What is Oil and Gas Separation?
The process of oil and gas separation is crucial in the petroleum industry as it helps in the separation of crude oil, natural gas, and water for further processing and transportation. When oil and gas come out of the wellhead, they are in a state of a multiphase system that comprises of hydrocarbons, water, and at times solids. When there is no separation, downstream refining and transport are affected and this leads to operational problems and high costs.
The main goal of the oil separation process is to maximize the purity of each component with the least amount of energy and time. Effective separation improves productivity, reduces wear and tear of equipment and helps in meeting the legal requirements of environmental impacts. It works like the traffic light system of a city where each component is guided to its proper place to prevent traffic jam and delay. This not only safeguards the infrastructure but also enhances the efficiency of hydrocarbon recovery, which is a key element of the current gas industry.
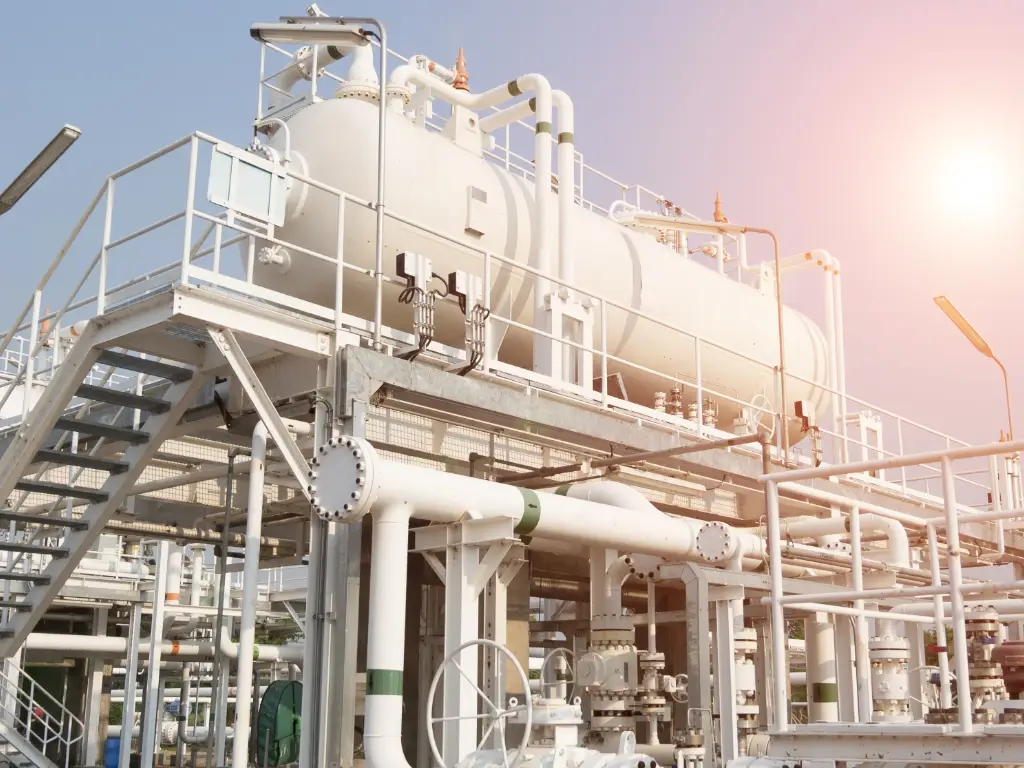
Key Equipment Types and Functions
Two-Phase Separators
Two-phase separators are used to separate the well fluid into two phases, which are gas and liquid, which in this case is oil and water. They work on the basis of density difference and gravity displacement. When the mixture enters, the gas goes up to the gas section and is released while the liquid is left at the base of the tank. These separators are used in the first stage of separation in the oil and gas industry. They are used in storage tanks, wellhead, and production facilities where water content is low. Their simple design makes them cost-effective, but they may need further processing if a large amount of water is to be removed.
Three-Phase Separators
Three-phase separators split the well stream into gas, oil, and water, which is essential for fields with a high water content. They operate based on the principle that the denser water sinks to the bottom, oil forms the middle layer, while the gas floats on the surface. It is therefore important to control the levels of the liquid and the flow of the gas in order to achieve the best separation. These separators are widely used in offshore platforms, oilfields, and gas processing plants where high purity separation is desired. While they are more complicated than two-phase separators, they offer a better level of separation and enhance the efficiency of downstream processing.
Cyclonic Separators
Cyclonic separators work on the principle of centrifugal force to separate the gas from the liquid. The incoming mixture is at high velocity and the heavier liquid particles move towards the walls of the separator and then downward while the lighter gas goes up. Due to their small size, they are suitable for use in offshore platforms and other areas where space and weight are limited. They are effective for handling high gas flow rates and are less affected by flow rate fluctuations. But they may not offer as high a separation efficiency as gravity-based separators in cases of fine mist or low density differences.
Vertical Separators
Vertical separators are based on the principle of gravity to enable the separation of the gas from the liquid. Gas rises to the top of the vessel while the liquid collects at the base of the vessel due to the force of gravity. Its design is especially advantageous when the gas-to-liquid ratio is high because the upward flow of the gas helps in the removal of the liquid. They take up less space on the ground, which makes them ideal for offshore and space-limited environments. However, they may have lower separation efficiency than the horizontal separators. They are widely applied in wellhead separation where the production of gas is usually high.
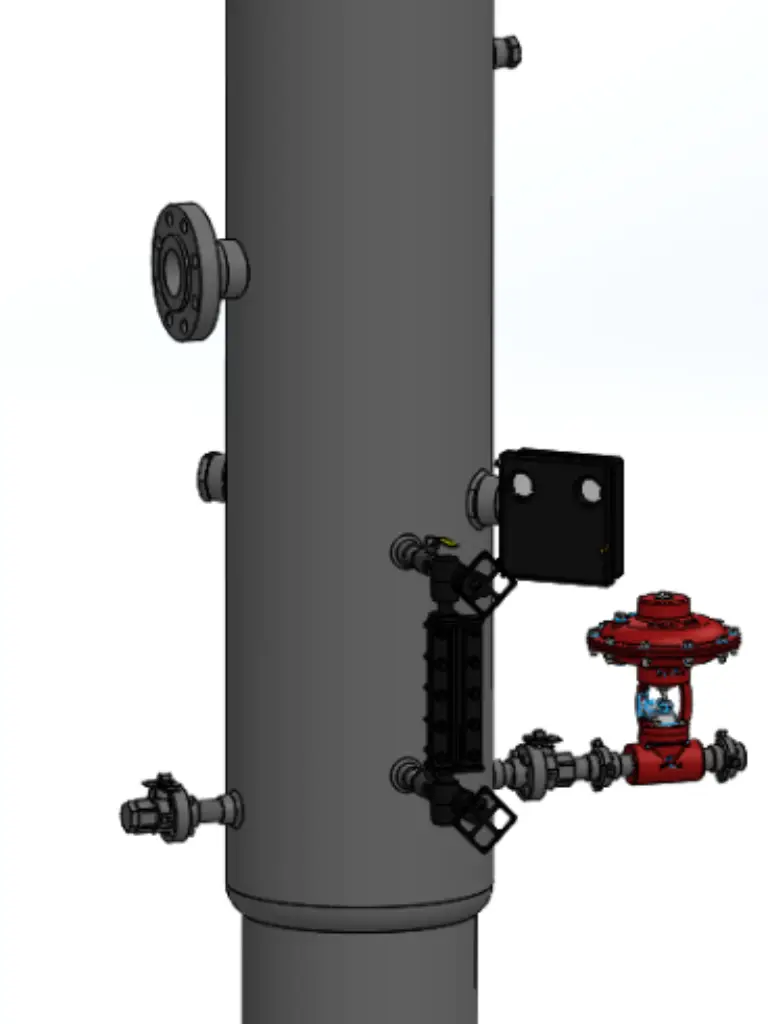
Horizontal Separators
Horizontal separators also offer longer flow lengths, which enhance the separation of oil, gas, and water. This is because the longer retention time allows for better separation of different phases. These separators are suitable for use in systems that handle large volumes of liquid and have relatively steady oil to gas ratios. They have a larger size which enables them to handle more volume, and therefore are suitable for central processing facilities and oil field gathering centers. However, they need more space and structural support than the vertical separators. They are widely used in on-shore oil production facilities where efficient phase separation is crucial for downstream processing.
Oil and Gas Separation Process
Inlet Separation
When the well fluid enters the separation system, it typically consists of a mixture of oil, gas, and water, often under high pressure. The fluid is directed through the inlet pipe into the first stage separator, where the separation process begins. Mechanical devices such as inlet diverters help distribute the fluid evenly, preventing turbulence and ensuring an efficient separation process. The initial step is crucial as it sets the stage for the subsequent phases by reducing gas entrainment in the liquid and ensuring a stable flow for effective processing downstream.
Primary Gas-Liquid Separation
At this stage, the force of gravity is used to help in the separation of the fluid phases depending on their densities. Gas, being lighter, rises to the gas section, while liquid hydrocarbons settle at the bottom of the tank. Some gas separators employ cyclonic separation or centrifugal separation as a way of increasing efficiency, especially in cases where the separation has to be done quickly. The gas is then allowed to rise to the top of the separator and is then channeled to the next process while the liquid is channeled to the next phase of separation. Proper instrumentation also helps in controlling the flow rate and pressure variations.
Oil-Water Separation
After the initial step of gas removal, the liquid that is left is a mixture of oil and water and hence needs to be separated. In separators, water being denser, settles at the bottom, oil forms the middle layer and any remaining gas floats on the top. In some cases, it is required to break stable emulsions with the help of demulsifiers. The separated liquid hydrocarbons are then transported to the processing facilities while the water is either treated for use again or injected back into the reservoir. Optimization of the oil-water separation increases the level of compliance with environmental standards and increases the yield of hydrocarbons.
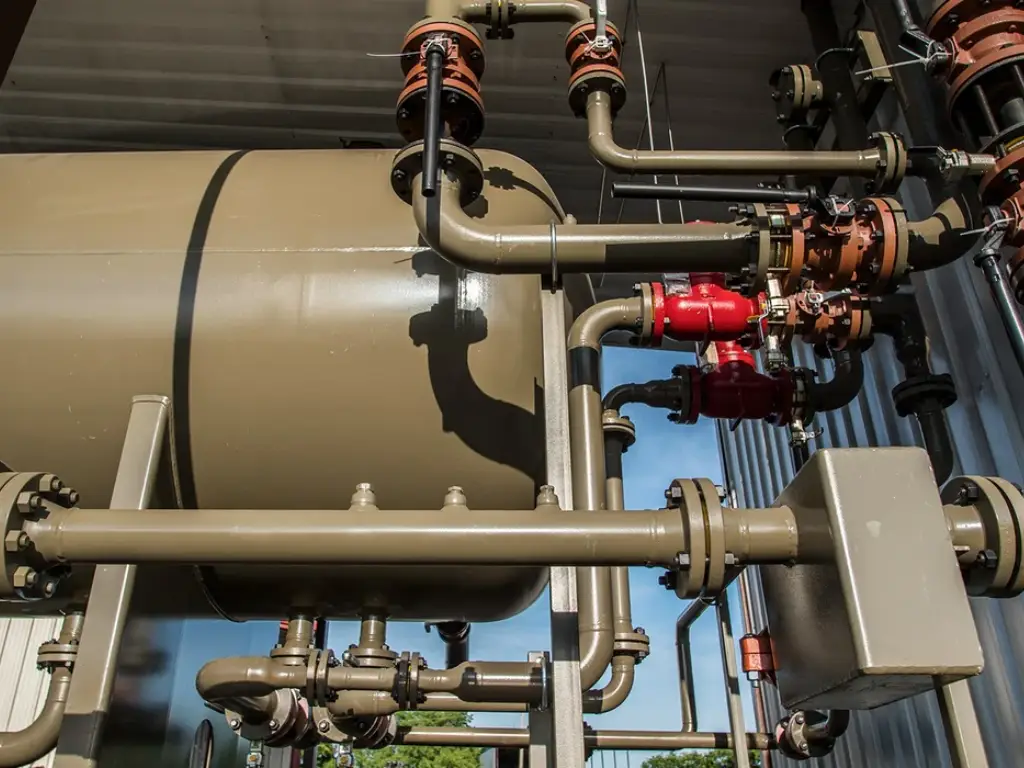
Gas Conditioning and Dehydration
The separated gas may contain water vapor and carbon dioxide (CO₂) which must be eliminated to avoid pipeline corrosion and hydrate formation. Deep dehydration is normally achieved by using molecular sieves and glycol dehydration systems. It may also be compressed using compressors to raise its pressure for transportation to the desired location. In conjunction with heating or cooling processes, gas conditioning makes certain that the gas is at the right psi for further processing or sale. This step is very important in the purification of the gas and also in the transportation of the gas through pipelines.
Liquid Storage and Transportation
After that, the processed oil is kept in storage tanks before it is shipped to the refineries for further processing. Water that is separated from the oil stream is either treated and then let out or is injected back into the reservoir to keep pressure up. Valves and heating control systems help to maintain the stability of the oil and to avoid the formation of wax or hydrates during storage and transportation. The transportation process must also meet safety and environmental concerns to avoid spillage and to enhance the flow of oil in the distribution networks.
Second Stage and Final Separation
In some instances, there is a second stage of separation especially in low pressure oil fields or fields with high water cut. This stage may include flashing where a sudden pressure drop causes dissolved gases to vapor phase and enhance the stability of the oil. Heating may also be used to strip out any residual light hydrocarbons like propane, ethane, butane and so on to meet the pipeline quality. The final purification is done by advanced scrubbers and secondary separators to ensure that any remaining impurities are eliminated before storage or transportation.
What Role Does Molecular Sieve Play in the Separation Process?
From the above process of oil and gas separation, it is evident that molecular sieves are very important in the dehydration process to the required specifications of both crude oil and natural gas. During separation, raw hydrocarbons contain water vapor that causes pipeline corrosion, formation of hydrates and reduction in the efficiency of processing.
Molecular sieves 3A, 4A, 5A, and 13X are used in adsorption units to remove water from natural gas streams to prevent formation of hydrates and enhance further processing. Molecular sieves are used in combination with compressors in separation plants to achieve the best outcome in the treatment of the gas. Glycol dehydration can also be used but the molecular sieves provide deeper dehydration which is required in the processing of propane, ethane and butane.
Below is a comparison of different molecular sieve types used in natural gas dehydration:
Molecular Sieve Type | Pore Size (Å) | Application | Advantages |
3A | 3 | Dehydration of natural gas and LPG | High water selectivity, prevents hydrocarbon co-adsorption |
4A | 4 | General gas dehydration, CO₂ removal | Effective water adsorption, versatile use |
5A | 5 | Hydrocarbon separation, gas drying | Suitable for both dehydration and hydrocarbon separation |
13X | 10 | CO₂ and H₂S removal, deep dehydration | High adsorption capacity, multi-purpose |
Jalon Molecular Sieves for Superior Performance
Jalon is a manufacturer of molecular sieves that provides a series of high-performance molecular sieves for oil and gas separation to meet the needs of dehydration and impurity removal. Their 3A molecular sieve is ideal for natural gas dehydration, it does not adsorb hydrocarbon and therefore does not alter the composition. The 4A and 5A molecular sieves have better water and light hydrocarbon adsorption to enhance the purity of the gas. When both CO₂ and H₂S need to be separated, the best adsorbent is the 13X molecular sieve. They have used their molecular sieves in different oil and gas plants around the world and have offered the following advantages:
- Superior moisture adsorption for extended dehydration cycles.
- Customizable solutions tailored to unique operational needs.
- Rigorous quality control ensuring consistency and reliability.
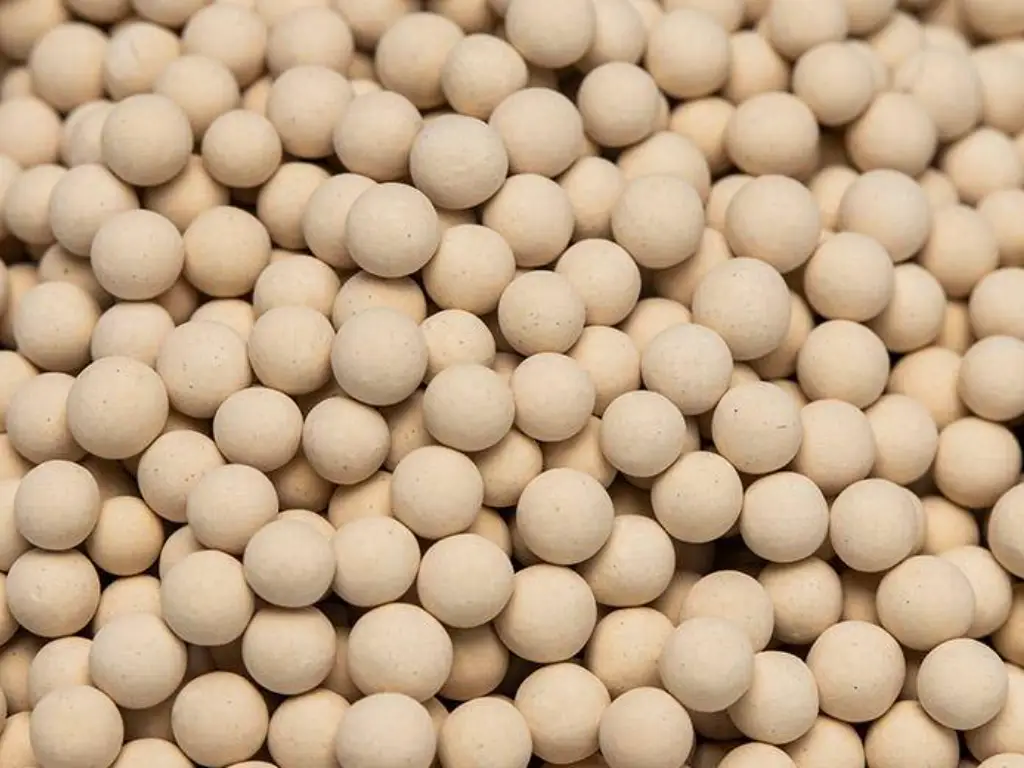
Optimizing Separation Processes & Future Trends
Optimization of oil and gas separation is a process that requires to be done on a continuous basis. Some of the ways through which efficiency is attained and energy is saved include multistage separation, automation of process controls and continuous monitoring. In the future, the industry is gradually shifting to the use of cleaner methods of separation that are more sustainable and less hazardous to the environment. Molecular sieves will be the main component of the new generation of gas treatment technologies that will be more efficient and cost effective.
Conclusion
Oil and gas separation is an important process that is applied to increase the yield of hydrocarbons and the reliability of the system. By understanding the separation process, selecting the right equipment, and using new molecular sieves, operators can obtain high production rates at a low cost. Molecular sieves from Jalon offer the highest level of dehydration, better quality of the gas and productivity for your business. As the industry shifts towards sustainability and energy efficiency, innovative solutions like molecular sieves will continue to shape the future of oil and gas.