The influence of different particle sizes of molecular sieves on application.
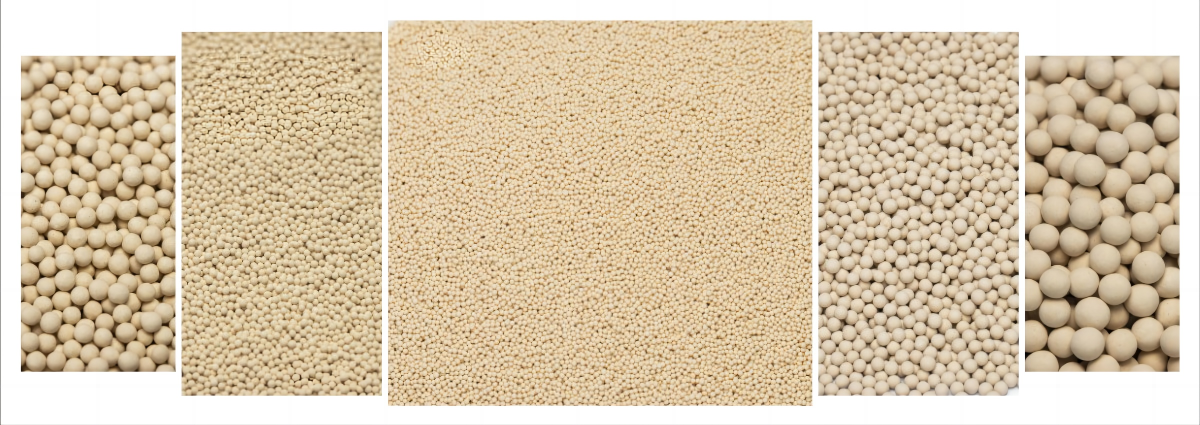
Molecular sieve is a kind of hydrated aluminosilicate with the function of sieving molecules. It has many pores with uniform pore size and neatly arranged pores in its structure. Different molecules can be separated according to different pore sizes. Molecular sieves with different pore sizes can sieve molecules of different sizes and shapes. For example, 3A molecular sieve can only adsorb molecules smaller than 0.3nm, 4A molecular sieve can only adsorb molecules smaller than 0.4nm, and 5A molecular sieve can only adsorb molecules smaller than 0.5nm. Therefore, when selecting a molecular sieve, the appropriate type of molecular sieve should be selected according to the size and shape of the target substance to be separated, so as to achieve the best screening effect.
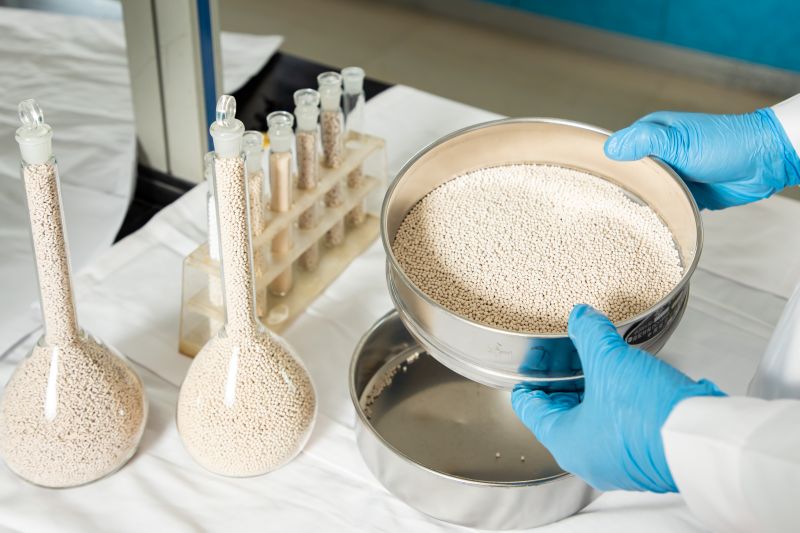
Common spherical molecular sieve particle sizes are 4*8 mesh (φ3-5mm), 8*12 mesh (φ1.6-2.5mm), 10*18 mesh (diameter 1-2mm). The particle size of molecular sieve refers to the diameter of molecular sieve particles, which has an important influence on the application of molecular sieve. This article introduces the influence of different particle sizes of molecular sieves on the application from the following aspects:
- Adsorption performance (mass transfer rate): Generally speaking, the smaller the particle size, the larger the specific surface area, the faster the mass transfer, and the stronger the adsorption capacity. When used as a desiccant, one gram of molecular sieve can absorb up to 22% of its own weight in water. Therefore, in applications that require efficient drying or removal of impurities, molecular sieves with relatively small particle sizes should be selected to improve their adsorption performance.
- Pressure drop: The particle size of the molecular sieve will also have a significant impact on the pressure drop that occurs during its application. In general, smaller particle sizes tend to result in higher pressure drops compared to larger particle sizes. This is because smaller particles have a higher surface area per unit volume, which results in more points of contact between the gas or liquid being filtered and the sieve material. As a result, there is greater resistance to gas or liquid flow through the screen, which translates into a higher pressure drop. Conversely, larger particles have less surface area per unit volume, which means fewer contact points and less resistance to gas or liquid flow, which results in lower pressure drop.
- Crush strength: The particle size of a molecular sieve has a significant effect on its crush strength, or the amount of pressure or force that can be applied to it before it breaks or crushes. In general, larger particle sizes tend to have higher crush strength than smaller particle sizes. This is because larger particles have less surface area per unit volume, which means they are less susceptible to surface imperfections or imperfections that would weaken the material. Conversely, smaller particles have a higher surface area per unit volume, which means they are more prone to surface defects, cracks and other imperfections that reduce their crush strength. In addition, smaller particles may also be more susceptible to attrition, the process by which small particles are shed from the surface of larger particles due to mechanical stress or friction. This further weakens the material and reduces its crush strength.
- Flow performance: The particle size of molecular sieve also affects its flow performance. Generally speaking, the larger the particle size, the smaller the flow resistance and the faster the flow speed. This is advantageous for some applications requiring fast separations. For example, in the process of gas or liquid purification, catalysis, adsorption, etc., it is necessary to choose a molecular sieve with a larger particle size to reduce flow resistance and increase flow velocity.
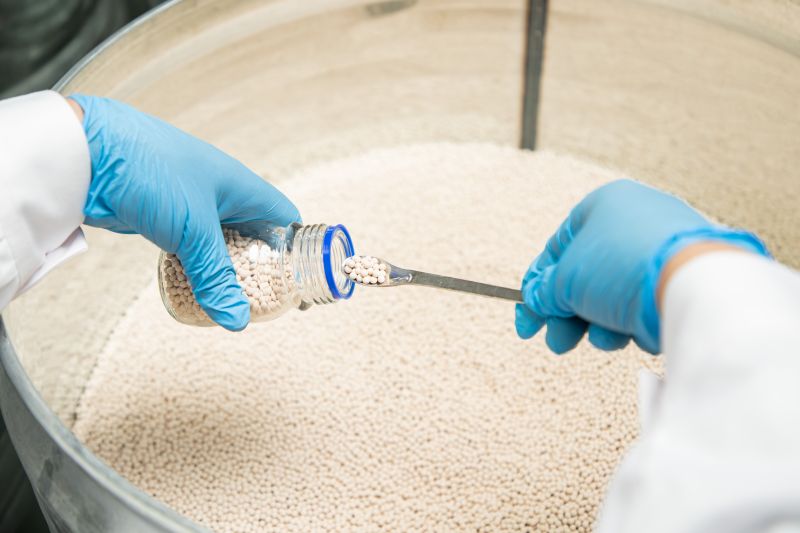
To sum up, the different particle sizes of molecular sieves have a significant impact on the application. Therefore, when using molecular sieves, it is necessary to choose the appropriate particle size according to different application requirements to achieve the best results.