair any leakage.
- Frost Buildup: Check for frost on cold surfaces as this may affect heat transfer. It is important to adhere to the manufacturer’s recommendations when it comes to defrosting in order to keep the system running optimally.
- Purity Monitoring: Nitrogen purity is one of the most important parameters that define the system efficiency. Any variation in the purity levels should be addressed as soon as possible to avoid the production of low quality nitrogen.
- Insulation: The insulation of the system should be in good condition to avoid heat transfer and keep the cold temperatures. Checking the insulation for signs of damage or deterioration is important in order to prevent energy loss.
Due to the complexity of cryogenic systems, it may require more expertise and may entail more complicated processes than other technologies to maintain.
Pressure Swing Adsorption (PSA) Nitrogen Generators
PSA nitrogen generators work on the principle of adsorption where nitrogen is separated from the air. It uses adsorbent materials such as zeolite molecular sieves where oxygen is adsorbed at high pressure and nitrogen is allowed to pass through. It is important to maintain the system in order to make it work effectively and last longer.
- Pre-Filtration System: The air pre-filtration system is very important in the performance of PSA generators. Some of the factors that affect the performance of the molecular sieve include dust, oil, and moisture which hinder the adsorption process by blocking the pores of the molecular sieve. It is important to replace the filters as often as the manufacturer recommends to avoid the contamination of the adsorbent material.
- Molecular Sieve Performance: Molecular sieve may allow some contaminants, moisture, or wear over time resulting in reduced capture efficiency. Reduced nitrogen purity or output is a direct signal of sieve degradation, if the purity level is below the set standard, then it may be time to replace or regenerate the molecular sieve.
- System Integrity: The valves, compressors, and pressure switches of the system are checked periodically to ensure that the PSA process is efficient. Defective parts can alter the pressure fluctuations and impact the efficiency of the nitrogen separation.
Last but not the least, the selection of right and quality molecular sieve is very important for the PSA system. Jalon is a professional manufacturer of molecular sieve adsorbents and we know that high-quality molecular sieves play a crucial role in the performance of PSA nitrogen generators.
Having more than 20 years of experience coupled with thorough understanding of adsorption technology, Jalon provides a wide range of molecular sieves for different brands and models of nitrogen generators to guarantee the stable and efficient operation of your equipment.
Our products, with 112 patents and strict quality control, provide high compression strength, high bulk density, and high adsorption capacity, providing stable and reliable nitrogen production for various industries.
By paying attention to these key areas of maintenance, PSA nitrogen generators can deliver a consistent nitrogen supply and high operational performance. This is because regular checks and timely replacements help to ensure that the system is running at its optimum.
Troubleshooting Common Nitrogen Generator Problems

Despite the best care, some issues may occur with nitrogen generators from time to time. One of the most frequent issues is low nitrogen purity. In PSA systems, this is due to the deterioration of the molecular sieves and may need to be checked and replaced. In membrane systems, a reduction in purity may be due to poor air quality or membrane deterioration.
Another common problem is a low nitrogen production rate. This can be caused by blocked filters that limit the flow of air, leaks that decrease the pressure of the system, or worn-out adsorbent material in PSA generators. In membrane systems, a decline in output could be attributed to membrane fouling or wear.
Another issue is the fluctuating system pressure due to the problems with the air compressor, pressure regulators, or leaks in the nitrogen generator. If pressure fluctuations are to continue, these components must be checked.
Also, any strange sounds during operation should not be overlooked. Noise produced by the compressors, valves or any moving parts may be an indication of mechanical deterioration or failure. It is important to note that these problems can be fixed early before they cause significant damage that will require expensive repairs.
Lastly, control system alarms are extremely important and should be solved as soon as possible. Referring to the manufacturer’s manual to check for error codes and recommended actions helps correct issues ina timely manner. This is due to the fact that constant surveillance and immediate action when there are any discrepancies ensure that the generators are always reliable.
Tips for Extending Nitrogen Generator Lifespan
Tip | Description | Frequency |
Proper Ventilation | Maintain adequate airflow around the generator to prevent overheating. | Daily |
Monitor Inlet Air Quality | Check and maintain the air pre-filtration system to remove moisture, oil, and particles. | Regularly |
Drain Condensate | Drain collected condensate in the air receiver and nitrogen generator to avoid corrosion. | Daily/Weekly |
Check for Leaks Often | Inspect connections, fittings, and hoses for leaks using soapy water or a leak detector. | Regularly |
Pressure and Temperature | Monitor pressure and temperature to avoid exceeding recommended levels. | Daily |
Filters | Replace air intake filters, pre-filters, and other filters as recommended. | As scheduled |
Valves | Inspect all valves for proper function and leakage. | Periodically |
Clean the Area | Keep the nitrogen generator free from dust and contaminants. | Regularly |
Performance Tests | Check nitrogen purity and flow rate for signs of poor performance. | Regularly |
Professional Servicing | Conduct professional servicing by qualified technicians for intensive checks. | Annually/Bi-annually |
Conclusion
A steady supply of nitrogen is crucial in most industrial operations, making a nitrogen generator one of the most important pieces of equipment. Proactive maintenance on the device is not optional, as it greatly improves performance, prolongs the generator’s working life, and protects the operational and economic efficacy of your processes. Trying to implement all the steps in this guide, which ranges from basic and regular checks and filter changes to more complex and timely fault fixes, including changing the filter elements, ensures the best gains in system health and productivity over time. Think of the system like an asset that, when taken care of, improves reliability, reduces costs, and most importantly, ensures peace of mind.